
Комплексные химические добавки в кассетной технологии производства железобетонных изделий
Использование химических добавок — органических пластификаторов н неорганических электролитов — ускорителей твердения бетона дает реальные возможности дальнейшего повышения качества бетонных изделий кассетной технологии и повышения их экономичности
Особенно большого эффекта следует ожидать от введения в бетон комплексных добавок поверхностно-активных веществ л электролитов, включающих в себя положительные свойства отдельных составляющих Но если влияние отдельных добавок поверхностно-активных веществ и электролитов на твердение бетона изучено достаточно широко, то вопрос об их совместном действий мало исследован Изучением этого вопроса занимаются кафедра строительных материалов ГИСИ, Горьковский завод КПД № 2 и кафедра технологии производства строительных материалов ВЗИСИ.
Выполненные в 1965—1968 гг. лабораторные и производственные эксперименты показали высокую эффективность комплексной добавки ССБ+СаС12, позволяющей на 10—12% снизить расход цемента без уменьшения прочности бетона. Однако повышенная агрессивность хлорнонов по отношению к арматуре и металлу форм может несколько ограничить применение таких добавок. В этом отношении более предпочтительны сульфатсодержащие добавки, так как агрессивность сульфат-ионов значительно ниже, и, кроме того, в процессе твердения они связываются в практически нерастворимые соединения типа гидросульфоалюминатов кальция. Поэтому авторами были проведены специальные исследования, посвященные изучению комплексной добавки CCB + Na2S04 на свойства Сетонов кассетной технологии. Параллельно велись опыты с комплексной добавкой ССБ+СаС12.
В качестве вяжущего использовались применяемые на заводе КПД-2 высокоалитовые низкоалюмннатные портлаидцеменгы Алексеевского завода марки 400 и завода «Большевик» марки 500 по ГОСТ 10178—62, химико минералогическая характеристика которых приведена в табл. 1
На первом этапе было исследовано чисто пластифицирующее действие добавок на цементное тесто, которое определялось по изменению нормальной густоты теста При введении в него добавок. При этом, если водопотребность цемента завода «Большевик» (нормальная густота 26%) соответствовала требованиям кассетной технологии (до 27%), то цемент Алексеевского завода (нормальная густота 29,50%) не вполне соответствовал им.
Одновременно проверялись сроки схватывания цементного теста с целью изучения влияния добавок на допустимый период укладки бетона в кассету. Результаты опытов сведены в табл. 2.
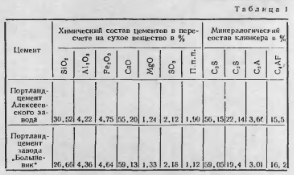
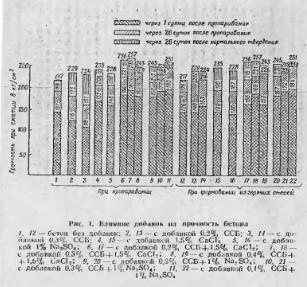
Значительное снижение водопотребпостн цементов при использовании комплексных добавок позволяет в целом ряде случаев эффективно применять при изготовлении изделии и кассетах цементы, не вполне удовлетворяющие оптимальным требованиям для кассетной технологии, как эго имеет место на примере цемента Алексеевекого завода.
При использовании комплексных добавок на 20—30% сокращается срок начала и до 13% — конца схватывания цементов. При этом, как правило, сохраняется возможность качественного уплотнения бетонной смеси и кассете.
Исследования нарастания прочности бетонов проводились при двух видах тепловой обработки: чаропрогреве и формовании из разогретой смеси. В первом случае применялись бетонные смеси с осадкой стандартного конуса С—8 см.
При формовании образцов из горячем смеси водопотребность увеличивалась на 10—15%. Начальная подвижность в том случае была 15—22 см, но к концу формования составляла 6—8 см.
В соответствии с условиями твердения бегона в кассетах формы с образцами-кубами 15X15X13 см при тепловой обработке пригружались равномерно распределенной нагрузкой 100—120 г/см’2. Образцы пропаривались без предварительной выдержки по режиму ч 3 ч подъем температуры, 4 ч изотермическая выдержка и 2 ч остывание в форме. Образцы, изготовленные из разогретой до 85—90°С смеси, выдерживались 1,5 ч при температуре 65—70°С, после чего подвергались дополнительной кратковременной тепловой обработке паром по режиму: 1 ч подъем температуры от 65—70°С до 85—90°С, 4 ч изотермическая выдержка и 2 ч остывание в форме.
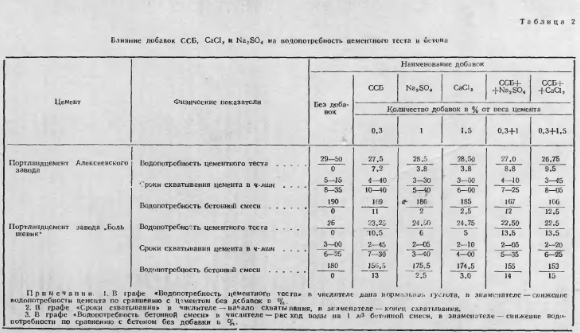
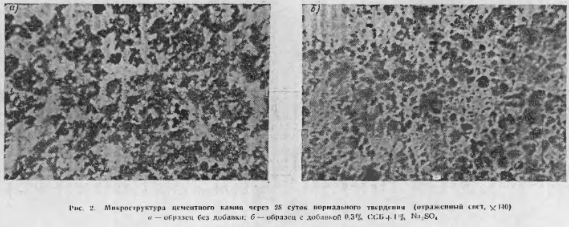
Испытание образцов проводилось через сутки после изготовления (что соответствовало обычному времени выдержи ил- кия кассетных изделий в цехе, принятому на заводе КПД № 2) и в 28-дневном возрасте. В качестве контрольных изготавливались образцы из бетонной смеси с подвижностью 6— S см, которые испытывались в 28-дневном возрасте после твердения в нормальных условиях. Контрольные образцы из бетонной смеси с подвижностью 15—22 см не изготавливались, так как бетон, приготовленный из горячей смеси, после укладки в форму имел подвижность 6—8 см.
Комплексные добавки вводились в количестве, рассчитан ном как оптимальное из условий пластифицирования бетонной смеси (соответственно 0.2—0,3% ССБ+1,5% СаС12 и 0,2— 0,3% ССБ-г 1% Na2SC>4 от веса цемента) Кроме того, применялись комплексные добавки, содержащие повышенный по сравнению с оптимальным расход ССБ.
Результаты испытании, приведенные на рис. 1. показывают, что оптимальным расходом добавки ССБ, применявшейся в комплексе с СаСЬ, из условия получения наилучших прочностных показателен при пропаривании является 0,25—0,30% от веса цемента, а при применении комплексной добавки ССБ+ + Na2SC>4 соответственно 0,3—0,35%. Такие добавки позволяют на 17—32% повысить прочность пропаренного бетона на всех стадиях его твердения или на 8—14% сократить расход цемента в бетоне без снижения его прочности. Аналогичные результаты получаются и для образцов нормального твердения. Более высокое оптимальное содержание добавки ССБ в случае применения ее с сульфатом натрия вместо СаС1, по- видимому, можно объяснить более энергичным разрушающим действием сульфата натрия на адсорбирующиеся на зернах цемента пленки ССБ.
При формовании изделий из разогретой смеси оптимальный расход добавки ССБ может быть еще больше: 0,3—0,35% от веса цемента — при использовании ее в комплексе с СаС12 и 0,35—0,4% для добавки CCB+Na2SC>4 что объясняется, по- видимому, резким падением прочности адсорбированных иа зернах цемента и его новообразований коллоидных пленок сульфитно-спиртовой барды при применении предварительно разогретого бетона. Прочность бетона при этом повышается иа 25—43%; при сохранении же прочности бетона неизменной создается возможность экономии на 10—17% расхода цемента.
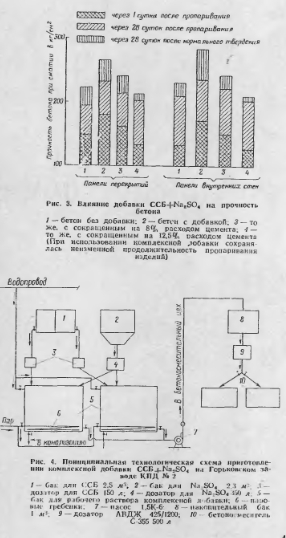