
Мелкозернистый пневмобетон и его применение
При возведении тонкостенных конструкций ИЛИ в специальных работах (при замоноличивании стыков сборных сооружении, нанесении гидроизоляционных покрытии) целесообразно применять мелкозернистые песчаные бетоны. Учитывая особенности таких бетонов, необходимо использовать специфические способы их укладки и уплотнения, существенно улучшающие физико-механические свойства. Свойства мелкозернистых бетонов улучшаются и при рациональной технологии их нанесения путем пневмонабрызга.
Сущность этой технологии в том, что приготовленная в обычном смесителе мелкозернистая бетонная смесь с помощью переоборудованного по прямоточной схеме растворонасоса нагнетается в рабочей трубопровод (рис. 1). По выходе из растворонасоса смесь поступает в смесительную камеру установки, куда одновременно с ней по специальному шлангу от компрессора подается сжатый воздух при 7 ати. Таким образом, транспортировка смеси по трубопроводу и нанесение ее на обрабатываемую поверхность происходит под воздействием струи сжатого воздуха. Расход его в зависимости от производительности установки (от 1 до 6 м3/час) составляет до 3—6 м3/мин. При обычных режимах транспортирования, характеризуемых показателем концентрации растворовоздушной смеси смесь в трубопроводе находится во взвешенном состоянии.
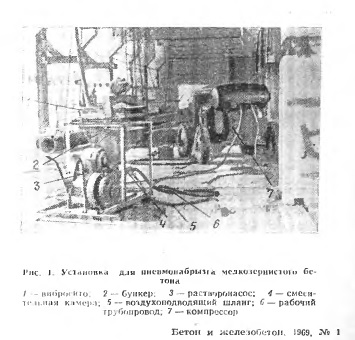
Для выяснения особенностей технологии, установления оптимальных технологических параметров и выявления физико-механических свойств мелкозернистого пневмобетона в ЦНИИ организации, механизации и технической помощи строительству Госстроя СССР была проведена специальная работа. В опытах использовали специальную установку (рис. 2). Были применены портландцемент М500 активностью 557 кг/см2 и 2 вида песка: крупный Дровинского месторождения с Мкр—3,11 и мелкий Вольского месторождения с Мкр-1,63. Испытания проводились на смесях следующих составов (по объему) 1:1, 1:2, 1:3, 1:4. Подвижность смесей по конусу СтройЦНИЛа 10 см, значения ВЩ соответственно 0,405, 0,5, 0,612; 0,755.
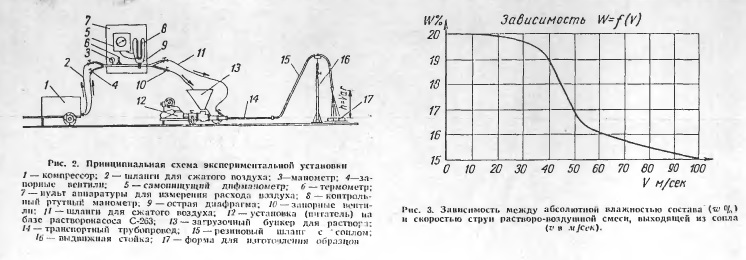
Исследования позволили установить, что данная технология улучшает свойства транспортиру слой цементно-песчаной смеси, удаляя значительную часть воды из смеси при нанесении ее в конструкцию и интенсивно уплотняя смесь за счет высокой кинетической энергии растворо-воздушной смеси и аэродинамического давления струн, выходя щей из сопла установки. Наносимый материал по физико-механическим свойствам существенно отличается от исходного затворяемого цементно-песчаного раствора и практически равноценен высококачественному мелкозернистому бетону.
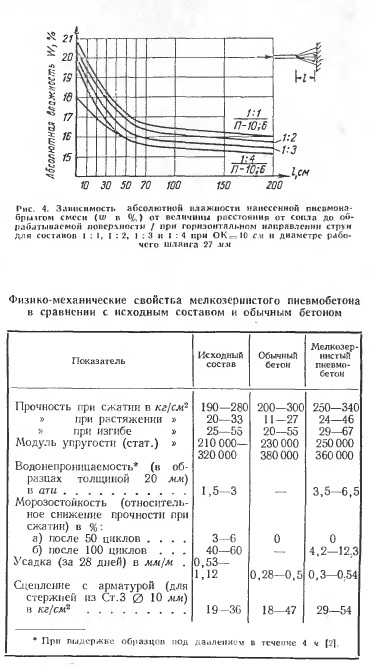
П. П. Шиповскпй и И. И. Шаров установили, что при транспортировании и нанесении смеси из нес удаляется до 15—23% воды затворения. Исследования показали, что основная масса воды удаляется из смесн в результате частичной сепарации последней при нанесении вместе с массой воздуха. Небольшая часть воды испаряется в транспортирующем воздухе, когда он имеет повышенную температуру.
Частичное обезвоживание смеси зависит от степени взвешивания смеси в воздухе и степени ее сепарации при нанесении. При недостаточном количестве подаваемого воздуха смесь взвешивается лишь в незначительной степени и из нее удаляется малое количество воды. При избытке подаваемого воздуха смесь подвергается чрезмерной сепарации, из нее отделяется не только вода, но частично и цементное тесто, что нежелательно.
Исследования позволили установить зависимость между степенью водоудаления и скоростью струи растворо-воздушной смеси на выходе из сопла (рис. 3). В этих опытах использовали состав 1 : 3 на песке с Мкр—3,11. Как видно из рис. 3, с увеличением скорости струи абсолютная влажность нанесенной смеси уменьшается. При скорости от 30 до 50 м/сек совершается переход смеси во взвешенное состояние в воздушной струе.
Поскольку чрезмерное увеличение скорости струи смеси связано с увеличением расхода воздуха и приводит к излишней сепарации растворовоздушной смеси оптимальными скоростями следует считать 50—60 м/сек. В этом случае обеспечивается достаточно высокая степень обезвоживания наносимой смеси. Такие скорости обычно создаются при применении растворо-воздушной смеси.
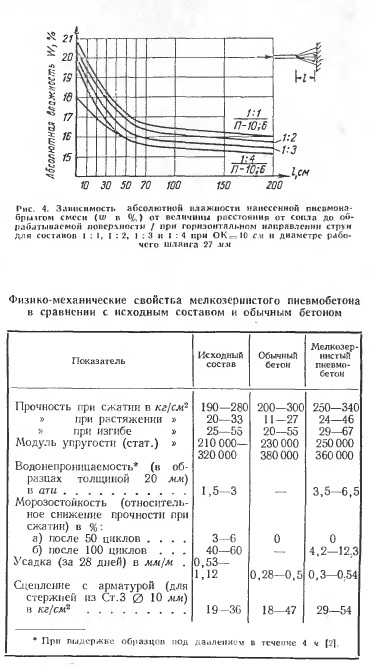
Указанные параметры процесса являются оптимальными. Свеженанесенная смесь обладает мини мальным воздухововлечением (0,6—1,2% по объему), степень ее уплотнения практически не отличается от таковой для составов, уплотненных вибрацией.
На качество наносимого пневмобетона также оказывает влияние правильный выбор расстояния от сопла до обрабатываемой поверхности. При недостаточном удалении сопла от поверхности исчезает эффект частичного обезвоживания смеси, плотность ее при укладке понижается. При слишком большом расстоянии выбрасываемая из сопла струя из-за сопротивления воздуха теряет значи тельную часть кинетической энергии, вследствие чего плотность укладки раствора также снижается.
Как видно из графика (рис. 4), по мере увеличения от 0 до 80 см влажность смеси резко снижается, а при дальнейшем росте — остается почти постоянной. Таким образом, величину = 80—90 см для рассматриваемого случая следует считать оптимальной.
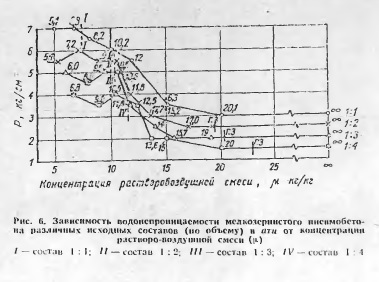
На рис. 5 показана зависимость 28-дневной прочности мелкозернистого пневмобетона при сжатии (RCM) в функции от показателя концентрации растворо-воздушной смеси — р при = 80 см. Для всех составов смеси (кроме 1:1) оптимальная величина р составляет 11.
Параллельно с испытанием образцов из мелкозернистого пневмобетона в ряде случаев изготовлялись и испытывались образцы из обычного тяжелого бетона. При оптимальных технологических режимах мелкозернистый пневмобетоп по всем основным физико-механическим показателям значитель-но препосходит исходную растворную смссь, уплотненную вибрированием.
Данные таблицы спидегельешуют об относительно высоких физико-механических характеристик мелкозернистого пневмобетона, особенно при использовании песков с зерновым составом.Замена крупного песка мелким (Мкр =1,63) снижает прочность получаемою пневмобетона при сжатии на 10—15%, но приводит к возрастанию прочностей при растяжении и изгибе на 10—20% и увеличению усадочных деформаций в 1,2 раза.
Достаточно высокие физико-механические показатели мелкозернистого пневмобетона удачно сочетаются с практическими преимуществами новой технологии. С помощью относительно простой по конструкции установки решаются одновременно три главных технологических задачи: приготовление смеси, ес транспортирование, укладка смеси в конструкцию и се уплотнение. Все это обеспечивает удобство выполнения ряда работ, минимальную трудоемкость н стоимость их по сравнению с обычной технологией, основанной па применении вибрирования.
Особенно ощутимы преимущества технологии мелкозернистого пневмобетона при выполнении специальных работ, характеризующихся сравнительно малыми объемами и выполняемых на широком фронте, например при замоноличивании стыков сборных сооружений или нанесении гидроизоляционных покрытий. Ее применение также целесообразно при возведении различных тонкостенных сооружений в промышленном и гражданском строительстве: резервуаров, покрытий и т. д. Для обеспечения плотной укладки смеси в тонкостенные армированные конструкции ее наносят слоями с поперечным изменением угла наклона сопла к поверхности до 45%.
Рассматриваемый способ имеет существенные преимущества и перед обычным торкретированием, так как позволяет осуществлять непрерывность и равномерность технологического процесса, соблюдать постоянство состава укладываемой смеси. При бетонировании конструкции подачу мелкозернистых смесей производят на расстояние 100 м по горизонтали и 20 м по вертикали. К достоинствам нового способа следует также отнести отсутствие пыленпя при нанесении раствора.
Практика показала, что применение мелкозернистого пневмобетона при омоноличивании стыков сборных железобетонных конструкций является весьма эффективным решением. На строительстве цеха выпарки Уфимского химического завода при заделке стыков сборных элементов был применен мелкозернистый пневмобетон. Работа выполнялась Главсредневолжскстроем при участии ЦНИИОМТП. Производительность установки, обслуживаемой 4 рабочими, достигла 1,1—1.2 м3/час. Для получения в стыках бетона М200 был применен исходный состав смеси 1:3 (по объему). Использовались портландцемент М400 и песок с зернами крупностью до 7 мм и Мкр =2,9. Испытания бетона в стыках показали, что его 28-дневная прочность на 29—32% превосходит прочность исходного раствора.
Эта же технология применялась при замоноличивании стыков сборных железобетонных элементов в тресте Стальмонтаж в г. Салавате на строительстве многоэтажного промышленного корпуса нефтехимического комбината № 18, в Москве при возведении многоэтажного крупнопанельного здания на ул. Чкалова. Технико-экономический анализ эффективности применения новой технологии замополичивания стыков по ряду объектов показал, что по сравнению с обычной технологией, основанной на применении вибрирования и подачи бетонной смеси башенным краном, стоимость работ сокращается примерно в 2—2,5 раза, трудоемкость и 3—3.5 раза, стоимость I мг бетона снижается примерно и 3 раза.
Накоплен опыт применения мелкозернистого ннсвмобстона при бетонировании основных конструкций монолитных железобетонных резервуаров.
Натурные исследования, проведенные и 1965 т. трестом Спецжелезобетонстрой при участии ЦНППОМТП на строительстве ТЭЦ-21 в Москве, показали, что обладая высокой прочностью, водонепроницаемостью и морозостойкостью, мелкозернистый пневмобетон может быть применен при возведении монолитных сооружении, работающих в сложных эксплуатационных условиях (покрытия, градирни, вентиляционные башни н т. п.). Это подтверждает опыт применении мелкозернистого пневмобетона трестом Мосэлсктротягстрой в строительстве тонкостенных монолитных покрытии здании и сооружений [5].
Технология мелкозернистого пневмобетона может найти рациональное применение в таких работах, как частичное восстановление и добетонирования железобетонных конструкций, устройство подливок при укладке плит покрытий дорог, аэродромов и т. д.
В 1966 г. мелкозернистый ппевмобетон в больших масштабах был успешно приманен СУ-134 треста Мосстрой 16 Главмосстроя при участи ЦНИИ-ОА1ТП на строительстве Главного вычислительного центра Госплана СССР при заделке стыков сборных железобетонных элементов здания, а также при обетонироваинн металлических подвесных тонкостенных конструкций (подвесок) и добетонировании колонн по периметру слоем до 8 см.
В 1966—1967 гг. способ пневматического бетонирования успешно применялся при восстановлении зданий и сооружений в Ташкенте.
Выводы.
Мелкозернистый бетон, получаемый при транспортировании и нанесении цементно-песчано-водной смеси в струе сжатого воздуха, обладает высокими физико-механическими показателями и в ряде случаев может успешно заменять обычный бетон. Улучшение свойств мелкозернистого бетона, наносимого пневмоспособом, происходит за счет удаления части влаги из смеси при набрызге н эффективного уплотнения при нанесении смеси при большой скорости струн.
Обеспечивая комплексное решение приготовления, транспортирования, укладки и уплотнения смеси, технология мелкозернистого пневмобетона во многих случаях, особенно при выполнении работ сравнительно малых объемов на широком фронте, оказывается значительно экономичнее других решений.
Технология мелкозернистого пневмобетона может найти выгодное применение при замоноличивании стыков сборных железобетонных зданий и сооружений; ремонтных, восстановительных и специальных работах; бетонировании монолитных тонкостепных железобетонных и армоцементных конструкций, в том числе обладающих повышенной водонепроницаемостью и морозостойкостью; нанесении гидроизоляционных покрытий.