
Применение воздухововлекающих добавок в производстве наружных стеновых панелей из керамзитобетона
Во ВНИИЖелезобетоне в течение нескольких лет проводились исследования по применению воздухововлекающих добавок при изготовлении керамзитобетопных изделии. Рекомендовано применять воздухововлекающие добавки (СНВ, ЦНИПС-1, различные пенообразователи), в першую очередь, для поризации смеси с вовлечением в нее до 12% воздуха. Это позволяет не только пластифицировать смесь, но уменьшать в ее составе содержание песка, заменив его частично мелкораздробленными воздушными пузырьками, равномерно распределенными в растворной составляющей бетона. Расход керамзитового песка снижается на 0,1—0,2 м3/м3, общий расход керамзита — до 1,3 -Р 1,5 м3/м, а объемный вес керамзитобетона на 50-М50 кг/м3. Появляется возможность выпускать -изделия требуемого объемного веса при использовании утяжеленного керамзита, так как благодаря пластификации смеси отпадает необходимость применения пригруза, уменьшается трудоемкость процесса формования, повышается производительность технологических линий.
Поризация смеси воздухововлекающими добавками позволяет во многих случаях заменить дробленый керамзитовый песок обычным -кварцевым без увеличения объемного веса бетона. Расход кварцевого теска -по весу остается таким же, как и при обычном керамзитобетоне, а по объему уменьшается До 0,15—0,2 m3Jm3 с заменой недостающего объема вовлеченным воздухом. Расход керамзитового гравия составляет 1—1,2 м3 на 1 м3 бетона. Благодаря уменьшению расхода пористого песка млн замене его кварцевым снижаются водопотребность бетонной смеси и отпускная влажность изделий.
Изучены факторы, влияющие на поризацию смесей при введении воздухововлекающих добавок, установлены оптимальные режимы приготовления, формования и ускоренного твердения поризованных керамзитобетонов, их основные физико-механические свойства — прочность, деформ ативность, теплопроводность, долговечность. Параллельно с исследованиями проведены работы по внедрению технологии в производство. На основании исследований и результатов внедрения технологии на заводах Главмоспромстройматериалов (Бескудниковском комбинате строительных материалов и конструкций № 1, заводах КС Б № 20 и ЖБИ № 21) разработаны и выпущены инструкции по использованию добавок [1, 2]. Введение добавок предусмотрено утвержденными Госстроем СССР ГОСТ 11024—-64 на керамзитобетон-иые стеновые панели и типовыми нормами расхода цемента СИ 386-68.
Выпуск нормативной и инструктивной литературы позволил перейти к массовому внедрению технологии, которая получила широкое распространение в последние три года. В настоящее время воздухововлекающие добавки применяются при изготовлении керамзитобетонных стеновых панелей более чем на 50 заводах страны с годовым объемом производства более 1,5 млн. м3.
С применением воздухововлекающих добавок изготовляют панели для жилых домов (серий 1-464, 1-467, 1-335, 11-49, 1МГ-600 и др.), промышленных и общественных зданий. При этом существенно снижается стоимость панелей. Только за счет уменьшения расхода керамзита стоимость 1 м3 керамзитобетона снижается на 0,5—2 руб. при работе на керамзитовом песке п на 1,5—6 руб. при замене керамзитового песка кварцевым. Благодаря этому в 1968 г. годовой экономический эффект составил более 2 млн. руб.
Однако несмотря на массовый характер применения воздухововлекающнх добавок при производстве керамзитобетонных изделий и более, чем пятилетний успешный опыт эксплуатации сотен здании с наружными стенами из керамзитобетона с воздухововлекающими добавками в печати [3, 4] и публичных выступлениях даются категоричные рекомендации по ограничению воздухововлечеиия до 5%. Мотивируется это опасением снижения долговечности, теплофизических и других свойств керамзитобетонов.
В связи с этим представляется необходимым более подробно остановиться на влиянии воздухововлекающих добавок и (вовлеченного воздуха на свойства керамзитобетона. Известно, что с увеличением вовлеченного воздуха прочность бетона вследствие снижения плотности уменьшается. В тяжелых, а также конструктивных легких бетонах это снижение до известных пределов компенсируется уменьшением водоцементного отношения, благодаря эффекту пластификации смеси, который возрастает с уменьшением расхода цемента. Отсюда и рекомендации об ограничении воздухововле- чения 3—5%, хотя, например, ГОСТ 4797—64 допускает для повышения долговечности гидротехнического бетона введение воздухововлекающих добавок в количестве до 12%.
В конструктивно-теплоизоляционных керамзитобетонах прочность с увеличением объема вовлеченного воздуха также снижается, однако при этом снижается и объемный вес бетона. Поэтому допустимой является такая степень воздухововлечеиия, которая обеспечивает требуемую прочность бетона. Чем ниже марка бетона, выше прочность применяемого керамзита, песка и цемента, больше продолжительность твердения, тем, естественно, и больше может быть процент вовлеченного воздуха. Важно при этом подчеркнуть, что хотя, по сравнению с керамзитобетоном плотной структуры, керамзитобе- точ, поризованный воздухововлекающими добавками, имеет меньшую прочность (и меньший объемный вес), при данном объемном весе бетона и неизменном сырье наличие вовлеченного воздуха не снижает прочность (рис. 1). Однако равнопрочный бетон без добавок имеет при этом неплотную водопроницаемую структуру, не защищающую арматуру от коррозии.
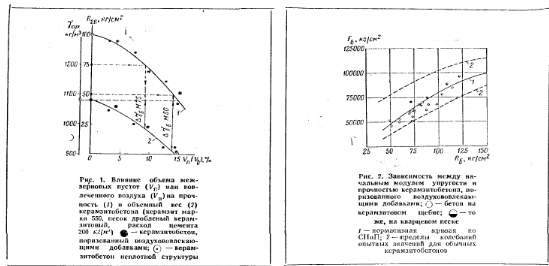
Лишь при очень большом воздухововлечении (20% н более) ухудшаются адгезионные свойства порнзованного раствора и это приводит к снижению прочности поризованного керамзитобетона, по сравнению с бетоном неплотной структуры. Однако такие составы на практике не применяются.
Начальный модуль упругости керамзитобетона, поризованного воздухововлекающими добавками, отвечает нормативным требованиям (рис. 2); отклонения не выходят за пределы разброса, как в опытах с обычными керамзитобетонами. Причем все они относятся к бетонам марок 75—100 с небольшой степенью воздухововлечеиия.
Известно, что замена пористого песка плотным всегда повышает модуль упругости. Поэтому поризованные керамзитобетоны на кварцевом песке имеют повышенный модуль упругости, в основном превышающий требования СНиП.
Особое внимание в проведенных исследованиях уделено теплопроводности керамзитобетона, ионизованного воздухововлекающими добавками. При неизменном керамзите и данном объемном весе бетона поризацния воздухововлекающими добавками н замена керамзитового песка кварцевым не влияет на теплопроводность бетона (или раствора) в сухом состоянии (рис. 3,а). Бетоны плотной структуры в ряде случаев характеризовались меньшим значением Хсух , чем порнзованные того же объемного веса. Но специально поставленные опыты показали, что это объясняется не различиями в структуре бетона, а тем, что для получения бетона плотной структуры того же объемного веса был применен более легкий из хорошо вспучиваемых глин керамзит, обладающий значительно меньшим коэффициентом теплопроводности. Порнзованные керамзитобетоны на таком керамзите также имели меньшие значения объемного веса и коэффициента теплопроводности. Существенно, что даже для бетонов, приготовленных на керамзитах с худшими теплофизическими свойствами, коэффициенты теплопроводности при равновесной влажности отвечают нормам СНИП (рис. 3,6).
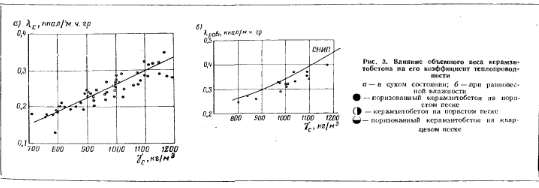
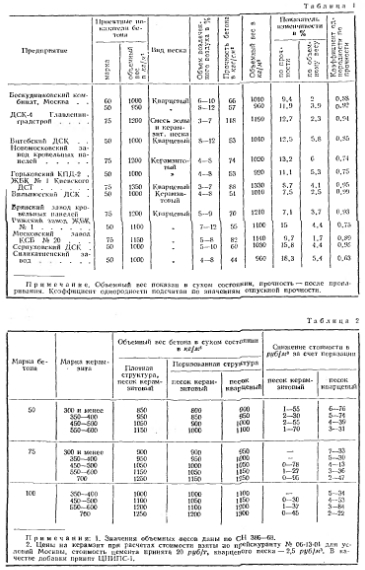
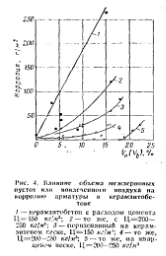
Замкнутый характер пористости керамзитобетона, полное заполнение поризованным раствором всех межзерновых пустот в крупном заполнителе создают плотную структуру, обеспечивающую при соответствующем расходе цемента (не менее 200 кг/м3) защиту арматуры от коррозии (рис. 4). При одном и том же объеме пор в бетоне (одинаковом объемном весе) поризация воздухововлекающими добавками в 5—6 раз снижает степень коррозии арматуры.
Приведенные в табл. 1 данные свидетельствуют также о достаточно низких значениях показателен изменчивости прочности и объемного веса поризованного керамзитобетона. Коэффициент однородности по прочности во всех случаях выше 0,6. На многих заводах введение добавок существенно повысило однородность бетона. По данным ряда предприятий, где ведется постоянный контроль за объемом вовлеченного воздуха, его колебания составляют ±2%- Таким образом, и Данные многолетних исследований н опыт производства свидетельствуют о безусловной допустимости применения воздухововлекающих добавок для поризации керамзитобетонных смесей. Ограничение воздухововлечения 5% в случаях, где но условиям прочности процент поризации может быть повышен, использование воздухововлекающих добавок только для пластификации смесей, применение добавок в сочетании с интенсивной. это, накопленный опыт и ориентирует производство
Применение воздуховоолекающих добавок и соответствии с разработанной ВНИИЖелезобетоном технологией и инструктивным и документами дает возможность существенно повысить качество изделий (снизить объемный вес, увеличить плотность структуры); уменьшить расход дефицитного керамзита; отказаться во многих случаях от дробления песка; снизить стоимость продукции; организовать выпуск изделии с требуемыми -показателями при наличии тяжелых заполнителей; значительно упростить процессы формования и решить ряд других задач, актуальных для современного индустриального строительства.
Как видно из табл. 2, применение керамзитобетона, поризованного воздухововлекающими добавками, вместо керамзитобетона плотной структуры целесообразно для всех случаев производства панелей. Исключение составляет лишь производство панелей из бетона пониженного объемного веса на относительно тяжелых (марок 600—700) и дорогих керамзнтах, где более эффективно использование беспесчаных керамзитобетонов, поризованных пеной или газообразователямн, а также изготовление панелей с полной немедленной распалубкой или коротким 6—8-часовым режимом термообработки.
Однако в последнем случае при сочетании поризации добавками с электроразогревом смеси до температуры 70—80° С и последующим активным термосным выдерживанием в течение 4—6 ч, также целесообразно применение керамзитобетона, поризованного воздухововлекающими добавками. Такая технология, ускоряя схватывание поризованных смесей устраняет и другой их «недостаток» — малую жесткость, которая в ряде случаев препятствует заглаживанию верхней поверхности панелей, выемки проемообразователей и выполнению других операций немедленно после формования изделий. Возможность горячего формования изделий из поризованных керамзитобетонных смесей подтверждена исследованиями ВНИИЖелсзобетола, ГИС11 нм. Чкалова н производственным опытом Бескудниковского комбината и Серпуховского и Горьковского ДСК.
Выводы
Поризация керамзитобетонных смесей воздухововлекающнмн добавками в соответствии с рекомендациями, изложенными в конструктивных документах ВНИИЖелезобетона, позволяет существенно улучшить качество и экономику керамзитобетонных стеновых панелей, не ухудшая физико-механических свойств.
Допустимый объем воздухововлечения в керамзитобетоне зависит от -применяемых материалов, марки бетона и конкретных условии производства н -в пределах до 12—15% обусловлен лишь достижением необходимой прочности бетона и требуемых свойств смеси.
В качестве мелкого заполнителя при производстве керамзитобетонных панелей с воздухововлекающими добавками мо-гут использоваться и плотные, и пористые пески, в зависимости от местных условий.
Рекомендации применять воздухововлекающие добавки при производстве керамзитобетонных панелей только для пластификации смеси с ограничением степени воздухововлечения до 5% необоснованны, не вытекают из результатов каких-либо исследований и не должны приниматься во внимание при организации производства керамзитобетонных панелей.