
Оптимальный состав бетонной смеси, подвергаемой вакуумированию
Для приготовления мелкозернистого бетона применяют портландцемент в шлакопортландцемент марок 300, 400 и 500, обогащенные пески Вяземского карьера с модулем крупности не менее 2,75 е содержанием пылевидных, илистых частиц, определяемых отмучивавшем, не более 2% но весу (в том числе глины не более 0,.25-%). С целыо уменьшения расслаиваемость бетонной смеси при перевозке автотранспортом и облегчения подачи бетононасосами вводится пластифицирующая добавка СДБ в количестве 0,05% цемента. При отрицательной температуре наружного воздуха бетонная смесь готовится на подогретых материалах. Температура смеси в момент отпуска с завода зависит от температуры внешней среды и колеблется от 10 до 30°С.
Составы бетона на портландцементе марки 400: для бетона марки 200 — 3,6 с расходом цемента 425 кг/м3; для бетона марки 300 — I : 2,7 расходом цемента 525 кг/м3.
Однородность прочности мелкозернистого бетона за 1970—1972 гг., характеризуемая -коэффициентом вариации, для бетона марки 200 составила 8,1%, для бетона марки 300 — 6,8%.
Значения переводного коэффициента от прочности IB кубах с ребром 10 см к стандартной прочности кубов с ребром 20 см для мелкозернистых бетонов нормального твердения в 28-суточном возрасте равны единице.
Сопоставление мелкозернистого бетона с обычным по призменной прочности проведено на образцах-призмах размером 20X20 x 80- см « образцах-кубах 20Х100Х20 см, изготовленных в заводских условиях, показало, что отношение призменной прочности к кубиковой у мелкозернистого бетона составляет 0.8S и 0,89, тогда как у обычного оно равно только 0,68 и 0,72, т. е. ниже на 18%.
По величине снижения прочности призм от внецентренного приложения нагрузки и по характеру их разрушения, при центрально и внецеитренно приложенных нагрузках отличий я работе мелкозернистого бетона от обычного не обнаружено.
Более Высокий коэффициент призменной прочности мелкозернистого бетона указывает навозможность внесения соответствующей поправки при расчете конструкций, что существенно должно снизить расход цемента.
Каждому методу и интенсивности уплотнения соответствует оптимальным состав бетонной смеси. Метод вакуумирования имеет свои особенности, и потому бетонная смесь, не может быть рациональной также при вакуумировании). Это известное общее положение подтверждается и многочисленными экспериментами по вибровакуумираванию.
Если в процессе вакуумирования атмосферное давление будет передано только на каркас («скелет») из крупного заполнителя, a не нарастворную составляющую, то уплотнение бетонной смеси будет неполным; это имеет место при недостатке растворной составляющей. Поэтому эффективное уплотнение достигается при условии, если внешнее (атмосферное) давление в процессе вакуумировашия будет передано вакуум-щитом на бетонную смесь через растворную составляющую. Из этого следует, что плотный вакуум-бетон должен иметь «бесконтактное», базальное строение, а бетонная смесь должна содержать определенный избыток растворной составляющей (при оптимальном Лизе). Должно быть учтено, что в процессе вакуумирования изменяются состав и объем растворной составляющей (меняется Кизб, остается неизменным соотношение П/Щ).
В первых опытах применялись равноподвижиые бетонные смеси состава 1 : 5,5 с расходом цемента около 350 кг/м3, различавшиеся соотношениями и расходом воды. Использованы партлаэдцемент марки 400,мелкий днепровский песок (Л4=1,3) и гранитный щебень фракции 10—20 мм. Опытные образцы-плитки (150Х150Х70) формовали вибрационным способом и вибровакуумированием. Перед вакуумированнем бетонную смесь вибрировали в форме 15 сек.
Данные показывают (рис. 4) значительное увеличение объемной массы и прочности для всех составов вакуум-бетона. Оптимальное соотношение, обеспечившее наибольшие объемную массу и прочность вакуум-бетона, на 27% выше против виброуллотненного бетона при этом оказался выше на 16%.
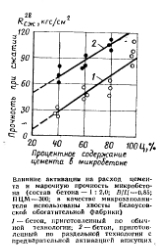
Эффективность составов бетона и самого процесса уплотнения при вакуумировании не может характеризоваться количеством извлекаемой воды, недостаточна характеристика и п-о одной величине уменьшения объема омеси. Уменьшение объема должно рассматриваться в овязи с количеством извлеченной воды,например -в виде их соотношения, названного нами коэффициентом эффективности вакуумироваиия (уплотнения при вакуумировании):
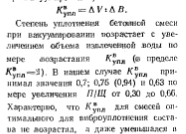
Опыты показывают, что по мере увеличения содержания цемента от 220 до 460 кг/м3 снижается для оптимальных виброуплотненных смесей от 0,5 до 0,36, а для вакуумбетонов от 0,67 до 0,42, оставаясь при этом выше па 19—40% Дри расходах цемента до 400 кг/м3. Увеличение расхода цемента сверх 450 кг/м3 -вызывает -сближение оптимальных значений П/Щ для обоих видов бетона и различие в нашем случае не превышало 10—,15%.
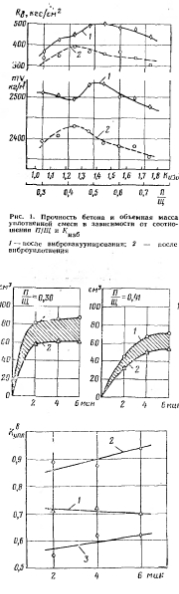
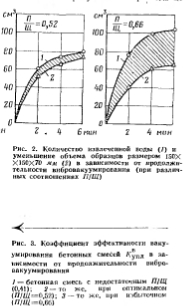
Значительное различие п содержании песка для вакуум-нровянного и вибрированных бетонов оптимальных составов обусловливает существенную разницу значений коэффициента избытка растворной составляющей. |Прн этом бетонные смеси, уплотняемые вакуумирова- мием, характеризуются двумя значениями Кизс, — до и после накуумиронап.ия (рис. 5).
При сравнении, способов вакуумирования более эффективным оказалось вакуумbровапие снизу, при вакуумировании сверху был меньшим. Вакуумвро- вание снизу обеспечивает лучшее уплотнение смеси (повышение объемной массы), хотя количество извлеченной воды в этом случае меньше (рис. 6). Оптимальное значение П/Щ постоянное (0,58) при заданном расходе цемента (330 кг/м3) и не зависит от способа вакуумирования.
Просос воздуха прн вакуумировании снизу исключается посредством многократного вибрирования в процессе вакуумирования. Количество извлеченной воды зависит от состава бетонной смеси и режима пибровакуумиравания. Рациональный режим и оптимальный состав смеси обеспечивает удаление воды до 30% и надлежащее уплотнение. Остающееся в бетонной смеси количество воды соответствует показателю жесткости омеси порядка 300—400 сек.
Основные свойства вакуум-бетон а — прочность, водонепроницаемость, водопоглощение, капиллярный подсос, усадка, набухание и морозостойкость, — как показали наши исследования, находятся на уровне соответствующих показателей для бетона из смесей с жесткостью 300—400 сек, хорошо уплотненных вибрацией с пригрузом.
Столь высокие показатели достигаются при двух обязательных условиях: оптимальном составе бетонной смеси и рациональном режиме вибровакуумировании. Исследования показали, что тонне хотя бы одного из этих условий ухудшает процесс уплотнения.
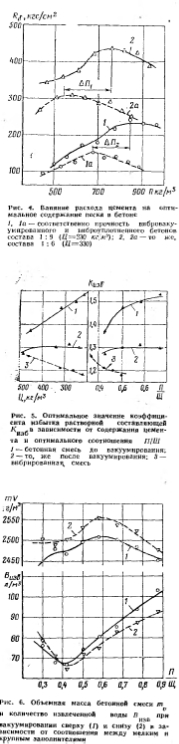
Рациональный режим вакуумирования включает: применение многократного вибрирования по 5—15 сек в ходе вакуумирования и снижение до 0,2—0,3 при вибрировании что исключает защемление смеси. Применением такого режима для уплотнения Малоподвижных смесей (OK=3-f-5 см) достигнуто увеличение прочности бетона на 60%, водонепроницаемости в 2 —2,5 раза
Выводы
Имеется принципиальное различие между бетонными смесями оптимальных составов, предназначенных для виброуплотнения для вакуумироваиия (вибропакууммрования).
Вакуумирование малоэффективно, если состав бетонной смеси оптимальный для виброуплотнения. Вакуум-бетон рационального состава характеризуется бесконтактным «плавающим» строением.
Вакуум-бетон оптимального состава отличается от виброуплотняемых увеличенным на 25—30% содержанием песка (ДЯ достигает 200 кг/м3, а соотношение П/Щ увеличивается на 20—40%).
Коэффициент избытка растворной составляющей уменьшается в процессе вакуумироваиия. Принципиально различные закономерности нзменен-ия оптимальной величины этого коэффициента в зависимости от расхода цемента для бетонных смесей, предназначенных для вакуумироваиия и виброуплотнения.
Применение оптимальных составов бетонных смесей в сочетании с рациональным режимом вибровакуумирования улучшает ход процесса уплотнения и качество вакуум-бетона. При этом основные свойства вакуум-бетона соответствуют показателям бетонов из смесей высокой жесткости порядка 300—400 сек, хорошо уплотненных вибрационным способом.
Данные выводы и рекомендации использованы при освоении производства объемных элементов (блок-комнат типа «колпак») на вибровакуумной формовочной машине МО.Б-УВ-1 в г. Кременчуге на ДСК-4 комбината «Кременчуг- строй».