
О давлении бетонной смеси на борта формовочных установок для изготовления объемных элементов
При проектировании и расчете формовочных установок для изготовления объемных элементов необходимо знать величину и закономерности давления бетонной смеси. При высоте слоя бетонной смеси 3 и более, а также площади стен до 20 м2 важно установить как статическое, так и динамическое давление смеси на борта формовочных установок.
Проводили исследования давления на борта формовочных установок четырех типов: на вибровакуумной машине, на установке кассетного типа, на машине непрерывного формования и на установке с подачей и укладкой бетонной смеси методом нагнетания.
Для определения величины давления использовали датчики мембранного типа и измерительную схему, разработанную в НИИСК.
Давление бетонной смеси на опалубку при изготовлении объемных элементов по методу вибровакуумирования определяли на фрагменте формующей установки.
Откидной борт установки представляет собой вакуум-щит. В неподвижном борте заподлицо с его поверхностью были установлены в специальные отверстия по высоте борта четыре датчика давления: нижний на -расстоянии 10 см от дна, остальные — на расстоянии 85 ом -один от другого.
Фрагменты объемного элемента высотой 275, шириной 68 и толщин-ой 4 ом изготовляли из бетонной смеси с подвижностью 19 см осадки по стандартному конусу.
Были проведены три серии экспериментов. В первой серии бетонную смесь заливали в форму и вакуумировали без дополнительного воздействия вибрации. Во второй серии при заливке в форму включали вибратор, установленный в нижней части вакуум-борта, а затем вакуум-насос. Третья серия экспериментов отличалась от второй тем, что в форму устанавливали сетку с размером ячейка 200Х200 мм и диаметром арматуры 4 мм.
Величину давления определяли в следующие моменты: после заполнения формы смесью; во время вакуумирования
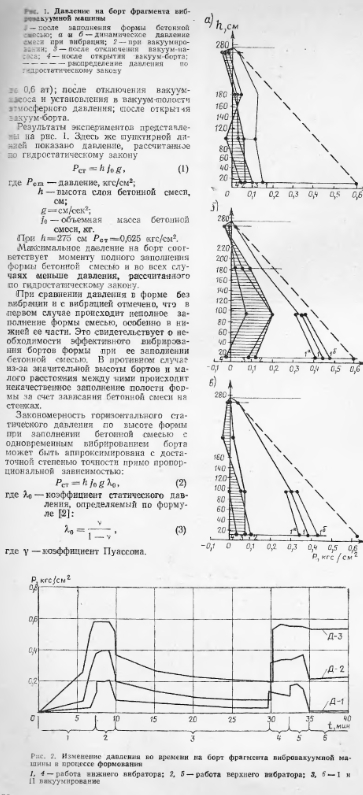
Для бетонных смесей по данным [з] у=0,42—0,49 и о=0,72—-0,96. С увеличением жесткости смеси значения у и А0 уменьшаются. На величину коэффициента статического давления влияет расстояние между стенками формы и степень армирования конструкции.
Так, во второй и третьей сериях экспериментов величина Я0, определяемая как средняя по показателям четырех датчиков, составила соответственно 0,75 и 0,68.
Разница в значениях этого коэффициента объясняется тем, что в третьей серии использовали арматурную сетку, частично воспринимающую массу бетонной смеси, уменьшая тем самым давление на боковые стенки.
Анализ показывает, что чем ниже находится точка, в которой определяется давление, и больше влияние стенок, тем меньше значение коэффициента Хо.
При вакуумировании давление на стенку формы резко падает и достигает 0,3 кгс/см2.
В верхней части формы датчики показывают отрицательные давления, т. е. мембрана прогибается в сторону бетонной смеси.
После отключения вакуум-насоса и установления в вакуум-полости атмосферного давления величина давления смеси на стенку формы возрастает очень незначительно, так как после отсоса воды в процессе вакуумирования смесь становится жестче и коэффициент бокового распора уменьшается.
Установлено, что для качественного заполнения формы необходима эффективная вибрация.
Максимальная величина давления на стенки формы создается после ее заполнения бетонной смесью и может быть определена по формуле (2).
Дальнейшие исследования при вибровакуумиравании проводили на фрагменте железобетонного изделия с толщиной слоя бетонной смеси 16 см. На вакуумном борте было закреплено два навесных вибратора ИВ-2 А. Фрагменты изготавливали из бетонной смеси с подвижностью 10 см осадки стандартного конуса. Датчики давления Д-1, Д-2, Д-3 были закреплены заподлицо с -глухой стенкой установки соответственно на расстоянии 216, 145 и 10 см от дна. Формование осуществлялось в следующей последовательности: загрузка бетонной смеси, включение нижнего бортового вибратора (7,5 мин), выключение верхнего- бортового вибратора (2,5 мин), после окончания вибрации на 20 мин включался вакуум-насос. После вакуум-кропания вибрация повторялась при последовательном включении нижнего, а затем верхнего вибраторов, каждого на 2,5 мил. Затем в течение 10 мин производилось повторное вакуумирование, после чего борт формующей установки отрывался.
Как видно из результатов проведенных экспериментов, статическое давление меньше, чем определенное по закону гидростатики (на рис. 3 показано пунктиром) и может быть’ определено по формуле (2).
Значение амплитуды динамического давления ад, при прочих равных условиях, не зависит от высоты слоя бетонной смеси и определяется амплитудой колебаний борта.
Таким образом, за счет динамического давления полное давление бетонной смеси может значительно превосходить гидростатическое.
После окончания формования объемного блока при выключенных вибраторах эффект тонкостропного превращения бетонной смеси прекращается, при этом резко уменьшается значение коэффициента статического давления % и статическое давление бетонной смеси (см. рис. 3, в).
Проведены эксперименты по определению величины давления на наружные борта машины для непрерывного формования объемных элементов типа «колпак», осуществляемого за счет перемещения сердечника из крайне верхнего «в крайне нижнее положение. Уплотнение смеси, производится при помощи контурной виброрейки, расположенной в верхней части.
Максимальное давление, развиваемое на стенки установки, достигает 1,55 кгс/см2, что значительно превышает гидростатическое давление бетонной смеси. Давление во времени меняется скачкообразно и не закономерно.
Это свидетельствует о том, что определяющее влияние на величину давления имеет деформация смеси, так как при перемещении сердечника его поверхность и поверхность наружных бортов не абсолютно параллельны, а при малой толщине стенки объемного элемента даже незначительная не параллельность, перекосы и неровности вызывают большие местные давления.
Давление на борта установки кассетного типа, установленной на заводе, определяли в процессе заполнения полости стенки блока бетонной смесью и ее виброуплотнения (с момента начала укладки и до окончания процесса формования). На рис. 3 показано изменение давления бетонной смеси на различных стадиях формовочного процесса. Максимальное давление на борт создается к моменту окончания формования, когда вибраторы еще работают (см. рис. 3,6) Максимальное полное давление в каждой точке борта может быть определено по формуле так как амплитуда динамического давления -мала. В зоне эффективной вибрации--значительных скачков © величине давления нет, гак как смесь находится в разжиженном состоянии и при ее деформации не возникают значительные усилия. Однако в этой зоне появляются большие динамические давления, амплитуды которых могут достигнуть 0,3 кгс/см2.

Таким образом, давление на стенки установки для непрерывного формования объемных элементов, в основном, определяется не высотой слоя, а механическими параметрами самой установки.
Были также проведены исследования давления на борта фрагмента установки, в которую бетонная смесь подается методом нагнетания. Размеры фрагмента соответствуют действительным размерам формовочной установки.
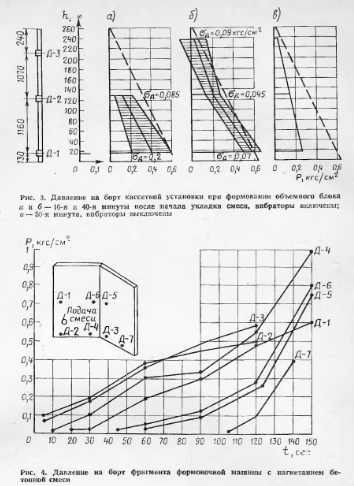
На рис. 4 приведена схема расстановки датчиков при первом и втором формовании. Здесь же приведены графики зависимости давления от времени. За отметку времени «0» принят момент начала подачи бетонной смеси.
Анализ полученных результатов свидетельствует о том, что на всех уровнях давление в процессе заполнения формы смесью растет, достигая максимального значения к концу формования. Давление бетонной смеси на борта достигает до 1 кгс/см2, т. е. 10 тс/м2, что требует применения жестких и массивных форм. Снижение давления приводит к тому, что форма не полностью заполняется бетонной смесью. Давления по площади стенки формы не одинаковы и колеблются в достаточно широких пределах.
Проведенные исследования позволили установить некоторые закономерности давления бетонной смеси, которые следует учитывать при выборе конструктивных схем формовочных машин, их расчете и назначении режимов формования.