
Оптимизация составов вакуумированного керамзитобетояа для цельноформованных объемных элементов
Способ вакуумирования получил широкое применение при формовании изделий из тяжелых бетонных смесей. Производство объемных элементов из тяжелых вакуумированных бетонов освоено на Кременчугском ДОК экспериментального объемно-блочного домостроения. На комбинате предполагается реорганизовать изготовление объемных элементов, комплектующих изделий из легких бетонов.
В связи с этим в НИИСК Госстроя СССР исследовали составы мелкозернистых вакуумированных керамзитобетонов для цельноформоватных объемных элементов на -образцах-кубах с длиной ребра 7,07 «см. Образцы формовали способом вибро-вакуумирования в специальной -вакуумной форме. Вакуумированиа бетонной смеси производилось снизу при разряжении, равном 0,7 атм. Твердение керамзитобетона осуществлялось «в лабораторной пропарочной камере с автоматическим регулированием температуры по режиму 2+6+2 ч, изотермический прогрев происходил при температуре 80°С. Образцы испытывали через 28 сут после тепловой обработки.
Для приготовления керамзито-бетонной смеси применяли портландцемент марки 500 (ГОСТ 310—60), керамзит Керченского завода фракции 5—40 мм и объемной насыпной массой 650 кг/м3. В качестве мелкого заполнителя использовали дробленый керамзитовый песок фракции —5 мм. Песок рассеивался на -отдельные фракции, из которых составлялись необходимые зерновые составы (среднее значение объемной насыпной массы песка 960 кг/м3).
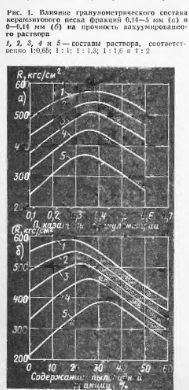
Подвижность используемой для формования образцов бетонной смеси различных составов регулировалась путем изменения се водосодержания и выдерживалась постоянной, в пределах 16 19 см осадки стандартного конуса. Принятое значение осадки конуса оптимально при формовании объемных элементов на вакуумных установках типа МОБ- УВ-1.
Установлено, что прочность легкого бетона на данном пористом заполнителе можно рассматривать как функцию количества и качества содержащегося в нем раствора. Исходя из этого изучали свойства как вакуумированных керамзитобетонов, так и входящих в их состав растворов.
Для проведения опытов было назначено пять составов цемантно-керамзитовых растворов: 1:0,65; 4:1; 1:1,3; 1:1,6 и 1;2. Путем постепенного насыщения раствора керамзитом получали различные составы смесей с объемной концентрацией керамзита (ф) от 0 до 0,6.
Опытным путем определяли оптимальный зерновой состав пористого песка фракции 0—5 мм для вакуумированного керамзитобетона. Зерновые составы керамзитового песка- фракции 0,14—5 мм принимали по кривой, соответствующей уравнению
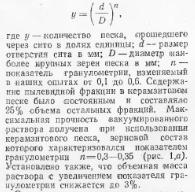
Оптимальному зерновому составу пористого песка для вибрированных легких бетонов кассетного формования соответствует показатель гранулометрии. Сравнивая значения п для вакуумированного и вибрированного легких бетонов, можно отметить, что зерновой состав песка для вакуумированного бетона отличается более высоким содержанием мелких (0,14—1,25 мм) фракций.
Изучали также влияние наиболее активной составляющей керамзитового песка крупностью до 0,14 мм на свойства вакуумированного раствора. Для каждого из принятых составов раствора содержание пылевидной фракции в керамзитовом песке изменялось от 0 до 60% по объему.
С повышением до определенного предела содержания пылевидной фракции в керамзитовом песке прочность вакуумированного раствора увеличилась (рис, 1,6). В зависимости от расхода цемента максимальное значение прочности получено при содержании пылевидной фракции в песке от 15 до 35%. Дальнейшее увеличение количества мелких частиц керамзитового песка, сверх экстремального (по прочности) значения, вызвало резкое снижение прочности раствора, особенно для составов с высоким расходом цемента. Увеличение содержания пылевидной фракции в керамзитовом песке повысило также объемную массу вакуумированного раствора. Однако по сравнению с ростом прочности объемная масса раствора увеличивалась не более чем на 10%.
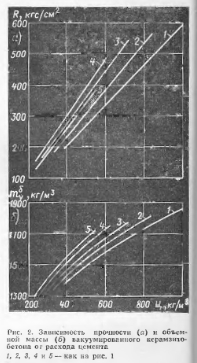
Введение пылевидной фракции песка способствовало также улучшению формовочных свойств керамзитобетонной смеси повышались удобоукладываемость и однородность смеси.
Последующие опыты проводили с использованием керамзитобетонных смесей, приготовленных на пористом песке оптимальной гранулометрии. Сохраняя по сторонним (в пределах одной серии составив) соотношение -между цементом и песком, при одинаковой степени вакуумуплотнения достигалась практически равновеликая прочность раствора в каждом из составов вакуумированного бетона данной серии. На основании этого можно считать, что повышение прочности керамзитобетона с увеличением расхода цемента (рис. 2,а) обусловлено увеличением количества раствора. Уменьшение же количества раствора при соответствующем повышении объемной концентрации керамзита (рис. 3,а) вызвало снижение прочности керамзитобетона. Большей прочностью обладал вакуумированный керамзит обет он, -содержавший раствор более высокого качества.
Изменение объемной массы керамзит о- бетона (рис. 2,6 и 3,6) в значительной мере обусловлено изменением содержания в нем крупного заполнителя. Повышение объемной концентрации керамзита способствовало уменьшению объемной массы бетона. При данном значении объемной концентрации керамзита большей объемной массой характеризовался керамзитобетон с более высоким расходом цемента.
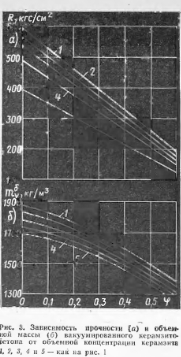
Сравнивая полученные экспериментальные данные с техническими показателями вибровакуумного способа формования объемных элементов из тяжелых бетонов, необходимо отметить, что при практически одинаковом расходе цемента для марок бетона 200—300 достигался значительное (на 600—1000 г)снижение объемной массы позволяет в условиях действующих предприятий и с использованием существующего технологического уменьшить массу объемных элемент:в в 1,3—1,7 раза.
Выводы
Оптимальному зерновому составу - керамзитового песка фракции 0,14—г. ю соответствует показатель гранудомет. В зависимости от расход цемента в керамзитовый песок целесообразно вводить от 15 до 35% объема гелевидной фракции, содержание которого должно быть тем больше, чем ниже расход цемента.
Зерновой состав керамзитового песка для вакуумированного керамзитобетона отличается более высоким по сравнению с керамзитобетонов содержанием мелких (до 1,25 мм) фракций.
Оптимальное -соотношение между мелким и крупным пористыми заполнителями в мелкозернистом вакуумированном керамзитобетоне характеризуется значением г =0,5—0,6.
Применение оптимального зернового состава пористых заполнителей пои расходе цемента 300—400 кг/м3 позволяет получить вакуумированный керамзитобетон марок 200—300 при объемной массе 1400—1500 кг/м3.