
Кассетно-конвейерные линии на предприятиях крупнопанельного домостроения
В настоящее время развитие кассетной технологии происходит в направлении создания кассетно-конвейерных линий. Сохраняя основные достоинства кассет, они, кроме того, обладают более высокой производительностью и низкой трудоемкостью, что обусловлено национальной специализацией технологических операций по постам, более высоким уровнем механизации работ, равномерным потреблением бетона и арматуры, сокращением загрузки мостовых кранов. Расчеты, выполненные ЦНИИЭП жилища, показывают, что себестоимость изготовления панелей внутренних стен н перекрытий на кассетноконвейерных линиях может быть снижена на 1,5—1,7 р., а приведенные затраты сокращены на 1,3—1,5 р. на 1 м3 бетона по сравнению с кассетным изготовлением этих изделий [1]. Кроме того, за счет механизации трудоемких операций и специализация постов значительно улучшаются условия труда бетонщиков.
За последнее десятилетие на ряде заводов нашей страны и за рубежом разработаны и опробованы в производственных условиях кассетно-конвейерные линии различных типов, отличающиеся конструкцией основных узлов, компоновочной схемой и способом формования изделий (рис. 1).
Кассетно-конвейерные линии для производства панелей перекрытий и внутренних стен, действующие на домостроительных предприятиях Алма- Аты и Софии (НРБ) [2], используют традиционный для кассетной технологии способ укладки и уплотнения бетонной смеси. Эти линии компактны, хорошо вписываются в пролет длиной -18 м. Организация производства по конвейерной схеме позволила специализировать технологические посты и упорядочить транспортные потоки в цехе. Опыт промышленной эксплуатации линии в НРБ показал значительное увеличение ее производительности по срав пению с производством в кассетах.
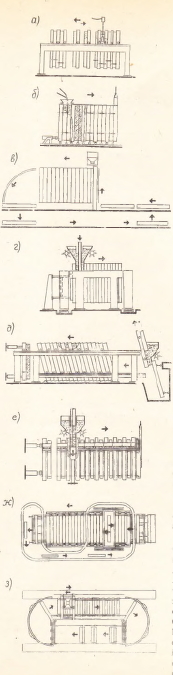
Одним из существенных недостатков кассетного формования является яс пользование пластичных бетонных сме сей, что затрудняет получение бетона марки М 250 и выше. Изделия в этом случае имеют большой разброс прочности при значительных расходах цемента. Поэтому в последние годы были разработаны кассетно-конвейерные линии с использованием метода подвижных щитов, в том числе линия ПЩ-26 на ДСК-2 Главленинградстроя (проект ЦНИИЭП жилища), линия ЛНФ на Тушинским заводе Главмосстроя (проект НИИАТ), кассетно-конвейгрная на Харьковском ДСК (проект КБ ДСК).
ЦНИИЭП жилища провел комплекс .научных исследований технологии формования изделий в производственных условиях на базе линии ПЩ-26 (см. рис. 1), на которой в течение последних лет изготовлено свыше 30 тыс. панелей внутренних стен для угловых секций домов 1ЛГ-602В [3]. Удалось изучить принципиальные оссЛенностп л установить оптимальные параметры работы оборудования, выбрать наиболее рацио тельные режимы формования.
Наиболее ответственными узлами оборудования являются щиты и замковые устройства, обеспечивающие заданные размеры изделий. Как показала практика, в процессе формования возникают значительные усилия, вызывающие частую поломку замков. Величину усилий в замках определяли методом тензомет- рмрования с помощью датчиков сопротивления и регистрировали на ленте осциллографа. Было установлено, что усилия зависят от комплекса технологических факторов: давления бетонной оме- си, вибрации, опускания шита при формовании, перемещения пакета и заполнения последующих отсеков. Суммарные усилия в замках значительно превышают нагрузку от гидростатического давления бетонной смеси и состав мют для верхних 100—170 кН, для нижних — 300—500 кН. Усилия в замках одного уровня отличались неравномерностью, величина их достигала 40% среднего значения нагрузки.
Давление бетонной смеси на щиты при формовании определяли при замерах упругой деформации в двух уровнях, совпадающих с уровнем расположения замков. Результаты показали, что давление по величине близко к гидростатическому.
Качество бетона изделий на уста новках с подвижными щитами в большой степени определяют конструктивные характеристики формующих бункеров и режимы укладки и уплотнения бетонной смеси. Для определения .указанных параметров были проведены экспериментальные исследования на натурных моделях н на установке ПЩ-26. Были найдены оптимальные соотношения конструктивных элементов вибробункера и установлено, что амплитуда колебаний его днища должна составлять 0,5 -0,6 мм при частоте 3000 кол/ /мин; для получения поверхности без крупных пор амплитуда колебаний калибрующей пластины должна быть не менее 0,2- 0,3 мм. Скорость формования была рассчитана из условий обеспечения равномерного распределения и уплотнения бетонной смеси в формовочной полости:
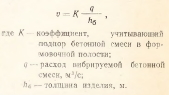
Определялись режимы термообработки и составы бетонной смеои. Исследования по подбору состава и длительная производственная проверка на линии ПЩ-26 показали, что при формовании целесообразно использовать умеренно жесткие смеси (с Ж=30— 50 с). Применение более жестких бетонных смесей, возможно, приводит к ухудшению качества поверхности панелей.
Режимы термообработки определяли па контрольны1 кубах и проверяли в производственных условиях. Общая длительность термообработки составляла 7 ч при режиме 2+2+3 (подъем тсмпературы+и ютершшеская выдерж- ка+выдержка без подачи пара). Консистенция гмссп доставляла от 30 до 60 с, состав смеси цемент марки 400 Пнкалечокого завода - 100 360 кг со ответственно для бетона марки М200 и МЗОО. щебень гранитный1—856 кг, ш счаио-гравиняая смесь 1080 кг. Прочность бетона изделий при распалубке составляла 70%.
Результаты исследований и опыт эксплуатации линии ПЩ-26 лепи в основу разработки головного обращали промышленные установки щитами для производства панелей внутренних степ па ДСК 7. В настоящее время изготавливают оборудование формовочной линии.
При проектировании и эксплуатации кассетно-конвейерных наибольшие трудности вызывают необходимость перемещения пакета щитов с изделиями, восприятие значительных (в несколько десятков тонн) распорных усилий от давления бетонной смеси и цикличное отсоединение и присоединение щитов.
Транспортные схемы таких линий включают гидродомкраты-толкатели, рольганги, поворотные круги, передаточные тележки, подъемники, распалубочные устройства и другие механизмы. Обеспечение их хорошего взаимодействия и необходимой надежности — сложная инженерная задача. Поэтому конструкция кассетно-конвейерной линии должна отличаться простотой транспортной схемы и минимальной протяженностью коммуникаций.
Для восприятия распорных давлений бетонной смеси, как правило, применяют замки, расположенные по торцам щитов. Такое расположение позволяет сравнительно просто механизировать раскрытие и закрытие замков при отсоединении или соединении ¦ щита к пакету. Вместе с тем такое размещение замков требует увеличения жесткости торцов щитов, а следовательно, их толщины и массы. Из-за наличия люфтов в замковых устройствах фактическая толщина изделий возрастает против номинальной. Поэтому при проектировании кассетно-конвейерных линий более рациональными считаются беззамковые системы с жесткими неразъемными связями.
В ЦНИИЭП жилища разработан проект роторной кассетно-конвейерной линии (рис. 2), которая представляет собой систему щитов, выполненных в виде секторов и жестко соединенных друг с другом таким образом, что между ними образуется клиновидная полость, куда устанавливают форму. Щиты-секторы смонтированы на кольцевой платформе, собранной из отдельных секций, каждая из которых имеет по три колеса. При вращении платформы колеса перемещаются по двум кольцевым рельсам. Поворот ротора на заданный угол обеспечивается гидроцилиндром.
В полости между щитами на посту бетонирования вводят форму, на которой с обеих сторон смонтированы бортовая оснастка и проемообразователи, установлена арматура и закладные де тали. Форма, как и полость, выполнена в виде клина, уклон каждой которого равен 150— 200 мм (угол в вершине клина составляет примерно 2°). Это позволяет осуществлять ввод формы в полость (сборку) и ее извлечение (распалубку) без раздвижки щитов.
Для прогрева отформованных изделий в щитах и форме предусмотрены паровые полости, подача пара и отвод конденсата осуществляется через два кольцевых коллектора, расположенных е внешней стороны платформы. Предусмотрена- двухстадийная тепловая обработка изделий. Первая стадия осуществляется в роторе двухсторонний контактный прогрев при температуре 90—95°Г. в течение 4,5 ч, вторая — в туннельной камере при температуре 75— 80°С в течение 6 ч.
Рядом с ротором расположен участок распалубки и подготовки форм, где изделия распалубливают мостовым краном, выполняют чистку и смазку форм, их оснащение арматурой и закладными деталями, форму по постам перемещают с помощью рольганга и передаточной тележки, а затем подают на формовочный пост ротора.
Формование изделий на роторной кассетно конвейерной линии выполняют либо по способу подвижных щитов, либо по виброударному.
Метод подвижных щитов, обладая существенными преимуществами, вместе с тем требует соблюдения более жесткой технологической дисциплины и более сложного формовочного оборудования, поэтому его рациональнее использовать п,ри большой производительности формовочной линии и достаточно высокой культуре производства.
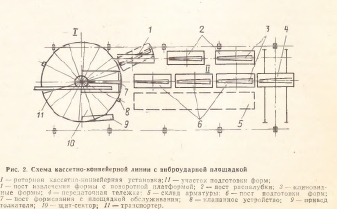
Лаборатория заводской Технологии домостроения ЦНИИЭП жилища разработала виброударный способ формования изделий в вертикальном положении, при котором используют воздействие вертикально направленных ударов и вибрацию. Вибрация -служит для минимально необходимого в данных условиях разжижения бетонной смеси (амплитуда колебаний на уровне критической), а низкочастотные удары большой амплитуды обеспечивают уплотнение смеси за счет создания значительных инерционных ускорений. Благодаря большой жесткости формы в вертикальном направлении ударные- и вибрационные колебания распространяются равномерно, без существенных потерь, что обеспечивает одинаковое уплотнение смеси. Малая амплитуда вибрации (0,08—0.1 мм) и низкая частота ударов (150—220 в 1 мин) позволяет применять генераторы виброударных воздействий сравнительно небольшой мощности.
Виброударный способ отличается относительной простотой, универсальностью и позволяет использовать бетонные смеси жесткостью 30—50 с. -нормального фракционного состава. Разброс прочности по высоте изделий составляет 6—9%, качество поверхностей изделий соответствует качеству -панелей кассетного формования. Установочная мощность виброударного привода составляет 1,0—1,3 кВт на 1 т колеблющейся массы. Уровень шума не превышает нормативных пределов. Критерий шумности равен 76—80 единиц (с преобладающим низкочастотным спектром). Виброударный способ обеопечивает эффективное формование изделий толщиной от 50 до 180 мм. Время вибропроработки смеси составляет 3— 4 мин.
Выводы
Кассетно-конвейерные линии являются перспективным направлением развития кассетной технологии. При их разработке необходимо учитывать требование простоты транспортной схемы и (минимальной протяженности коммуникаций, по которым перемещаются щиты и изделия.
При разработке компоновочных и конструктивных решений кассетно-конвейерных линий следует отдать предпочтение беззамковой системе образования пакета щитов, использованию эффективных технологических способов укладки и уплотнения бетонных смесей, например виброударного, подвижных щитов и других, обеспечивающих сокращение тепловой обработки и высокое качество изделий.
Роторная кассетно-конвейерная линия имеет ряд конструктивных и технологических достоинств, в том числе компактность, малую металлоемкость, относительно небольшое число обслуживающих механизмов, что обусловливает перспективность ее применения ,на заводах КПД.