
Перспективы развития методов форсированного прогрева изделий заводского домостроения
Предварительный разогрев бетонной смеси и форсированный подъем температуры в формах позволяют сократить длительность выдерживания изделий за счет уменьшения или ликвидации периода разогрева. Таким путем можно уменьшить время тепловой обработки примерно на 7з по сравнению с традиционной, т. е. с 11—12 до 7—8 ч (до получения 70% проектной прочности).
Особенностью заводского домостроения является применение бетонов марок М 150—300, расход цемента для которых не превышает 350—400 кг/м3. Технология ориентирована преимущественно на применение литых, подвижных или умеренно-жестких смесей, форсированная обработка которых существенно различается при использовании холодных и, особенно, горячих составов.
При прочих равных условиях продолжительность тепловой обработки зависит главным образом от Ц/В состава, а при высоких значениях этой величины предварительный разогрев как способ ускоренного прогрева неприменим.
Из графика, полученного на основе обработки данных (рис. 1), видно, что длительность прогрева в течение 8— 12 ч для достижения 70% проектной прочности достаточна лишь для бетонов, проектная прочность которых выше 30 МПа. Для составов, применяемых в заводском домостроении, продолжительность прогрева возрастает до 12—16 ч и более. Если на заводах в ряде случаев прогрев бетона с проектной прочностью 20 МПа длится меньшее время, это означает, что расход цемента превышает нормативные значения по СН 386-74 (повышается значение Ц/В). Между тем в условиях заводского домостроения можно практиковать короткие режимы прогрева и без перерасхода цемента, но за счет уменьшения распалубочной прочности и внедрения предварительного разогрева смеси. Так, из графика на рис. 1,а видно, что для изделий заводского домостроения распалубка при 50%-ной проектной прочности возможна после 6— 8 ч прогрева, а при 30%-ной прочности — через 3—5 ч. Оценка прочности бетона производится спустя 4 ч после распалубки, а ее величина находится в пределах 6—9 МПа, при которых возможен съем изделий за петли.
Из данных ЦНИИЭП жилища о режимах прогрева изделий из горячих смесей (рис. 1,6) видно, что для составов, применяемых в заводском домостроении, 70% проектной прочности могут быть достигнуты при разогреве оме- си до 80°С через 7—7,5 ч прогрева, а 30% всего через 2 ч.
Характерной особенностью использования горячих смесей является незначительная разница во времени твердения составов с разными Ц/В. Повышение Ц/В отношения состава может привести для обычных смесей к сокращению длительности прогрева на 6 ч, в то время как при использовании разогретых до 80°С смесей эта разница не превысит 0,5—1 ч (рис. 2). Это свидетельствует о нецелесообразности повышения жесткости горячих смесей в целях форсирования твердения бетона, а также о возможности сохранения режимов прогрева постоянными при изменениях состава смеси и номенклатуры изделий, часто наблюдаемых на производстве.
Загустевание горячей смеси, вызванное разогревом, компенсируют добавкой воды, объем которой невелик. Однако положение резко меняется, когда Ц/В выходит за пределы постоянной водопотребиости состава: загустевание растет непропорционально росту температуры, что вызывает необходимость (Введения дополнительно большого количества воды, а в целях обеспечения заданной прочности — и цемента.
Критическое значение Ц/В зависит от нормальной густоты цемента и температуры:
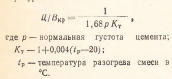
При средней нормальной густоте цемента 0,27 и температурах разогрева в диапазоне 40—80°С докритичаские значения Ц/В находятся в области, характерной для составов заводского домостроения (рис. 1,6). Верхняя граница области расположена в зоне, за пределами которой находятся бетоны с проектной прочностью более 30 МПа.
Отсюда следует, что можно рекомендовать приемы сокращения твердения бетона в формах, базирующиеся и на снижении распалубочной прочности и горячем формовании. Эти приемы могут применяться порознь и вместе. Ввиду того что при снижении распалубочной прочности основной проблемой становится трещино-образование в бетоне, этому (вопросу надлежит уделять особое внимание. Опыт применения предварительного разогрева свидетельствует о сокращении количества трещин, поэтому применение горячих смесей становится условием ранней распалубки изделий. Последующий рост прочности бетона в цехе зависит от величины распалубочной прочности и составляет 12—15% в первые сутки выдерживания.
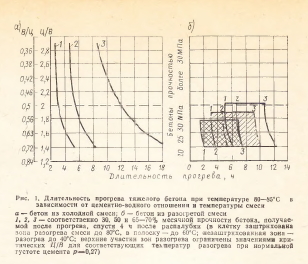
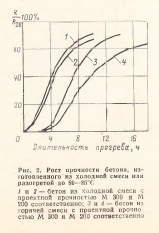
Вопрос о создании камер второй стадии прогрева решается в зависимости от результатов технико-экономического анализа производства, с учетом того, что в цехе длительность набора от 30 до 50% прочности составляет 1,5 сут, а от 50 до 70% —2—3 сут.
Сроки схватывания (начало и конец) обычно находятся в пределах 1,5—4 ч при нормальной температуре, а по мере ее подъема резко сокращаются. Однако, несмотря на последнее обстоятельство, рост прочности (В первые 2—3 ч прогрева бетона происходит крайне медленно (см. рис. 2). Ускорить этот процесс можно введением добавок — ускорителей твердения, в результате чего могут резко уменьшиться сроки схватывания и повыситься ранняя прочность. Проследим изменение прочностных показателей бетона из смесей подвижностью 1—2 см осадки стандартного конуса, с Я/Д=0,75, прогретой в замкнутых формах в камере при 90— 98°С в течение 0,5—2 ч.
Предварительная выдержка смеси составила 1 ч; испытание производили спустя 2—3 ч после прогрева (табл. 1).
Влияние предварительной выдержки смеси (перед формованием и тепловой обработкой) на рост прочности в начальный период прогрева можно увидеть из данных, полученных ЦНИИЭП жилища. Разогрев уложенного бетона в замкнутых формах до 80—95°С производили в течение 14 мнн переменным электротоком; последующий прогрев осуществляли в камере при температуре 80°С.
Таким образом, (введение добавок и предварительная выдержка обеспечивают ускоренный набор прочности, особенно в течение первых 2 ч твердения бетона, которое происходило при 80°С. В последующий период твердения разница в интенсивности роста прочности сглаживается и в возрасте 1 мес отличия в прочности фактически отсутствуют. При выборе добавок для ускорения твердения, определении их количества нужно исходить из необходимости сохранения подвижности смеси при (Выполнении транспортных и формовочных операций.
Для борьбы с увеличением пористости цементного камня при прогреве, а также для повышения степени гидратации предлагается применять замкнутые формы, в которых достигается прочность, равная контрольной и превышающая ее. Среди применяемых в заводском домостроении типов форм замкнутость в наибольшей степени обеспечивается в кассетных установках, где открытая поверхность бетона не превышает 2—3% поверхности изделия. Полностью замкнутые формы применяют в установках с подвижными щитами.
В процессе форсированного прогрева в бетоне неизбежно возникновение внутреннего давления, воспринимаемого элементами формы. При формовании изделий в горизонтальном положении такое давление может быть создано до начала разогрева бетона за счет внешней нагрузки. Но создание больших давлений весьма затруднительно, поэтому способы, базирующиеся на такой обработке бетона, не получили распространения.

Технически вполне доступно создание давлений, не выходящих за пределы 0,1—0,2 МПа. Тем более, что, по данным ЦНИИЭП жилища и ИСиАГосстроя БССР, повышение давления до 1 МПа существенно не сказывается на ускорении роста начальной и повышении конечной прочности.
По данным [3] из смесей, разогретых до 60 и 90°С, после прогрева бетона в течение 1,5 ч при 100°С под давлением 100Х102 Па была получена прочность 9 и 16,9 МПа. Испытания производили через 4 ч после прогрева, расход цемента Воскресенского завода Б ГЦ-500 составлял не менее 470 кг/м3 бетона (контрольная прочность в возрасте 1 мес—33,6 МПа). Приведение полученных данных к марке бетона 200 показывает, что а этом случае прочность после прогрева будет оцениваться «10 МПа. С учетом выдержки перед испытанием этот результат можно уменьшить на 20—30% и предположить, что прочность бетона составит 7— 8 МПа через 2 ч после начала прогрева в камере.
В ЦНИИЭП жилища были выполнены опыты на подвижных смесях с расходом Старооскольокого портландцемента марки 400—300 кг/м3. Уложенную в форму смесь в течение 15 мин разогревали до 80—90°С электротоком, после чего образцы на 2 ч помещали в камеру с температурой 80°С. Разогрев я твердение бетона производили под пригрузом. В процессе разогрева из смеси через специальные щели удалялась часть воды загворения (примерно 15% первоначального объема).
Эти эксперименты также позволили установить возможность получения прочности, равной 7—8 МПа, за 2 ч прогрева, но при применении пригруза, извлечении части воды затворения и предварительной выдержке смеси.
Прочность, полученная в течение 2 ч, соответствовала 30% месячной, что примерно в 2 раза выше результатов, полученных на горячих смесях без пригруза (ом. рис. 2), сразу после прогрева (т. е. без последующей выдержки).
В этой связи о прогреве под давлением можно говорить как о перспективном способе, который позволит обеспечить результат, превышающий возможности обычного горячего формования, особенно при распалубке изделий в раннем возрасте.