
Высокотемпературный прогрев изделий из легкого бетона в среде с пониженной влажностью
В качестве ограждающих конструкций жилых и промышленных зданий широко применяются однослойные керамзитобетонные панели. Особенность легкого бетона медленно отдавать влагу заставляет изыскивать методы их изготовления, обеспечивающие требуемую влажность. Низкая влажность панелей улучшает теплофизические характеристики стен и требует меньше энергетических затрат на поддержание в помещениях необходимых температурных режимов. Для решения этой задачи целесообразно заменить пропаривание изделий высокотемпературным прогревам в среде с пониженной влажностью. Однако эта технология недостаточно изучена, что тормозит ее внедрение в производство.
Выполненные НИИЖБ обширные исследования позволили определить основные параметры тепловой обработки керамзитобетонных изделий при температурах среды более 100°С, с учетом прочностных и структурных характеристик бетона. На основе этого разработана технологическая линия по изготовлению керамзитобетонных панелей с высокотемпературным прогревом, которая работает на Прокопьевском заводе в Кузбассе.
Опыты проводи на образцах-моделях из керамзитобетона марки М100.
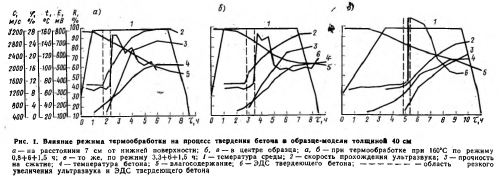
Жесткость бетонной смеси по техническому вискозиметру составляла 20— 25 с. Толщину образцов в соответствии с толщиной панелей приняли 40, 30, 20 и 15 см. Формы для их изготовления обеспечивали создание одномерного теплового потока, идентичного возникающему в центре изделия в производственных условиях.
Основные факторы, определяющие режим термообработки, следующие: температура изотермического выдерживания 120—160°С, продолжительность изотермического выдерживания 2—6 ч, скорость подъема температуры греющей, среды 40—160°С/ч. Все образцы остывали в камерах в течение 1,5 ч.
При твердении бетона важное значение имеют процессы гидратации и набора прочности. Степень гидратации цемента существенно зависит от режима термообработки и толщины изделий и колеблется в пределах от 40 до 71%. При этом чем они толще, тем большая неравномерность степени гидратации по сечению (3—4%). Закономерность ее изменения не одинакова при различных режимах термообработки. При температурах изотермического выдерживания (120—130°С) решающим в кинетике степени гидратации цемента в бетоне является изменение температурного поля. С увеличением температуры до 140—160°С превалирующим становится фактор распределения влажности по сечению изделий. Структурные особенности материала при вьюокотемпературном прогреве изучали ультразвуковым и импульсным методами, а также по изменению ЭДС бетона. Прочность бетона контролировали по испытаниям образцов-кубов на сжатие через каждые 2 ч термообработки.
Анализируя кривые электродвижущей силы (ЭДС) и скорости распространения ультразвуковых импульсов в бетоне образцов-моделей (рис. 1), можно заметить, что характер кривых, полученных для различных сечений образцов и при различных режимах термообработки, одинаков. Изменение электродвижущей силы бетона вполне согласуется с предположением о ступенчатом характере процесса гидратации. Сразу же после затворения цемента водой начинается интенсивное химическое взаимсдействие этих компонентов с образованием на поверхности зерен цемента гидратных накоплений, формирующихся постепенно в оболочки. Вода; диффундирующая через эти оболочки и соединяющаяся с минералами цемента, образует продукты гидратации. Таким образом,происходит процесс накопления новообразований под ранее образовавшейся гидратной оболочкой. Этот период на кривой ЭДС характеризуется участком, не отражающим резких изменений концентрации электролита. Скорость распространения ультразвука, достигнув некоторой постоянной величины (1000—1400 м/с), стабилизируется, что соответствует образованию первоначального кристаллического каркаса и появлению в бетоне некоторой начальной прочности.
На определенной стадии уплотняющиеся гидратные продукты механически разрушают гидратные оболочки. Непрореагирававшие части цементных зерен обнажаются и начинается их интенсивное взаимодействие с водой с выделением Са(ОН)2 и его диссоциацией на Са1+ и 2 ОН- (на кривой ЭДС резкое увеличение концентрации электролита). Характерно, что расположение этой области во времени неодинаково не только для образцов различных размеров, но и для отдельных сечений одного и того же образца и зависит от режима термообработки. Следующая горизонтальная площадка на графике соответствует периоду интенсивного протекания химического взаимодействия в системе «цемент—вода» с выделением извести и ее кристаллизацией из пересыщенного раствора. Затем рост скорости прохождения ультразвука снижается, а в некоторых случаях практически прекращается. Этот период соответствует резкому снижению концентрации электролита, что указывает на ослабление процессов химического взаимодействия.
Проведенные эксперименты свидетельствуют о том, что нераарушающие методы контроля твердения бетона в процессе термообработки позволяют установить достаточно четкие временные параметры наступления отдельных периодов в процессе структурообразования, их начало, интенсивность протекания и практическое завершение.
Степень развития процесса структурообразошания в различных зонах бетона конструкции и рост прочности определяются кинетикой распределения температуры и влажности по сечению изделия. Исследования температурных полей в зависимости от изменяющихся параметров теплового воздействия показали, что их кинетика при прочих равных условиях зависит от толщины обрабатываемого изделия и что оптимальный режим можно выбирать только для изделий конкретных размеров.
При температуре изотермического выдерживания 120СС продолжительность термообработки для изделий толщиной 30—40 см лимитируется только получением необходимой остаточной влажности бетона. Для изделий толщиной менее 20 си продолжительность изотермического выдерживания не должна превышать 4 ч. После этого термообработку надо прекратить или снизить температуру среды до 100—105°С. При 160°С для изделий толщиной 40 см оптимальная продолжительность изотермического выдерживания составляет 3 ч, а толщиной 30 см — 2,5 ч. После этого времени термообработку необходимо прекратить или проводить при температуре 100— 105вС.
Важным фактором при выборе продолжительности термообработки является скорость подъема температуры греющей среды, причем чем выше температура изотермического выдерживания и меньше толщина обрабатываемых изделий, тем существеннее влияние скорости paзогрева. В образцах толщиной 30—40 ом при термообработке по режиму со скоростью разогрева ореды 160°С/ч и температурой 160°С (по сравиению с режимом термообработки при 40°С/ч) не наблюдается перелрева поверхностных слоев, а в изделиях толщиной 20 ом и менее перегрев поверхностных слоев менее интенсивен. Это объясняется соотношением плотности теплового потока и способностью изделия аккумулировать тепло.
При малых скоростях разогрева среды л высоких температурах изотермического выдерживания за время с начала термообработки до изотермического выдерживания (3—3,5 ч) поверхностные слои бетона успевают достаточно прогреться и потерять часть воды затворения. Иначе говоря, потенциальные возможности бетона сопротивляться перегреву уже израсходоваяы или недостаточны для того, чтобы в период изотермического выдерживания можно было избежать пересушивания поверхностного слоя изделия.
При высоких скоростях разогрева среды к началу изотермичеокого выдерживания температура поверхностных слоев мало отличается от центральных. Равновесие между испаряющейся влагой и поступающей к поверхности из внутренних слоев сохраняется до тех пор, пока изделие не прогрето до максимальных температур (105—106°С) и количество воды, поступающее из внутренних слоев бетона, компенсирует количество испаряющейся воды с поверхности изделия.
Исследование влажностного состояния бетона в процессе термообработки, проведенное в Калининском политехническом институте, показало, что при назначении режимов термообработки большое внимание следует уделять не только параметрам греющей среды, но и продолжительноести теплового воздействия. Неправильный выбор продолжительности термообработки приводит или к недостаточному прогреву изделия и к недобору бетоном прочности, или к перегреву >и пересушиванию бетона и необратимым структурным нарушениям. Lc.m при пропаривании при атмосферном давлении температура бетона не поднимается выше 100—105°С, то при высокотемпературном прогреве в среде с пониженной влажностью она может подняться выше, что приводит к перегреву и пересушиванию материала. При достижении на поверхности бетона температуры 100°С начинается интенсивное испарение влаги. Если внешний массообмен не лимитируется внутренним массопереносом, то поверхность испарения совпадает с поверхностью бетона. В противном случае в поверхностных слоях происходят углубление зоны испарения и обезвоживание бетона. От фронта испарения влага в виде молярного фильтрационного потока пара движется к горячей поверхности. Температура бетона в зоне испарения колебалась в широких пределах (к 6 ч изотермического выдерживания образцов толщиной 15 м при температуре среды 160°С температура бетона в зоне испарения достигала 125—130°С). Это влечет за собой появление в легком бетоне структурных нарушений, значительно снижающих его прочность.
Правильно выбранный режим высокотемпературного прогрева с точки зрения влажностного состояния изделия является более рациональным по сравнению С паройрогревом, так как позволяет за более короткий срок термообработки подучать изделия с меньшей остаточной влажностью. Величина остаточной влажности при прочих равных условиях определяется толщиной обрабатываемого изделия и может колебаться для изделий различной толщины при одинаковых режимах от 3—4 до 12—44%, в то время как после пропаривания по режиму 3+6+3 ч при температуре 85—90°С остаточная влажность бетона составляет 17—19%.
Исследования макроструктуры бетона, прошедшего высокотемпературный прогрев по оптимальному режиму в среде с пониженной влажностью, показали что керамзитобетон отличается плотной структурой без видимых нарушений. Для определения рациональных режимов высокотемпературного прогрева в зависимости от изменяющихся параметров греющей среды можно пользоваться графическими зависимостями (рис. 2). Густозаштрихованиая часть обозначает область рекомендуемой продолжительности термообработки, при которой бетон набирает прочность от 70% и выше сразу после прогрева. Оптимальным -следует считать режим термообработки, назначенный по параметрам теплового (воздействия, средней части рекомендуемой зоны. "Слева от нее продолжительность термообработки недостаточна для набора бетоном прочности 70%- марочной сразу после термообработки, справа от неё — не может быть рекомендована. из-за перегрева поверхностных слоев бетона.
Однако после термообработки по указанным режимам остаточная влажность бетона все же на 2—4 % допускаемой. При (необходимости получения изделий: с более низким значением остаточной-влажности термообработку следует продолжить при температуре среды не выше 100-106°С.
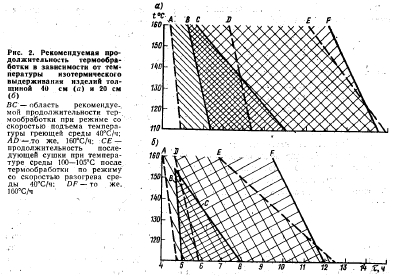
Таким образом, результаты проведенных исследований позволяют утверждать, что высокотемпературный прогрев в среде: с пониженной влажностью керамзитобетонных изделий марок до М 100 позволяет за более короткий срок (по сравнению с, пропариванием) получать изделия с равноценной прочностью и меньшей остаточной влажностью.