
Морозостойкий бетон для морских сооружений
Задача получения бетона, стойкого в суровых климатических условиях и при действии морской воды, особенно актуальна в связи с расширением строительства в арктических районах.
Представляют интерес результаты многолетних исследований, выполненных ЦНИИС, а также длительный (в течение 15 лет) опыт работы Кислогубской приливной электростанции (ПЭС). Здание ПЭС представляет тонкостенную железобетонную конструкцию, изготовленную в сухом доке и на плаву доставленную к месту эксплуатации [1],
Условия работы гидротехнических сооружений в приливной зоне весьма сложны. Вода, согреваемая теплым течением, зимой здесь не замерзает, а арктический воздух охлаждается до —25°С, а в отдельных случаях и до —30...—40°С. Колебания уровня моря в зоне приливов достигают 4 м. Конструкции сооружений в этой зоне два раза в сутки насыщаются морской водой и дважды замораживаются на воздухе. Интенсивность воздействия попеременного насыщения водой и замораживания зависит от расположения
конструкции по отношению к уровню моря. На среднем уровне воды продолжительность насыщения водой и замораживания равна, выше этого уровня сокращается период насыщения, а ниже — период замораживания. Сопоставление числа циклов замораживания и оттаивания на различных уровнях с относительной степенью разрушения бетона в действующих сооружениях (рис. 1) показывает, что более длительное замораживание и достаточное время насыщения водой способствуют быстрому разрушению. По данным метеорологов, число переходов температуры воздуха через СГС составляет свыше 400, однако с учетом микроклимата у сооружении, смягчаемого влиянием зеркала не замерзающей в зимнее время воды, и пониженной (до —2°С) температуры замерзания морской воды фактическое число циклов замораживания и оттаивания около 230.
Многолетними испытаниями бетонов различного состава и железобетонных конструкций, проводившимися ЦНИИС в натурных условиях и на специальном стенде [2]-, ускоряющем их искусственным регулированием продолжительности цикла по данным о температурах в бетоне, установлены переходные коэффициенты, характеризующие интенсивность воздействия цикла при различных температурах [3]. Сопоставление состояния образцов после различного числа циклов замораживания и оттаивания в естественных условиях и при замораживании при разных температурах в бассейнах стенда дополнило переходные коэффициенты постоянной поправкой.
В результате появилась возможность определить требуемую марку бетона по морозостойкости для конструкций ПЭС. В основу был положен принцип неразрушаемости бетона в течение года воздействия, т. е. отсутствие снижения прочности после числа циклов замораживания-оттаивания, равного годовому, с учетом восстановления структуры бетона в летний период. Большая роль перерыва в повышении стойкости бетона при многократном замораживании и оттаивании иллюстрируется данными рис. 2. При установлении числа циклов, которые должен выдержать бетон при испытании на морозостойкость, следует учитывать , что по ГОСТ 10160— 76 допускается снижение прочности до 15%. Чтобы избежать уменьшения прочности, морозостойкость бетона должна быть повышена не менее чем на 30%. Например, для района Кислогубской ПЭС число годовых циклов может быть принято равным 300, а с учетом требования о сохранении прочности — 400. Кроме того, необходимо учитывать данные о коэффициенте однородности бетона по морозостойкости, который, согласно работе [4], характеризуется следующими значениями; при обеспеченности 0,8; 0,95; 0,99 и 0,999 Кодн составляет соответственно 0,6; 0,5; 0,4 и 0,3.
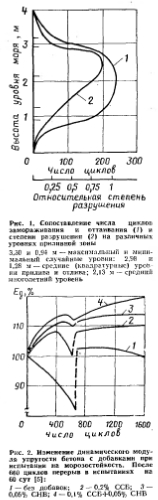
Следовательно, требуемая проектная марка бетона по морозостойкости при обеспеченности 0,95 должна быть не менее Мрз800. Для бетона конструкций Кислогубской ПЭС была принята минимальная марка бетона по морозостойкости Мрз1000. Ее гарантирован ное достижение было основано на выполнении комплекса мероприятий [2], включающего: применение материалов наиболее стойких в данных условиях: проектирование состава бетона оптимальной структуры с введением пластифицирующих и воздухововлекаюш: х добавок; создание нормированных тепловлажностных условий твердения, способствуюших получению стороной цементного камня и снижающих температурные напряжения з бетона; использование технологии изготовления и уплотнения бетонной смеси, позволяющей получать однородную структуру цементного камня и текстуру бетона; примененение дополнительных- мероприятий по тепло- и гидроизоляции для элементов, находящихся в особенно сложных условиях службы.
На морозостойкость бетона наиболее влияет микроструктура цементного камня, которая определяется водокаменным отношением и объемом условно-замкнутых пор, заполненных воздухом. Его можно установить по многочисленным данным о высокой эффективности введения в состав бетона воздухововлекающнх добавок, что было учтено при создании железобетонных конструкций Кнслогубской ПЭС из морозостойкого бетона (рис. 3)
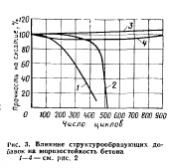
Выбор материалов для морозостойкого бетона производили на основании выполненных ранее работ с учетом выпускаемых промышленностью цементов и местных заполнителей. В связи с требованием одновременно высокой морозостойкости и стойкости в морской воде был принят сульфатостойкий портландцемент Вольских заводов, клинкер которого содержит трехкальциевый алюминат С3А не более 5%, трехкальциевый силикат QS не более 50% ври содержании суммы C3A+C4/VF не более 22%- Он замедляет нарастание прочности в начальный период твердения, однако в длительные сроки нарастания прочности способность к устранению микродефектов, образующихся при многократном замораживании и оттаивании, повышена, что и подтвердили дальнейшие исследования.
В качестве заполнителей использовали гранитный щебень фракций 5—10 и 10—20 мм и местный среднезернистый кварцевый песок. Принятое В<0,4 ври расходе цемента 400—500 кг/м3 позволяло получать удобоукладываемые смеси с расходом воды не более 170 л/м3. Подвижность смесей 2—4 см сказалась оптимальной при укладке в тонкостенные и густоармированные конструкции с применением высокочастотных вибраторов. Получить удобоукладываемые смеси, не отделяющие воду и содержащие вовлеченный воз- Нх. удалось введением в состав бегонией смеси комплексной добавки ССБ+СНВ. В момент окончания перемешивания смеси количество воздуха составляло 4—6%. Для исключения осадка, образующегося при совместном растворении добавок в жесткой воде, в воду затворкния вводили стабилизирующий компонент — альгинат натрия. при его отсутствии добавки вводили раздельно. Дозировку добавок устанавливали на основании экспериментов и уточняли в производственных условиях в зависимости от свойств бетонной смеси и содержания в пей воздуха.
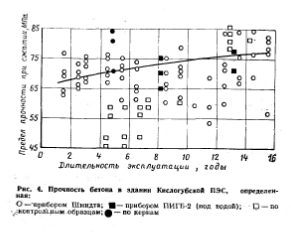
Добавки подбирали на основании испытаний в бассейнах, осуществленных по ускоренной методике [2]. После 300 циклов наиболее эффективной оказалась комплексная добавка ССБ+ +С.НВ. Продолжение экспериментов до 1500 циклов подтвердило правильность выбора.
Одновременно с образцами из бетона с добавкой ССБ+СНВ изготовили фрагмент конструкции — куб с ребром 1 м, с толщиной стенки 15 см. После 1500 циклов замораживания и оттаивания бетой открытых поверхностей фрагмента не изменился, на поверхности сохранились следы опалубки.
Для дальнейшей проверки морозостойкости бетонов принятых составов в лабораторных условиях изготовили образцы из материалов, предназначенных для бетонирования блока ПЭС. Состав бетона на 1 м3 следующий: цемент 480 кг, песок 650 кг, щебень фракции 5—10 мм — 450 кг, фракции 10— 20 мм — 840 кг, вода—180 л. В/Ц= = 0.38; добавки —0,15% ССБ или 0,15% ССБ +0,02% СНВ. Испытания на морозостойкость по стандарту проводили с оттаиванием в морской воде. Все образцы с воздухововлекающими добавками выдержали более 500 циклов.
В период строительства систематически испытывали на прочность и морозостойкость контрольные образны бетона в течение 10 лет в бассейнах, а затем в натурных условиях в приливной зоне на стенде рядом со зданием ПЭС.
Основной производственный состав бетона следующий: сулыфатостойкий
портландцемент марки М500 завода «Большевик» — 480 кг/м3; гранитный шебень — 1210 кг/м3 (5—10 мм —35%: 10—20 мм—65%): песок кварцевый с М.;п = 2.3—630 кг/м3; вода — 180 л; 0,01%ССБ+ (0,02 0,03) % СНВ. Содержание воздуха в бетонной смеси 60- 80 л/м3: В1Ц—0 375; ОК==1. .3 см: Ж =15...30 с. Бетон в сооружении увлажняли в течение 30 сут, а в холодную погоду укрывали брезентом и подогревали паром до 30—40°С.
В процессе эксплуатации ПЭС регулярно контролировали прочность бетона испытанием контрольных образцов и неразрушающнмн методами.
Полученные данные (рис. 4) свидетельствуют о том. что ПРОЧНОСТЬ бетона в сооружении за 15 лет увеличилась по сравнению с проектной маркой М400 почти вдвое, а в некоторых образцах и в конструкции превысила М800. Внешне состояние контрольных образцов, испытывавшихся на морозостойкость за этот период, практически не . изменилось. Бетон вырубленных после пяти лет эксплуатации в зоне прилива кернов значительно превосходил проектные требования.
Подвижность смеси поддерживали 1 —3 см, а вибрирование осуществляли высокочастотными шланговыми вибраторами. При этом контролировали продолжительность вибрирования на каждой позиции для исключения возможности расслоения смеси и водоотделения. Была введена индивидуальная ответственность бетонщиков за качество уплотнения отдельных элементов конструкций. Все незначительные дефекты поверхности тщательно расчищали и заделывали полимербетонным раствором на эпоксидной смоле. В результате блок ПРИ затоплении пе имел течей.
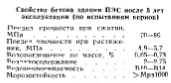
Высокое качество бетона и бетонных работ, соответствие бетона заданным требованиям во всех элементах комплекса технических мероприятий определило надежную работу КОНСТРУКЦИЙ ПЭС в СУРОВЫХ климатических УСЛОВИЯХ. Пенный опыт, строительстве Кислогубской ПЭС следует использовать ПРИ проектировании сооружений, к бетону КОТОРЫХ предъявляются повышенные требования ло МОРОЗОСТОЙКОСТИ. Возможность получения бетона марки свыше МрзЮОО и изготовления из него тонкостенных железобетонных КОНСТРУКЦИЙ подтверждена опытом 15-летией эксплуатации Кислогубской приливной электростанции.