
Быстротвердеющий бетон сухого формования
При традиционной технологии формования сборных бетонных и железобетонных изделий из водозатворенных смесей используют химические добавки [1], а также предварительный разогрев смеси, позволяющие сократить индукционный период формирования структуры цементного геля, ускорить твердение бетона, снизить энергоемкость производства. При этом наибольший эффект достигается в бетонах с низким начальным водосодержаннем [3, 4]. Реализация совокупного воздействия на бетон предварительного разогрева и введения ускорителей твердения при обычной технологии связана с большими трудностями, так как при этом резко снижается удобоукладываемость смеси, и, как следствие, возрастает пористость, а вместе с ней уменьшается прочность и долговечность бетона.
При сухом формовании бетона фактор удобоукладываемостн смеси в привычном понимании этого термина отсутствует, в связи с чем ускоренное схватывание цементного геля под воздействием повышенной температуры и химических добавок не оказывает отрицательного влия- нря на его формовочные свойства, оно благоприятствует развитию твердения и Упрочнения цементного камня и бетона.
Повышение температуры вызывает ускорение диссоциации клинкерных минералов на ноны вследствие увеличения кинетичсской энергии молекул твердой и жидкой фаз. Образующийся при этом ионный раствор быстро пересыщается, чем интенсифицируется ионообмен и образование зародышей центров кристаллизации. Этим процессам способствует введение Б горячую бетонную смесь электролитов, пептизирующе действующих на твердую фазу и ускоряющих в первые часы трансформацию цементного геля в камневидное состояние. В результате уже через 6...12 ч твердения в естественных условиях бетон набирает прочность, достаточную для распалубки, транспортирования и складирования изделий. При этом разогрев сухой бетонной смеси целесообразно осуществлять, используя горячие заполнители, температура которых после высушивания 70...85°С.
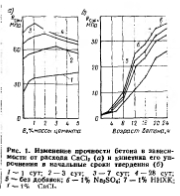
Для практической проверки проведи эксперименты, в которых использовали портландцемент Волковыского цементного завода 36,5 МПа, Кн.г=0,27 и рц = 3100 кг/м3; щебень гранитный прочностью 80 МПа фракции 5...20 мм и песок природный стандартной гранулометрии. Сухую бетонную смесь оптимального состава [5] (Ц=360 кг, Щ-1250 кг. и = 810 кг) помешали в формы с ребром i0 см и уплотняли в течение 60 г вибрированием с частотой 50 Гц и амплитудой 0.5 мм при величине пригруза 0,015...0.025 МГ1а. Затем горячую смесь насыщали водой или раствором добавки, имевшими такую же температуру, под давлением 0,3 МПа и снова вибрировали 60 с при тех же параметрах.
В начальной стадии эксперимента установлено влияние расхода ускорителе? твердения (СаСЬ, NajSO. ННХК) кг прочность холодного бетона (120°С) Оказалось, что прочность бетона в различные сроки твердения не однозначно зависит от расхода химической добавки (рис. 1). Например, в возрасте 1 сут прочность тем выше, чем больше введено ускорителя твердения независимо от его вида; к трем суткам прочность бетона с 5% СаС12 и ННХК оказалась ниже, чем при расходе 3%. В более поздние сроки оптимальный расход добавки снижается и составляет для СаС12 и ННХК к возрасту 28 сут—1%, для Na2S04—1...2%.
Приняв расход ускорителя 1 % 33 оптимальный, установили, что через 10...12 ч твердения образцов в формах под влагоизолирующей пленкой на воздухе при. температуре I« 20°С прочность бетона с добавками составляет 15...25 МПа, что обеспечивает возможность распалубки, транспортирования и складирования изделии для последующего (по мере необходимости) дозревания бетона до набора отпускной прочности (рис. 2).
Влияние предварительного разогрева на прочность бетона исследовали на образцах, твердевших в различных условиях — одну серию в формах укрывали влагоизолирующей пленкой и выдерживали 24 ч при ( = 20°С, после чего образцы распалубливали и хранили до испытаний в нормально-влажностных условиях; другую серию распалубливали немедленно после повторного вибрирования и сразу же помешали в камеру нормально-влажностного твердения; третью серию образцов в формах укрывали влагоизолнрующей пленкой и помещали на 24 ч в теплоизолирующий кожух из пенопласта, чем создавали термосные условия твердения бетона; после распалубки образцы хранили в нормально-влажностных условиях. В результате установлено, что выбор оптимальной температуры предварительного разогрева бетона зависит от условий его твердения — при немедленной распалубке изделий разогрев не должен превышать 40°С, при твердении нх в форме с влагоизоляцией поверхности целесообразен разогрев до 60°С. при этом наблюдается ускорение роста прочности бетона в раннем возрасте; так, к 12 ч твердения она составляет 15...20 МПа вместо 10... 12 МПа для бетона с начальной температурой 20°С, однако к 28 сут твердения прочность разогретого бетона практически равна прочности холодного бетона. Наиболее интенсивно процесс упрочнения происходит в условиях термоса — через 20 МПа, через 12 ч —до 35 МПа и к 24 ч — до 45 МПа для образцов бетона с начальной температурой 60°С.
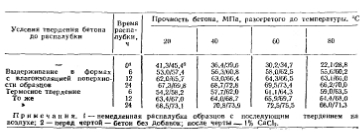
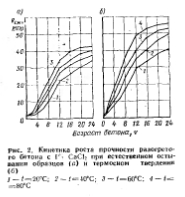
Следовательно, применение предварительного разогрева сухой бетонной смеси в сочетании с введением ускорителей твердения позволяет через 8...10 ч твердения в естественных условиях или 6... 8 ч термосного вызревания получать бетон прочностью 15...30 МПа. Учитывая, что в условиях заводского производства отформованные изделия после выдерживания дозревают на воздухе, необходимо проследить изменение прочности бетона при распалубке образцов через 0, 6, 12 и 24 ч и твердении их в течение 28 сут в помещении при влажности воздуха «60% и температуре <«20°С (см. таблицу).
Приведенные данные свидетельствуют о том, что увеличение времени выдерживания в условиях, обеспечивающих влагоизоляцию поверхности образцов, способствует росту прочности как холодного, так и разогретого бетона. Наибольший эффект отмечен при термосном выдерживании в течение 24 ч, поскольку в этом случае ускоряется гидратация цемента и большее количество жидкости переходит в связное состояние в начальный период твердения. Этим ограничивается развитие процесса обезвоживания бетона при последующем твердении на воздухе. Так, к 28 сут воздушного твердения немедленно распалубленные образцы из разогретого до 60°С бетона потеряли до 50% воды затворения, в то время как твердевшие первые 24 ч под влагоизолирующей пленкой и в условиях термоса — не более 20 и 15%. Испарение жидкости из бетона с низким начальным водосодержаннем (В/Ц=0,26...0,28) замедляет гидратацию цемента и увеличивает пористость цементного камня, в результате чего снижается прочность бетона. Таким образом, выдерживание в течение 12...24 ч предварительно разогретого до 40...60°С бетона в условиях, исключающих потери им влаги, обеспечивает достаточно стабильный рост прочности при последующем твердении на воздухе.
Экономическая эффективность предлагаемой технологии при производстве, например, тротуарных плит складывается из уменьшения расхода цемента, по сравнению с изготовлением их кассетным способом или вибропрессованием на 25...35%, устранения затрат на ТВО заменой ее выдерживанием в естественных условиях и роста долговечности изделий вследствие повышения плотности и прочности бетона. Дополнительные затраты на предварительное высушивание заполнителей составляющие примерно 1 р/м3 бетонит перекрываются экономией от устранения, ТВО, затраты на которую составляли 3...4 р/м3 бетона в изделиях.
Вывод
Применение ускорителей твердения в сочетании с предварительным разогревом сухой бетонной смеси и рациональными условиями твердения бетона создает предпосылки для исключения тепловлажностной обработки изделий из технологического процесса и замены ее выдерживанием в естественных условиях.