
ДОБЫЧА МЕЛКИХ И КРУПНЫХ БЛОКОВ
В настоящее время процесс разработки пильного известняка на мелкие и крупные блоки полностью механизирован. За последние 15—20 лет в СССР создана новая отрасль машиностроения — производство камнерезных машин. Развитие камнедобычи идет по пути создания мощных механизированных карьеров производительностью 200—800 тыс. м3 в год, дающих продукцию минимальной себестоимости (табл. I—7).
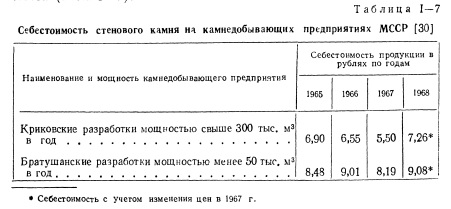
В Молдавии в 1972 г. будет закончено строительство первой очереди Кишиневской шахты мощностью 50 тыс. м3 в год с последующим наращиванием мощности до 250 тыс. м3 в год (к 1975 г.). К этому же сроку предполагается ввести в эксплуатацию вторую очередь Окнипкой шахты мощностью 200 тыс. м3 в год. На территории УССР строится Алексеевский карьер мощностью 800 тыс. м3 стеновых камней и блоков в год. Перечень этих примеров можно значительно продолжить.
В 1958 г. объем добычи пильного камня на карьерах производительностью свыше 100 тыс. м3 составлял 53% от общего объема производства, в 1966 г. — около 74%, а в 1970 г. — свыше 80% [103]. Изготовление стеновых блоков производится по одностадийной либо двустадийной технологии. Первая из них предусматривает выпиливание готовой продукции непосредственно в забое из пласта горной породы. Согласно этому способу добычи дополнительные операции по доводке блоков до стандартных размеров и формы должны отсутствовать.
При двустадийной технологии изготовления блоков первоначально из массива камня выпиливают блоки — заготовки весом 10—12 т, которые разделывают с помощью специальных станков на элементы заданных размеров. В ряде случаев этот способ может быть довольно эффективным, поскольку он позволяет получить продукцию широкого ассортимента и высокого качества. Двустадийное изготовление стеновых блоков применяется в ряде зарубежных стран (Италия, Франция и др.)- В СССР добыча пильного известняка осуществляется преимущественно по одностадийной технологии открытым либо подземным способами, причем в целом по стране превалирует открытый способ разработки (табл. I—8). Это объясняется укоренившимися недостатками подземного способа добычи блоков. К числу этих недостатков прежде всего следует отнести большие потери разрабатываемой горной породы в недрах, достигающие 80—90% от промышленного объема. Остающийся в опорных целиках, кровле и подошве выработок камень оказывается недоступным для разработки. Подземный способ пока не дает возможности полностью механизировать все производственные процессы. Так, в 1969 г. на камнедобывающих предприятиях Молдавии ручными работами было занято 2860 чел., при этом уровень механизации основных производственных процессов достигал лишь 30%. Обычно себестоимость продукции подземных разработок в 1,5— 2 раза выше, чем на открытых карьерах.
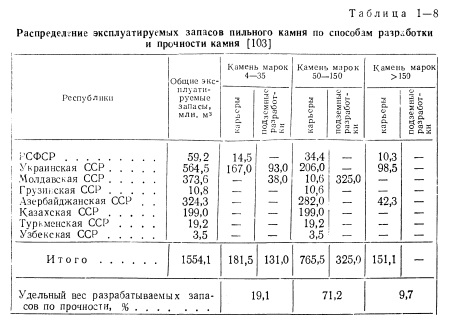
Серьезным недостатком подземного способа добычи блоков является повышенная запыленность шахтного воздуха технологической каменной пылью, образующейся при механизированной разработке известняка. На многих камнедобывающих предприятиях запыленность воздуха достигает 400—600 мг/м3, что в 40—60 раз превышает допустимую норму, помимо этого, применение в подземных условиях машин с двигателями внутреннего сгорании приводит к сильной загазованности шахтной атмосферы. Перечисленные отрицательные моменты подземного способа разработки природного камня привели к тому, что совершенствованию технологии подземной добычи блоков и созданию необходимой техники уделялось недостаточное внимание. Некоторыми специалистами высказывалось мнение о том, что в ближайшие 2—3 года подземная разработка камня должна вообще прекратиться. Тем не менее, в Молдавии, например, до сих пор около 90% стеновых блоков добываются подземным способом. В Одесской области около 55% объема производства камня приходится на долю подземных разработок.
При всех своих недостатках подземный способ добычи блоков имеет и определенные преимущества перед открытым способом разработки камня. Главное из них — отсутствие вскрышных работ. Практика разработки целого ряда месторождений пильного известняка в Молдавии, на Украине, во Франции и Болгарии показывает, что большая глубина залегания пильного слоя камня, высокое значение коэффициента вскрыши, наличие перекрывающих скальных пород являются объективными условиями применения подземного способа добычи камня. При оценке этого способа следует учесть и то, что его применение возможно на застроенных площадях и не связано с поглощением плодородных земель. Между тем карьер с годовой добычей 100 тыс. м3 камня при мощности пласта 2,6 м ежегодно вырабатывает 10 га площади, а, как известно, 1 га пахотной земли дает сельхозпродукции на 500—600 руб. в год [150]. Расчеты показывают, что расходы на рекультивацию 1 га отработанной площади составляют 8—14 тыс. руб. На многих месторождениях выработка поверхностных пластов камня и увеличение коэффициентов вскрыши сверх экономически предельных значений привели к необходимости перехода от открытых разработок к подземным. При этом в ряде случаев такой переход сопровождался снижением себестоимости продукции. Так, на Булдынском месторождении мелкие блоки, добытые в штольнях, оказались на 37% дешевле блоков, выпиленных на карьере.
В 1957—1959 гг. в Молдавии было начато строительство Пашканского, Окницкого и Мало-Милештского карьеров. Ни на одном из них не удалось достичь проектной мощности, а себестоимость стенового камня оказалась выше, чем при подземном способе его добычи.
Эти и другие примеры свидетельствуют о том, что, развивая камнедобывающую промышленность в направлении открытых разработок, необходимо одновременно совершенствовать подземный способ добычи камня. Тем более, что многие дефекты этого способа полностью либо в значительной мере устранимы. Так, например, до недавнего времени очистка шахтного воздуха от технологической пыли являлась одной из специфических серьезных проблем подземного способа добычи камня. В ОИСИ были разработаны конструкции полых режущих органов .камнерезных машин, позволяющие организовать пневмоотсос каменной пыли из-под резцов в момент ее образования. В одной из шахт Булдынского заводоуправления была определена запыленность воздуха при работе камнерезной машины КМАЗ-188, оснащенной обычным цепным баром и полым вибробаром с системой пневмоотсоса пыли. В первом случае средневзвешенная запыленность воздуха у пульта машиниста составила 123,2 мг/м3, а во втором — 8,2 мг/м3 при допускаемой норме 10 мг/м3.
Существенные резервы повышения эффективносги подземного способа добычи пильного известняка содержатся в совершенствовании технологии добычных систем. В современной практике подземной добычи пильного камня применяются три системы разработки: камерная, камерно-столбовая и разработка длинными столбами.
В СССР преимущественное распространение получила камерная система добычи. По этой системе от главных штреков идут камерные выработки, между которыми оставляются опорные целики. Размеры камер и целиков назначаются, исходя из условия обеспечения устойчивости кровли без крепления. В зависимости от прочности и состояния кровли ширина камер изменяется в пределах от 4-х до 7 м, а высота обычно равна 2,4 м (при однослоевой выемке). Длина камер достигает 30 м. В Молдавии на некоторых месторождениях освоена многослоевая выработка камня, при которой коэффициент использования полезного ископаемого существенно повышается. Увеличение ширины камер может быть достигнуто за счет применения анкерной крепи кровли.
К основным недостаткам камерной системы добычи камня относятся низкий коэффициент использования запасов сырья (в пределах 6—12%), постоянное изменение направленности выработок, нарушающее цикличность работы, сложность осуществления оперативного маркшейдерского контроля и большая протяженность всех коммуникаций.
При камерно-столбовой системе разработка горной породы производится первоначально в (камерах, разделенных междукамерными столбами, которые затем разрабатываются обратным ходом. Отработанное пространство обрушивается или заперемычивается. По сравнению с камерной системой камерно-столбовая позволяет увеличить коэффициент извлечения горной породы на 7—12%. Различные разновидности камерно-столбовой системы были применены в штольнях Алексеевского шахтоуправления, на Ильинских шахтах и Должанском месторождении пильного камня. Широкое распространение камерно-столбовая система получила в Канаде, Австрии и США.
Из числа существующих систем подземной разработки наиболее целесообразной считается разработка длинными столбами. По этой системе от основной штольни прокладывают два панельных штрека шириной по 8 м каждый. Расстояние между штреками достигает 60 м. Через каждые 15 м они соединяются между собой галереями шириной 4 м. При этом образуются столбы сечением 50X11 м, которые разрабатываются па глубину 6 м. В результате остаются длинные охранные целики шириной 5 м. При этой системе в целиках остается только около 20% горной массы, обеспечиваются необходимые условия для транспортирования камня и эффективного применения камнерезных машин. По сравнению с камерной системой улучшаются условия проветривания забоев. Возможна многослоевая разработка камня.
Совершенствованию систем подземной добычи пильного известняка посвящен ряд научно-исследовательских работ Молдавского отделения НИИСМИ Министерства промстройматериалов МССР и других организаций.
Значительно успешнее решается вопрос экспериментально-теоретического обоснования рациональной технологии добычи пильного камня открытым способом с использованием различных камнерезных машин. В этой области известны работы М. М. Протодьяконова, М. М. Касьяна, А. П. Петрика, А. М. Столярова и др. Большая работа по обоснованию оптимальных параметров открытых разработок камня выполнена Б. М. Родиным [101]. Им же предложена классификация методов открытой добычи камня. В основу классификации положены: количество одновременно разрабатываемых уступов (слоев), высота уступов, организация работ по вырезке камня из уступа и последовательность получения готовой продукции. По сравнению с подземным, открытый способ разработки камня
характеризуется большим многообразием добычных систем.
В настоящее время в камнедобывающей промышленности страны используется около 30 типов различных камнерезных машин Такое многообразие машин объясняется большим диапазоном изменения прочности пильного камня и непостоянством горно-геологических условий.Подавляющее большинство камнерезных машин предназначено для открытых разработок и только три типа (КМАЗ-188, КМГ-2 и КМГ-3) — для подземных.
В качестве режущих органов камнерезных машин используются дисковые пилы, кольцевые фрезы, режущие цепи и вибробары. Наибольшее распространение получили дисковые пилы диаметром от 800 до 1650 мм. Ими оснащены камнерезные машины СМ-89А, СМ-824, СМ-543, КМ-6, ПТ-38, СМ-518, КМГ-2, КМГ-3 и агрегаты СМ-950 и СМ-828.
НИИ сверхтвердых синтетических сплавов и алмазного инструмента Госплана УССР совместно с НИИСМИ Министерства стройматериалов СССР разработана и внедрена в производство конструкция дисковой пилы со сменными резцами «крупного окола». Одним из преимуществ пилы этого типа является пониженное пылеобразование при распиловке камня.
Основным недостатком дисковых пил различной конструкции является сравнительно малое использование их диаметра (35— 40%), в связи с чем они применяются преимущественно для изготовления мелких блоков. О технико-экономических показателях обычных дисковых пил и пил «крупного скола» можно судить по данным табл. I—9.
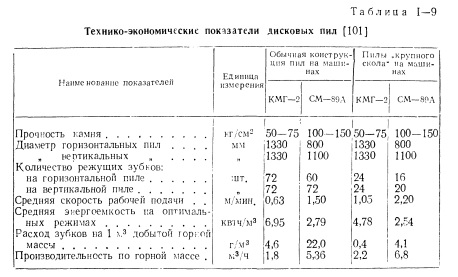
Кольцевые фрезы используются для выпиливания крупных блоков из камня прочностью от 50 до 1200 кг/см2. Коэффициент использования диаметра фрезы составляет 0,65—0,75. Кольцевыми фрезами оснащены камнерезные машины СМ-177А, СМ-580А, СМ-428 и машины тыльной резки агрегата СМ-950. Испытания фрезерных режущих органов на Мало-Милештских (МССР) и Секирянских (УССР) разработках показали достаточную эффективность их применения при разработке известняка прочностью до 500—550 кг/см2. К достоинствам фрез следует отнести устойчивость при работе, в результате чего стенки пропила получаются ровными. Правда, из-за конструктивных особенностей фрез толщина пропила доходит до 45 мм.
Режущие цепи характеризуются высоким коэффициентом использования их длины до 0,80—0,85. При одной и той же глубине резания длина бара с режущей цепью может быть в 2,2—2,6 раза меньше диаметра дисковых пил и в 1,2—1,3 раза меньше диаметра кольцевых фрез.
Цепными барами оборудованы машины КМАЗ-188, СМ-543, КБЯ-35 и машины для поперечных пропилов агрегата СМ-950. Серьезным недостатком баровых режущих органов является их неустойчивость при прохождении пропила. В СКВ Госстроя УССР разработана конструкция двухопорных баров длиной до 2,3 м. В ПИПСМИ создан новый тип режущей цепи со съемными режущими зубками «крупного скола». Испытания цепей этой конструкции, проведенные на Булдынском и Алексеевском карьерах (УССР), выявили увеличение производительности камнерезной машины КМАЗ-188 на 20—25%, снижение энергоемкости резания на 25— 30% и повышение устойчивости в 3—4 раза.
Помимо рассмотренных режущих органов камнерезных машин для распиливания камня в ряде случаев применяют вибробары, абразивные круги и диски с алмазными резцами [5].
В зависимости от рабочего положения относительно добычного уступа камнерезные машины делятся на предуступные, уступные и надуступные [101]. Предуступные машины (КМГ-2, КМГ-3, КМАЗ-188, СМ-824, СМ-950 и др.) располагаются на уровне подошвы уступа (рис. I—3, а). У уступных машин (СМ-580А, СМ-89А п др.) одна опора располагается на кровле добычного уступа, другая — у его подошвы (рис. I—3, б). Надуступные машины (НКМ-2, НКМ-4, СМ-543 и др.) передвигаются по кровле разрабатываемого уступа (рис. I—3, в, г).
По характеру выполняемых технологических операций все камнерезные машины классифицируются на универсальные, специализированные, агрегаты и комбайны. Универсальные машины (КМГ-2, КМГ-3, КМАЗ-188, СМ-89А, СМ-177А, СМ-518, КМ-6, СМ-580А) осуществляют все операции по вырезке камня. Специализированные машины (НКМ-2, НКМ-4, модернизированная модель СМ-89А и др.) выполняют одну либо две совмещенные по времени операции. Агрегаты (СМ-824, СМ-950, СМ-828 (рис. I—4) и др.) состоят из нескольких специализированных машин, осуществляющих в сумме все операции по добыче камня. Комбайны (СМ-543, ПКБ-121, КМ-1) объединяют несколько специализированных машин. Это позволяет избежать перемонтажа режущих органов.
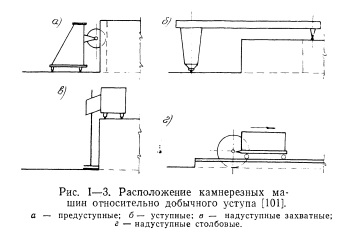
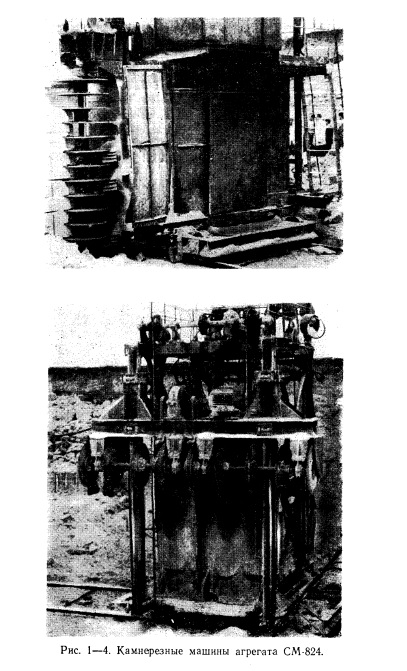
НИИСМИ Госстроя СССР и СКВ Госкомитета стройдормаш разработали типаж камнерезных машин на 1964—1970 гг., согласно которому неэффективные и устаревшие машины сняты с производства и заменены новыми, предназначенными преимущественно для открытых разработок камня [101]. К числу устаревших отнесены все машины, использовавшиеся при подземной добыче. Недостатки этих машин общеизвестны и неоднократно описаны в литературе [5, 6, 30, 101]. Однако пока эти машины (КМГ-2, 3, КМАЗ-188) продолжают оставаться основным средством подземной добычи камня. Высокоуступная машина СМ-825 нуждается в доработке.
В последние годы проектно-конструкторским технологическим институтом МПСМ МССР разработаны и внедрены в производство камнерезные машины новой конструкции, более совершенные, нежели КМГ-2, 3 (рис. I—5).