
ПИРОЛИЗЕР-КАРБОНИЗАТОР ДЛЯ МАЛО- И СРЕДНЕ-МАСШТАБНОЙ ЭНЕРГЕТИКИ
Развитие мирового топливно-энергетического комплекса идет по пути все большего использования твердого топлива как для выработки электрической и тепловой энергии, так и для получения жидкого и газообразного топлива на фоне ужесточения экологических норм. Совершенствование процессов сжигания и термохимической переработки твердых топлив становится одним из главных направлений современной угольной технологии.
Цена на нефть и природный газ возрастает в последнее время заметно быстрее чем на уголь, что делает актуальной задачу замещения, где это возможно, углеводородных топлив углем. Однако и на угольных электростанциях для растопки и стабилизации горения используют мазут или природный газ. К тому же на электростанциях используется мазут с высоким содержанием серы, при сжигании которого образуется большое количество токсичных веществ, оказывающих негативное воздействие на окружающую среду. Также совместное сжигание угля с мазутом приводит к возрастанию механического недожога, снижает КПД котлов, повышает выход оксидов азота, усиливает высокотемпературную коррозию поверхностей нагрева [1], что в целом негативно сказывается на показателях работы электростанций.
В то же время давно существует идея растопки угольных топок на основном топливе, разработано несколько конструкций и способов работы растопочных пылеугольных горелок [2-5]. В основе их лежит принцип частичной газификации угля, позволяющий получить легковоспламеняющуюся смесь, для этого, прежде всего, необходим предварительный прогрев пылевоздушного потока. Различные конструкции растопочных пылеугольных горелок отличаются лишь способом этого предварительного прогрева. Прогрев осуществляется за счет ввода в пылевую трубу плазмы с температурой 5 и более тысяч градусов (Гусиноозерская ГРЭС), либо от электронагревателя сопротивления (предложение Красноярского политехнического института), либо за счет сжигания небольшого (в десятки раз меньшего, чем требуется на растопку) количества мазута или газа.
Большинство регионов России являются импортозависимыми в части топливноэнергетического баланса (например, доля местных топлив в ТЭБ Свердловской области 5%). В связи с чем стоит важная задача - активно вовлекать в использование местный топливный потенциал регионов, представленный в основном низкосортными углями, биомассой и торфом. И если для замещения углеводородных топлив в тепловой энергетике наиболее пригодны качественные каменные угли и антрациты, то для целей газификации как раз предпочтительнее подобные высокореакционные топлива.
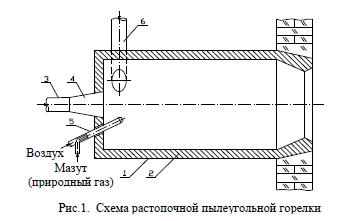
Если ориентироваться на мало- и среднемасштабную энергетику (диапазон мощностей с опорой на материалы Энергетической стратегии России до 2030 г.: малые локальные энергоустановки, промышленно-отопительные ТЭЦ) то для этих целей требуются достаточно простые, недорогие и надежные в эксплуатации устройства, которые позволят либо непосредственно осуществлять растопку пылеугольных котлов, либо получать синтетический газ для его последующей трансформации в жидкое моторное топливо, электрическую энергию и другие энергоносители.
В качестве такого устройства для растопки котлов возможно использование горелки конструкции, подобной разработанной на кафедре тепловых электрических станций УрФУ под руководством профессора Б.В. Берга (Рис. 1) [5].
Растопочная горелка состоит из следующих элементов: стального корпуса 1 с огнеупорной излучающей обмуровкой 2; патрубка подачи пылевоздушной смеси 3 со щелевым (вертикальная щель) устьем 4; двух одинаковых вспомогательных жидкотопливных или газовых низкорасходных горелок 5, размещенных симметрично относительно продольной оси щелевого устья патрубка (выходной части пылевой трубы) и подвода вторичного воздуха 6.
Растопка горелки осуществляется следующим образом. Зажигаются две вспомогательные низкорасходные горелки 5. Затем через патрубки 6 и 3 подаются воздух и пылевоздушная смесь (угольная пыль с первичным воздухом), которая, выходя через щелевое устье 4, приобретает форму плоской струи, вытянутой по вертикали. Струя имеет развитую боковую поверхность и до прогрева обмуровки воспринимает излучением теплоту факелов вспомогательных горелок одновременно с обеих сторон, что позволяет достаточно быстро осуществить предварительный нагрев. После прогрева обмуровки до 700 °С вспомогательные горелки отключаются; дальнейшие газификация, нагрев и воспламенение пылевидного топлива происходят за счет излучения стенок обмуровки, нагрев которых, в свою очередь, поддерживается частичным сжиганием угольной пыли и образующихся горючих газов.
Работа растопочной горелки в автотермическом режиме (за счет тепла выделяемого при сгорании в ней части угля) представляется более эффективной, в связи с чем, в ней поддерживается соответствующее значение избытка воздуха а ~ 0,5 - 0,7. В результате происходит частичная газификация угля с получением газообразного топлива (полугаза) и коксового остатка, а горелка работает в режиме окислительного пиролиза и карбонизации.
Такая растопочная горелка прошла испытания и проверена в эксплуатации на ТЭЦ- 3 города Улан-Батора (Монголия). Горелка диаметром 0,8 и длиной 1 м была установлена на котле БКЗ-75. Две вспомогательные мазутные форсунки по 30 кг/ч мазута разогревают огнеупорную кладку стенок муфеля горелки до 700 °С за 30 минут, после чего идет устойчивое воспламенение пылевоздушной струи за счет излучения от футеровки муфеля без их дальнейшей помощи. Подобная реконструкция позволяет уменьшить расход растопочного мазута в десятки раз.
Однако использование устройств подобной конструкции, работающих при относительно невысоких температурах, для газификации малоэффективно из-за низкого качества получаемого газа. В то же время температурный уровень в реакторе для нужд мало- среднемасштабной энергетики желательно ограничить средними значениями, лежащими ниже температуры шлакования (t < 1100-1200°С), что требует взамен высокотемпературных агрегатов типа Shell, MHI и др. разработки иного, отвечающего этим требованиям, варианта. В качестве такого газификатора предлагается использовать многозонный поточный или слоевой агрегат, позволяющий получить при умеренных температурах бессмольный газ, близкий к идеальному паровоздушному, и (попутно) активированный полукокс.
Основным недостатком однозонных реакторов является экстремальный профиль температур по их длине. В случае полной газификации это с необходимостью понуждает на переход к жидкому шлакоудалению. При работе в режиме карбонизации оплавление минеральных включений в топливных частицах при их случайном сближении может провоцировать развитие когезионных процессов, выпадение агломератов и шлакование ограждающих поверхностей.
Выравнивание профиля температур осуществляется известными физическими (рециркуляция механического недожега (уноса) и возврат части теплоты выводимых из реактора продуктов) и химическими (распределенный зональный ввод реагентов) приемами.
Рассмотрим схему работы адиабатного реактора с зональным подводом окислителя и топлива, продуцирующего при умеренных температурах (1100-1200°С) «бессмольный» топливный газ, близкий по составу к идеальному паровоздушному (СО2, Н2О, СН4 ~ 0), и полукокс, подвергнутый пароуглекислотной активации (рис. 2). Под «бессмольным» будем понимать топливный газ, концентрация конденсирующихся смолистых веществ в котором, проскакивающих в камеру сгорания двигателя, лежит в границах соответствующих ТУ.
В головной части за счет первичного дутья ai на основе окисления части летучих осуществляется стадия нагрева и пиролиза загружаемого свежего топлива. В средней части под воздействием вторичного дутья a2 происходит полное дожигание летучих. В хвостовой части протекает частичная газификация (активация) полукокса газообразными продуктами, поступающими из средней части. Для поддержания автотермичности процесса в эту зону подается третичное дутье a3.
Позонная отработка предлагаемой технологии проведена в лабораторных (диаметр 150 мм) реакторах и опытно-промышленной установке мощностью 200 кВт. Работоспособность всей схемы проверена на однокорпусной опытной установке тепловой мощностью 15 кВт.
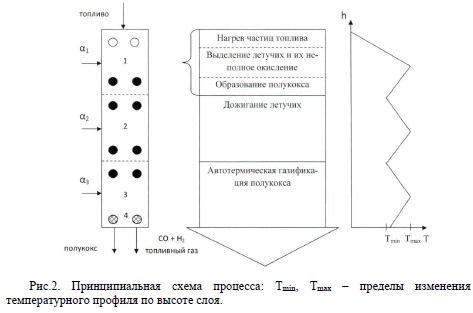
Агрегат подобной конструкции принят за основу для создания пиролизера- карбонизатора угольной ПГУ сбросного типа с топпинг-процессом, разработку которой кафедра ТЭС ведет совместно с УралОРГРЭС. Результаты расчетов схемы ПГУ изложены в [6].