
ПОВЫШЕНИЕ ЭФФЕКТИВНОСТИ ГАЗОНАПРАВЛЯЮЩИХ ЭЛЕМЕНТОВ ТЕХНОЛОГИЧЕСКИХ УСТАНОВОК
Разработанная и одобренная правительством РФ «Энергетическая стратегия России до 2020 г.» и принятая правительством 17 ноября 2001 г. Федеральная целевая программа «Энергоэффективная экономика» предусматривают в числе важных приоритетов резкое повышение эффективности использования топливноэнергетических ресурсов на основе энергосберегающих технологий и оборудования, его совершенствовании и рациональном практическом применении.
Актуальность рассмотрения вопросов экономии энергии именно при тепловой сушке обусловлена тем, что последняя характеризуется высокой энергоемкостью. Согласно [1] расход котельно-печного топлива на сушку только по девяти энергоемким отраслям промышленности России (химической, машиностроительной, угольной промышленности и др.) составляет около 2 % т.у.т. В то же время средний КПД сушильных установок редко превышает 33 %. Повышение КПД сушильных установок (СУ) вдвое позволило бы экономить ежегодно 50-55 млн. т.у.т., что составляет около 30 % планируемого ежегодного объема экономии по стране.
Частью проблемы обеспечения необходимых качественных показателей продукции и экономии топлива, энергии и капитальных затрат является рассмотрение задачи интенсификации сушки. Для решения подобной задачи необходимо проводить широкомасштабные исследования и разработки с целью создания современных СУ.
Для разработки методов инженерного расчета и анализа СУ необходима информация о процессах, развивающихся в их элементах. Однако часто такая информация по своему объему недостаточна и требуется принятие конкретных технических решений в условиях неопределенности. Тогда особенно эффективно применение методов математического моделирования сушильных и смежных процессов на ЭВМ, а также комплексных экспериментальных исследований гидродинамического совершенства существующих рабочих камер и технологических процессов как в промышленных, так и лабораторных условиях.
Общая производительность сушильного цеха деревообрабатывающего завода ОАО «Целлюлозно-картонный комбинат», где установлено 24 сушильных камеры для термообработки пиломатериалов финской фирмы «Валмет», составляет 354000 м3/год. Сушильные машины непрерывного действия с продольной циркуляцией воздуха и поперечным размещением штабелей в камере предназначены для сушки пиломатериалов [2] при изготовлении деталей и строганных заготовок авто-вагоно- сельхозмашиностроения до транспортного влагосодержания 18-22 %, а также с
эксплуатационным влагосодержанием 8-12 % для производства мебели. Сложность задачи выявления резервов рационального энергоиспользования усугубляется наличием в крупногабаритных СУ неравномерности скорости сушки, а значит и неравномерности тепло- и массообмена, в различных зонах по высоте штабелей пиломатериалов, что во многом предопределяет технологический брак выпускаемой продукции, а также дополнительный рост нерасчетных капитальных и энергетических затрат.
Так, например, до 3-4 % высушиваемого материала имеют не только повышенное влагосодержание, но и брак в виде коробления и растрескивания, которые также проявляются и в готовых изделиях.
Основная причина подобных дефектов заключается в образовании недопустимо больших остаточных внутренних напряжений при нарушениях режимов сушки из-за неравномерности распределения полей скоростей сушильного агента по поперечному сечению рабочей камеры, а значит и полей влагосодержаний и протекающих тепло-и массообменных процессов в материале вследствие различного к нему энергоподвода.
Последнее подтверждается прямым промышленным экспериментом, проведенным с целью оценки аэродинамических характеристик в одной из камер сушки. Исследование скоростного режима сушилки было проведено на участке подачи и распределения сушильного агента в рабочую камеру. В рабочей зоне СУ размещается поперек потока сушильного агента 12 штабелей пиломатериалов, в каждом по три вертикально расположенных пакета, в одном пакете 8 м3 досок (рис. 1).
Продольная циркуляция сушильного агента осуществляется тремя осевыми вентиляторами суммарной производительностью 210000 м3/час. Установка работает с частичной рециркуляцией сушильного агента (около 4,5 %), который подогревается с помощью ребристых паровых калориферов до температуры 45-65 оС. Периодически с интервалом порядка 12 часов один штабель высушенного материала удаляется через герметичные двери участка подачи агента сушки, другой подается в противоположном загрузочном конце СУ.
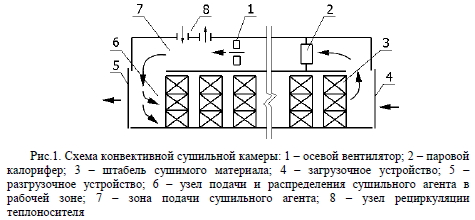
Очевидно, что различная скорость сушки по высоте штабелей обуславливается неодинаковыми гидродинамическими условиями, что подтверждается результатами опытного исследования аэродинамики камеры на «холодных» режимах. Так, например, отмечается значительная неравномерность как продольных (вблизи торцов пиломатериалов рост скорости сушильного агента до 25 %), так и вертикальных профилей скорости (падение скорости до 50 %, а также наличие обратных потоков в верхней и повышение скорости почти в 2 раза в нижней части камеры) в рабочей зоне участка подачи и распределения теплоносителя (рис. 2, А).
Выравнивание профилей скорости сушильного агента, а значит и выравнивание процессов тепломассопереноса влаги по сечению материала за счет перераспределения потока теплоносителя, исключение застойных зон и т.д., то есть умение управлять аэродинамической обстановкой в рабочей зоне СУ, приводит к снижению брака из-за неравномерности сушки как по высоте, так и ширине штабеля пиломатериалов и, соответственно, к снижению нерасчетных эксплуатационных расходов.
Варьирование скоростью теплоносителя в локальных зонах приводит в них и к изменению его расхода G кг/с, который однозначно связан с количеством подводимого тепла к сушимому материалу:
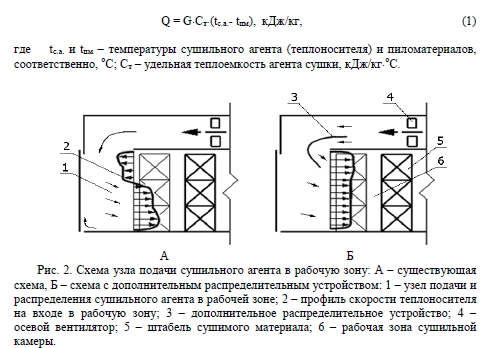
Данные численных исследований процессов гидродинамики и тепломассообмена, проведенных с помощью вычислительного комплекса PHOENICS, также достаточно хорошо согласуются с экспериментальными данными и весьма актуальны для поиска рациональных аэродинамических режимов работы различных теплотехнологических агрегатов при рассмотрении подобного рода задач [3,4,5,].
Поиск факторов для оптимизации аэродинамической обстановки начального (разгрузочного) участка камеры проводился на разработанной и изготовленной в масштабе 1:50 модели отмеченной ранее СУ. Измерение профилей скорости в лабораторных условиях проводилось с помощью прецизионной термоанемометрической аппаратуры отечественного производства, работающей в режиме постоянной температуры в комплекте с однониточным стандартным датчиком с диаметром нити 5 мкм. Осредненные профили потоков измерялись с помощью миниатюрного щелевого насадка полного давления в комплекте с микроманометром с наклонной трубкой. Скорости воздушных потоков менее 0,6 м/с замерялись с помощью термоанемометра. На специально разработанной аэродинамической установке [3] проводились тарировки зондов термоанемометра и пневмотрубок. Направление аэродинамических потоков определялось с помощью флажка. Режим течения - турбулентный, число Рейнольдса составило Red = 2,3-10 . Измерение динамических характеристик потоков на опытном стенде и при прямом промышленном эксперименте проводилось в 7-ми вертикальных сечениях узла подачи и распределения сушильного агента 1 (рис. 2, А).
Каждое такое сечение разбивалось на 80 квадратов (поперечное сечение реальной сушильной установки: высота - 7,7 м, ширина - 7,0 м). В каждом квадрате определялось осредненное значение скорости в направлении максимального вектора. Средняя скорость потока при лабораторных исследованиях в рабочей зоне соответствовала скорости сушильного агента при промышленных испытаниях сушильной машины и составляла порядка 3,5 м/с.
Анализ эпюр скоростей в узле подачи и распределения сушильного агента как по вертикальным, так и по горизонтальным сечениям (10 горизонтальных сечений по высоте рабочей зоны - 5,3 м) показал наличие (особенно в вертикальном сечении - непосредственно перед первым штабелем сушильного материала) обширной застойной зоны с обратным движением теплоносителя (рис. 2, А) в верхней части на входе в рабочую зону камеры 6.
Последнее предопределяет неблагоприятные условия для сушки не только для верхнего пакета первого штабеля, но и, очевидно, для последующих штабелей сушимого материала по длине рабочей зоны. Выравнивание профиля скорости на входе в рабочую зону перед первым штабелем пиломатериалов приведет к равномерному распределению теплового потока, а значит и интенсивности сушки по высоте штабеля.
Для достижения этой цели была проведена серия экспериментов, в которых с помощью дополнительного распределительного устройства в виде фасонной пластины разной конфигурации осуществлялось перераспределение потока теплоносителя во входном сечении рабочей зоны камеры сушки.
В конечном итоге были определены такая форма и место расположения распределительного устройства, которые позволили получить практически равномерную эпюру скорости (рис. 2, Б) перед первым штабелем сушильного материала. Равномерный энергоподвод, а значит и равномерная интенсивность сушки пиломатериалов, позволяет не только снизить технологический брак из-за повышенного влагосодержания, но и улучшить качество выпускаемой пилопродукции за счет уменьшения пересыхания материала.
Снижение брака по указанным выше причинам только на 1 % позволит в год получить дополнительно порядка 146 м кондиционной продукции на одну сушильную камеру или около 3504 м3 в целом по заводу. Работа имеет практическое применение.