
Оценка качества железобетонных элементов неразрушающими методами
Ультразвуковые, радионзотопные, магнитные, вибрационные и другие неразрушающне методы в промышленных условиях широко применяются для определения прочности и плотности бетона, толщины защитного слоя, диаметра арматуры, несущей способности отдельных конструкций. Результаты контроля физико-механических параметров бетона позволяют характеризовать качество готовой продукции. Неразрушающие методы испытаний и оценки качества обладают рядом достоинств: не повреждают испытываемый элемент и тем самым не снижают его прочности; требуют сравнительно небольших затрат времени; позволяют определять требуемые характеристики в любой доступной точке элемента или детали. К недостаткам относят то,что значение контролируемой величины А (например, прочности бетона) определяется по значениям косвенного показателя КП (время прохождения ультразвука, диаметр отпечатка после вдавливания штампа и т. п.), причем зависимость А — КП является не функциональной, а корреляционной, т. е. справедлива только в среднем для большего числа измерений. Кроме того, для неразрушающих испытаний обычно используют сложную современную аппаратуру (ультразвуковую, радиоизотопную, и др.),что требует наличия специальных знаний у обслуживающего персонала.
По своей сущности неразрушающие методы допускают многократное испытание элемента или детали и тем самым позволяют получать большой объем информации. Это позволяет значительно повысить точность измерений. В настоящее время статистическая обработка результатов сравнительных испытаний механическими неразрушающнми методами показывает, что неразрушающие методы контролируют прочность бетона с погрешностью не более 15 %, плотность тяжелых бетонов и легких — до 2,5 %, защитный слой бетона — до 2 %, диаметр арматуры — до 5 %, влажность исходных материалов — до 4,5 %. Вместе с тем необходимы громоздкие вычисления в процессе статистической обработки результатов. Поэтому дальнейшее развитие неразрушающих методов контроля будет идти по пути механизации и автоматизации испытаний и обработки их результатов.
Ультразвуковой импульсный метод определения прочности бетона (ГОСТ 17624—78) является наиболее распространенным из неразрушающих методов. Он основан на возбуждении в испытываемом элементе ультразвуковых акустических колебаний (более 25 кГц) и измерении скорости их распространения. Известно также, что прочность бетона непосредственно связана с его плотностью, что позволяет по скорости прохождения ультразвука в бетонном или железобетонном элементе определять прочность бетона.
Обычно используют серийно выпускаемые приборы УФ-90ПЦ, УК-10П, УК-16П, «Бетон-8УРЦ» и др. Эти приборы позволяют передавтаь импульсы акустических колебаний (продольных или поперечных) в бетон и принимать их из бетона посредством специальных преобразователей. Последние являются взаимозаменяемыми, т. е. любой из преобразователей можно использовать в качестве излучателя, тогда другой становится приемником. Излучатель передает акустические колебания частотой 25, 60, 80 или 150 кГц, причем не непрерывно, а сериями (импульсами) с частотой повторения 50 Гц.
Преобразователи можно приклеивать или просто прижимать к поверхности бетона. Клей должен обеспечивать хороший акустический контакт, прочно удерживать его в процессе испытания и позволять снимать без повреждений после окончания эксперимента. В качестве клея используют пластилин (для преобразователей продольных волн), эпоксидную смолу ЭД-6 без отверднтеля (для пребразователей поперечных волн), воскоканифольный компаунд (для преобразователей обоих типов).
Преобразователь к бетону можно прижимать специальными приспособлениями или просто рукой. Конструкция приспособлений должна исключать возможность прохождения ультразвукового импульса к приемнику по элементам самого приспособления. В месте прижима поверхность бетона смазывают для обеспечения хорошего акустического контакта. В качестве смазки применяют технический вазелин, вязкое машинное мае по, солидол, жидкое мыло, эпоксидную смолу без отверднтеля и др. Мелкие раковины и шероховатости выравнивают быстр отвердеющим гипсовым раствором или пластилином, а при наличии существенных неровностей их предварительно сглаживают механическим путем.
Для измерения скорости прохождения ультразвука используют различные схемы. Сквозное прозвучивание (рис. 16.1, а, б) применяют, если доступны обе поверхности элемента, в противоположном случае используют поверхностное прозвучивание (рис. 16.1 в).
Чтобы определить кубиковую или призменную прочность бетона ультразвуковым методом, измеряют время прохождения колебаний через бетон. Прочность бетона исследуемого изделия определяют методом тарировочных кривых. Тарировочную кривую для бетона данного состава строят путем измерения скорости прохождения колебаний на 4...5 стандартных бетонных кубах (призмах), причем сначала измеряют скорость прохождения колебаний, а затем определяют прочность бетона обычными механическими испытаниями в прессе.
Для получения надежной тарировочной кривой необходим достаточно широкий диапазон прочностей при механических испытаниях. Этого достигают уплотнением бетонной смеси в различных образцах, вариацией режимов термообработки или испытанием образцов одной партии в различном возрасте.
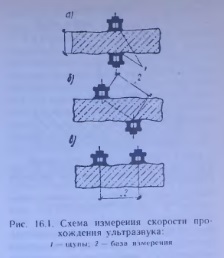
Разновидностью ультразвукового импульсного метода является методика контроля прочности бетона с учетом частотных характристик ультразвукового сигнала. Она предназначена для контроля прочности бетонов неизвестного состава без проведения предварительных тарировочных испытаний и без построения тарировочных кривых. При этой методике учитывают не только скорость распространения ультразвукового сигнала, но и свойства бетона как частотного фильтра, для чего измеряют значения первых двух полупериодов сигнала и амплитуды.
Расположение участков, где должна определяться прочность бетона, зависит от вида и размеров конструкции (изделия), особенностей ее работы и технологии изготовления. Например, часть участков в изгибаемых элементах обязательно располагается в расчетных сечениях. Расположение таких участков должно быть указано проектной организацией в рабочих чертежах. Контроль конструкций (изделий) может быть выборочным или сплошным. При выборочном способе количество контролируемых конструкций (изделий) должно быть не менее 10 % их общего числа в партии, но не менее 3 шт. Примерная схема организации выборочного контроля качества плоских плит перекрытий и панелей внутренних стен, изготовляемых кассетным способом такова. Прочность бетона каждого контролируемого изделия определяется как минимум на трех участках, которые расположены посередине пролета в плитах перекрытия и у верхней грани панелей внутренних стен. Для контроля отбирают не менее 10 % изделий, изготовляемых в смену (партии), и не менее одного изделия из кассеты. Если какое-либо изделие показало заниженную прочность, то оценку партии производят повторно, а изделия, изготовленные в той же кассете, подлежат сплошному контролю.
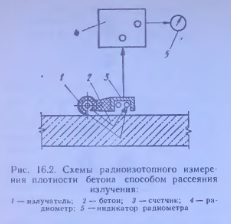
Радиоизотопный метод определения плотности бетона (ГОСТ 17623— 78) основан на том, что при прохождении через бетон гамма-излучений интенсивность последних снижается, причем это снижение зависит от плотности и прочности бетона. Источником радиоактивного излучения обычно является кобальт-60, обеспечивающий проникновение излучения в бетон на глубину до 80 см. Существует две разновидности метода — способ сквозного просвечивания и способ рассеяния излучения (рис. 16.2). В радиометре обычно используется принцип измерения количества электрических импульсов, возникающих в результате воздействия лучей на газовый катодный счетчик. Определение плотности бетона, как и в случае ультразвукового контроля плотности, производят по тарировочной кривой. В этом методе особое внимание необходимо обращать на выполнение требований охраны труда, чтобы избежать воздействия гамма-излучений на обслуживающий персонал.
Методы рентгенографии и радиографии. При испытаниях железобетона рентгенографию и радиографию применяют для контроля положения, количества и диаметра арматуры в железобетоне, а также для нахождения различного рода дефектов в самом бетоне: расслоений, каверн, недоуплотнений. Регистрация излучений производится чаще всего с помощью рентгеновских пленок. Рентгеновские мелкозернистые пленки имеют с обеих сторон светочувствительный слой. Только 1...2 % падающего на пленку излучения взаимодействует с ней и вызывает ее почернение. Чтобы увеличить почернение пленки и соответственно уменьшить время облучения, с обеих сторон помещают усиливающую фольгу, в качестве которой может служить фольга как из солей, так и из тяжелых металлов. Например, фольга из вольфрамата кальция флюоресцирует, что приводит к дополнительному почернению пленки. Время экспозиции можно таким образом уменьшить в 4...8 раз.
При использовании рентгенографии и радиографии чаще всего применяют метод сквозного просвечивания. Фокус рентгеновской трубки или радиоактивного источника гамма-излучения находится на одной стороне испытываемой конструкции, а пленка — на противоположной. Расстояние «излучатель — пленка» должно быть примерно в 3...10 раз больше, чем толщина строительной конструкции. При этом пленка должна плотно прилегать к поверхности конструкции, что позволяет уменьшить искажение изображения. Расстояние «излучатель — пленка» определяет время экспозиции, которое может составлять от нескольких минут до нескольких часов и зависит от квадрата расстояния «излучатель — пленка», в связи с чем это расстояние нельзя чрезмерно увеличивать. Если требуется определить диаметр и положение арматуры в железобетонных конструкциях, то рекомендуется применять метод двух источников. Снимки производят дважды на одну и ту же пленку при параллельном смещении источника. При использовании метода двух источников для каждого арматурного стержня на пленке получается два отпечатка; взаимный сдвиг отпечатков должен быть измерен с максимальной точностью. Если арматура расположена тесно, целесообразно получить два снимка, радиографию с простым облучением и радиографию со сдвигом источника.
Радиография (ГОСТ 17625—83) находит также применение для контроля заполнения швов и стыков, пустот в бетоне и каналов для арматуры с предварительным натяжением. Особенное значение такой контроль имеет для ответственных сооружений, требующих высокого качества выполнения работ. Рассмотрим практический случай применения радиографии для контроля заполнения каналов цементным раствором. При проведении контроля железобетонной вертикальной цилиндрической осветительной башни, армированной предварительно напряженными канатами, было осуществлено более 200 радиографических снимков. Контроль заполнения каналов цементным раствором проводился преимущественно в зоне верхнего крепления канатов. Источником излучения служил кобальт-60. Источник гамма-излучения помещался в свинцовом рабочем контейнере массой 300 кг. По вертикальной оси осветительной башни на определенной высоте располагался рабочий контейнер с источником. Пленки укреплялись на внешней стороне осветительной башни на требуемой высоте. Это позволяло получить панорамный снимок для каждого уровня по высоте башни. Если обнаруживалась незаполненная полость, ее можно было тут же заполнить цементным раствором.
Радиография применяется и для контроля сварных соединений в железобетонных конструкциях. При проведении радиографии сварочных швов для обеспечения хорошего изображения в качестве гамма-излучателя применяют иридий-192. Если же необходимо достичь лучшей выявляемости дефектов, проводят радиографию с использованием источника кобальт-60.
Магнитные методы (ГОСТ 22904—78). Магнитные характеристики арматуры в железобетонных конструкциях существенно отличаются от магнитных характеристик бетона. В настоящее время разработаны и внедряются приборы-зонды для определения диаметров и положения арматуры в железобетоне, где используется это различие магнитных свойств.
Основой методики измерений магнитными зондами является оценка изменений в магнитном поле, возникающих при введении в него ферромагнитного материала. Зонд при работе передвигается и поворачивается на поверхности испытываемой железобетонной конструкции до тех пор, пока показания на шкале регистрирующего прибора не достигнут максимума. Поворотом измерительного зонда на 180° (перпендикулярно поперечной оси) можно установить параллельность положения арматуры относительно поверхности конструкции. Толщину защитного слоя можно измерить как методом двойной радиографии, так и с помощью магнитного зонда. Если с помощью радиографии выяснено положение, количество и диаметр арматуры, то можно определять магнитным методом толщину защитного слоя от 10 до 40 мм с точностью ± 2 мм, а для защитного слоя толщиной от 10 до 80 мм — с точностью ± 3 мм. Применение магнитных зондов особенно эффективно для слоев толщиной менее 150 мм, причем они дают более точные результаты, чем двойная радиография, и более экономичны при толщинах менее 50 мм.
Приведем примеры определения толщины защитного слоя. Для сборных элементов плотины размеров 6000 X 1000 X 90 мм требовалось установить положение арматурных каркасов, так как возникли подозрения, что при изготовлении они были перевернуты. Элементы были армированы перекрестно, расстояние между арматурными стержнями по проекту составляло в одном направлении 200 мм (диаметр 10 мм), а в другом — 300 мм (диаметр 8 мм). Результаты радиографии при толщине 90 мм и измерения магнитным зондом показали, что арматурные каркасы были смещены примерно на 10 мм к внешней стороне относительно проектного положения. Выяснилось, что для определения толщины защитного слоя целесообразно применять комбинацию из двух методов: магнитного и радиографического. Сопоставление этих методов показало, что измерения защитного слоя толщиной менее 150 мм магнитным зондом являются более точными, чем при двойной экспозиции во время радиографирования. Для бетонных конструкций с неизвестным количеством и диаметром арматуры магнитным зондом можно измерять толщину защитного слоя с точностью 3 мм.
На заводе железобетонных конструкций измеряли толщину защитного слоя бетона на несущих железобетонных элементах. Для измерения использовали прибор ИЗО-10Н, основанный на применении электромагнитного метода определения толщины защитного слоя бетона и расположения арматуры. Этот метод применяют при производственном и инспекционном контроле качества конструкции по ГОСТ 8829—77 и 22904—78, а также при проверке качества конструкций в процессе эксплуатации. Вначале проверялось соответствие показаний прибора ИЗС-10Н реальной толщине защитного слоя бетона в плитах перекрытий из тяжелого бетона. С этой целью перед началом эксплуатации прибора ИЗС-10Н в заводских условиях была произведена градуировка на отдельных стержнях и на каркасе плиты перекрытия. Для получения градуировочной зависимости изготовили специальный стенд размером 50 х 30 х 20 см, толщина защитного слоя бетона при этом имитировалась с помощью фанерных листов различной толщины. Испытания проводили для стержней, применяемых при изготовлении каркасов плит. В данном случае для установления градуировочных зависимостей «показания прибора — толщина защитного слоя» использовали арматурные стержни диаметром 8 и 10 мм, длиной 60 см каждый.
Измерения на панелях проводили по следующей методике: на выходящих из пропарочной камеры панелях выбирали три контрольных сечения, два из которых расположены по краям и одно — в середине пролета конструкции. В каждом сечении измеряли толщину защитного слоя бетона для двух стержней поперечной рабочей арматуры; с помощью измерителя защитного слоя ИЗС-10Н в намеченных к контролю сечениях определяли направление и расположение рабочих стержней арматуры и каркасов плиты; расположение арматурных стержней размечали на поверхности плиты карандашом; снимали по шесть измерений на каждом стержне поперечной арматуры. При обработке результатов определяли среднюю толщину защитного слоя бетона а для отдельных стержней и в целом по конструкции, а также значения коэффициента вариации и среднеквадратического отклонения толщины защитного слоя. Минимальные измеренные значения а для отдельного стержня составляли 5,0 мм, для плиты а = 8,1 мм, а максимальные соответственно 16,2 и 15 мм. Среднее значение защитного слоя за анализируемый период было равно 12,3 мм. Остановлено, что практически для всех проконтролированных панелей толщина защитного слоя меньше проектной (равной 15 мм), а в 50 °о случаев она значительно меньше (9... 10 мм).
В результате проведенной работы было принято решение об оснащении существующего стенда неразрушающего контроля прибором ИЗС-10Н для организации систематических магнитных измерений на технологической линии с целью обеспечения соответствия фактических характеристик армирования проектным значениям. Это позволит обеспечить изделиям необходимую прочность и трещиностойкость, а также предотвратить коррозию арматуры.
Термодефектоскопия строительных конструкций. В связи с последними достижениями в области инфракрасной (ИК) техники начали применять (в комплексе с другими методами) тепловую дефектоскопию. Современные приборы ИК-тепловизоры — как черно-белые, так и цветные, позволяют получать изображение температурного поля; при этом по степени почернения и диапазону цвета можно дать полю достаточно точную количественную оценку. Эти приборы имеют высокое температурное разрешение (до 0,05 °С); дистанционность измерения; полностью исключается механический и тепловой контакт, возмущающий температурное поле на измеряемой поверхности; пространственное разрешение может составлять доли миллиметра (до 400 линий на 1 мм); возможно осуществлять обзор очень малых (до сантиметров) и очень больших (до сотен метров) объектов; один и тот же прибор может охватить диапазон температур от 0 до 500 С.
Ограничения теплового метода обусловлены некоторой инерционностью теплового потока, из-за которой тепловое изображение на поверхности изделия несколько «размывается».
Чувствительность (или способность к обнаружению минимального дефекта) в основном зависит от отношения коэффициентов теплопроводности изделий и дефекта.
Возможны три схемы дефектоскопии: 1) изделие нагревается во всем объеме до 100°С (в частности, в процессе термовлажностной обработки) и затем остывает при температуре наружного воздуха; 2) над поверхностью изделия движется с заданной постоянной скоростью нагреватель в виде нити с рефлектором, а на известном расстоянии, определяемом экспозицией температурного поля, движется детектор ИК-излучения (тепловизор), измеряющий температуру поверхности; 3) в схеме, аналогичной приведенной, детектор и нагреватель движутся по разные стороны изделия.
Тепловизоры можно также использовать для наблюдения за полем температуры на поверхности железобетонных изделий после термической обработки, что позволит уточнить методику предотвращения трещинообразования. При посредстве тепловизора можно регулярно наблюдать кинетику поля температуры на поверхности массивных бетонных сооружений (блоков плотин) для точного и дистанционного определения граничных условий с целью расчета термонапряженного состояния.
Одной из самых перспективных областей применения тепловизоров является их использование при обследовании зданий различного назначения с целью выявления дефектов теплоизоляции в ограждающих конструкциях, а также конструктивных недостатков. Тепловизоры позволяют фиксировать распределение температуры как на внутренней, так и на наружной поверхностях ограждающих конструкций зданий. Лучше всего проводить эти исследования зимой, когда контрасты температуры между зданиями и окружающей средой максимальны. Вначале проводят тепловой контроль наружной поверхности здания и отмечают места возмущения температурного поля. Затем отмеченные места обследуют более тщательно с внутренней стороны и определяют размеры, характер и возможную глубину залегания предполагаемого дефекта (при термографировании с внутренней стороны место расположения дефекта будет холоднее, чем бездефектные участки конструкции). Полученные термограммы дефектных мест сравниваются с термограммами заведомо бездефектных конструкций или с заранее известными типами дефектов.
В ходе испытаний были выявлены, например, места недостаточной теплоизоляции стыков и панелей, усадки теплоизоляции, локальных скоплений влаги, различных трещин и щелей в ограждениях, места, где отсутствовали уплотнители между оконными рамами и т. д. Наличие обнаруженных дефектов подтвердилось при вскрытии отмеченных участков конструкций. Обследования с помощью тепловизоров помогают четко определить характер дефекта, его местонахождение и размеры и наметить способы устранения.
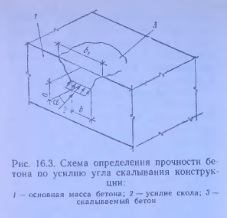
Определение прочности бетона по усилию скалывания угла конструкции заключается в скалывании выступающего угла конструкции усилием, которое приложено к поверхности под углом, отличным от прямого (рис. 16.3). Для создания и измерения скалывающего усилия обычно используют прибор типа ГПНВ-5.
Определение прочности бетона методом отрыва со скалыванием (рис. 16.4). Метод основан на определении прочности бетона при сжатии усилием, необходимым для местного разрушения бетона при вырыве из него специального анкера (рис. 15.4). Местное разрушение бетона и относительная трудоемкость метода компенсируются его довольно высокой точностью.
Анкеры могут быть установлены и заанкерены в бетоне конструкции как при ее изготовлении, так и после; в последнем случае в бетоне необходимо проделать шпур, и ввести в него анкер в виде разжимного конуса. Возможна также заделка анкерного устройства с помощью эпоксидного клея. Для вырывания анкеров используют приборы ГПНВ-5 и ГПНС-4, представляющие собой портативные пресс-насосы. Разработан также новый прибор ГПНО-5, позволяющий испытывать как обычные, так и тонкостенные конструкции (с использованием укороченных анкеров), выполненных из бетона классов до В75. Определение прочности бетона методом отскока (ГОСТ 22690.1—77) основано на статистической связи между упругостью бетона, характеризуемой величиной упругого отскока, падающего на него металлического шарика, и прочностью бетона. Для определения величины упругого отскока используют приборы типа КМ, молотки систем Шмидта, КНСИ, ЦНИИСКа и др. Определение прочности бетона производят по тарировочной кривой, для построения которой, как и в ультразвуковом методе, необходимо предварительно провести параллельные испытания, т. е. на одних и тех же образцах сначала определить величину отскока шарика, а затем испытать эти образцы в прессе.
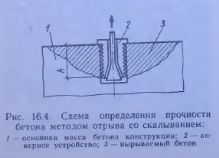
При определении прочности бетона методом пластических деформаций (ГОСТ 22690.1—77) также используется металлический шарик. Метод основан на статистической связи между прочностью бетона и диаметром или глубиной отпечатка (лунки), возникающего при пластической деформации бетона в процессе вдавливания шарика. Приборы для таких испытаний делят на две группы. В приборах статического действия нагрузка на штамп или боек передается постепенно, с возрастающим усилием (прибор конструкции Г. К. Хайдукова и др.). В приборах динамического действия нагрузка передается в виде удара — это молотки систем К. П. Кашкарова (ГОСТ 22690.2—77) и др. При определении прочности бетона методом пластических деформаций необходимо строить тарировочные кривые.
Промышленность непрерывно разрабатывает и внедряет новые, более совершенные приборы и установки контроля готовых изделий и технических процессов на заводах сборного железобетона. Например, созданы микропроцессорные комплексы ВСМ-4 и ВРМ-4. Комплекс ВСМ-4 предназначен для неразрушающего определения прочности и однородности бетона. Он состоит из портативного склерометра и аналого-цифрового преобразователя с микропроцессорным устройством, предназначенного для измерения и регистрации сигналов от ударника склерометра, снабженного магнитоупругим преобразователем. В комплекс ВРМ-4 входят и датчики напряжений бетона и аналого-цифровой преобразователь (АЦП) с микропроцессорной системой; датчики, заложенные в бетон, подсоединяются к АЦП. ВРМ-4 коммутирует, регистрирует и записывает в память комплекса сигналы от датчиков, а также выполняет необходимые расчеты для определения напряженного состояния и усилий по сечениям конструкций.
В настоящее время комплексы применяют для контроля действительного состояния и качества многих железобетонных сооружений, например при определении распределения прочности бетона в железобетонных колоннах и ригелях, при определении напряжений обжатия в сечениях преднапряженных ригелей, при контроле усилий в железобетонных колоннах во время монтажа каркаса зданий и т. п.