
Примеры практического учета технологических факторов при проектировании и изготовлении сборных элементов
Способ снижения расчетных первых потерь напряжения в арматуре прн стендовой технологии изготовления предварительно напряженных конструкций. Недостатком традиционного способа изготовления предварительно напряженных железобетонных изделий являются потери напряжения в арматуре от температурного перепада, которые снижают трещиностойкость изделия, требуют повышенного расхода высокопрочной стальной арматуры и удлинения цикла термообработки.
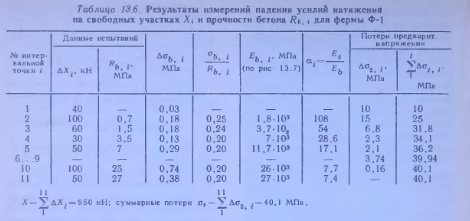
Новый способ значительно экономит арматуру и повышает качество изделий за счет снижения расчетных потерь напряжения в арматуре предварительно напряженных конструкций от перепада температуры (80 МПа), некоторой части потерь напряжения от релаксации арматуры (30 МПа), от деформации упоров (20...30 МПа), которые учитываются при расчете трещиностойкости, раскрытии трещин и деформации (II группа предельных состояний). Метод позволяет снизить расчетные потери примерно на 100 МПа, что соответствует снижению расхода рабочей напрягаемой арматуры на 5 или 8 % (соответственно для стержневой и проволочной арматуры) Кроме того, это позволяет: избегать дополнительного перерасхода арматуры, доходящего до 30 % при изготовлении конструкций на открытых полигонах при температуре воздуха ниже + 15° С (до —25° С); сокращать удлиненные циклы термообработки до продолжительности цикла в закрытом помещении, а также повышать качество изготовляемых изделий. Расчетные потери напряжения могут быть снижены при изготовлении предварительно напряженных конструкций по стендовой технологии (преимущественно на коротких стендах) для изделий любой длины, для любого класса бетона и класса арматуры.
Способ снижения расчетных потерь напряжения в некоторых случаях дает возможность: а) компенсировать пониженный по сравнению с проектным значением уроьень контролируемого предварительного напряжения в арматуре; б) переводить конструкции в другой класс нагрузок; в) переводить конструкцию в другую категорию трещиностойкости, в том числе при несоблюдении требований ГОСТ 8829—77 по трещиностойкости, ширине раскрытия трещин деформативности.
Способ основан на снижении указанных потерь напряжений путем соответствующей подтяжки напрягаемой арматуры с помощью домкрата в период от начала подъема температуры (пуска пара в ямную камеру или паровую рубашку) до стабилизации температуры изотермической выдержки (2...4 ч). Напряжение в арматуре поддерживают постоянным за счет перемещения натяжного устройства соответственно показаниям контрольного приспособления, без передачи усилия обжатия на бетон (при росте его прочности от нуля до передаточной прочности).
Практически технология способа состоит в следующем. Вначале натягивают арматуру и формуют изделие. Затем на арматуру каждого свободного участка наносят торцовую риску или устанавливают на ней у торца изделия индикатор, после чего одновременно с подъемом температуры непрерывно подтягивают арматуру (вплоть до начала охлаждения) с двух противоположных сторон изделия, а величину напряжения в арматуре каждого свободного участка поддерживают постоянной перемещением натяжного устройства при неизменном показании контрольного манометра. При этом арматура и бетон в торцовой части изделия не должны смещаться относительно друг друга. Контроль этого условия проводят по несмещаемости торцовой риски относительно торца бетона или по показаниям индикатора 3 (рис 13.15).
Подтяжка арматуры осуществляется таким образом, чтобы уровень предварительного напряжения по манометру домкрата был постоянным с начала подъема температуры и до окончания ее подъема. В период внедрения технологии (период наладки) рекомендуется контроль стабильного (постоянного) уровня предварительного напряжения осуществлять как по манометру домкрата, так и с помощью индикатора часового типа с ценой деления 0,01 мм, установленного на арматуре в обеих торцовых зонах изделия, согласно рис. 13.15. В случае стабилизации уровня предварительного напряжения по показаниям манометра и индикатора в течение 15...30 мин подтяжка арматуры домкратом может быть закончена. Период подтяжки арматуры домкратом должен уточняться при каждом изменении скорости подъема температуры и уровня изотермического прогрева, а также класса бетона и изделия. В период отработки технологии изготовления и подтяжки рекомендуется установить закон фактического роста прочности бетона в период подъема температуры.
При внедрении методики снижения расчетных первых потерь напряжения в арматуре при изготовлении предварительно напряженных конструкций рекомендуется разработать следующий план мероприятий.
1. Выявить на действующих заводах ЖБИ рассматриваемого региона наличие стендов (коротких, длинных), на которых изготовляют преднапряженные конструкции. При этом установить: а) место расположения стенда (стендов) - на открытом полигоне, в закрытом полигоне, в закрытом помещении (цехе), б) длину стенда (от упора до упора); в) способ натяжения (домкратом всей арматуры одновременно, неодновременно); вид арматуры (стержневая, канатная, проволочная); д) виды изготовляемых на стендах однотипных изделий (под разные классы нагрузки), отличия в армировании — количество рабочей арматуры) е) соответствие (или характер несоответствия) результатов испытаний конструкций требованиям ГОСТ 8829—77 и контрольных нагрузок, приведенных в рабочих чертежах.
2. Из числа выявленных стендов и изготовляемых на них предварительно напряженных конструкций для внедрения предлагаемого способа снижения расчетных потерь напряжений особо выделить те, в которых натяжение всей арматуры осуществляется домкратами одновременно. При этом могут применяться и другие технологии изготовления при условии обследований, выполняемых с участием сотрудников НИИ.
3. Выполнить пересчет конструкций для выявления возможного уменьшения количества рабочей арматуры при условии согласования с проектной организацией — автором проекта и при условии испытания конструкций с новым армированием, изготовленных с применением способа подтяжки.
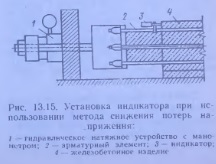
4. При широком внедрении способа выполнить пересчет конструкций с использованием имеющихся в проектных организациях программ для расчета предварительно напряженных конструкций на ЭВМ.
Пример 13.3. Производится изготовление сборной предварительно напряженной железобетонной фермы длиной 24 м из бетона класса В35 на стенде с расстоянием между упорами 28 м и расположением арматурных канатов вдоль нижнего пояса. Принято групповое натяжение арматурных канатов натяжными устройствами на неподвижные упоры стенда с контролем по манометру до уровня 200° по шкале. После установки напрягаемой арматуры формуют изделие в течение 2 ч. Перед термообработкой с каждой стороны изделия готовят к работе (см. рис. 13.15): контрольный манометр на гидравлическом натяжном устройстве и электромеханический индикатор 3 на арматуре свободного участка 2 около бетонного торца изделия 4. Принимают уровень напряжения в арматуре свободного участка, равный 190° по шкале контрольного манометра, за постоянный уровень на время последующей термообработки. Проводят термообработку изделий в камере и подтягивают арматуру одновременно, начиная с момента подъема температуры от 15 до 70° С (в течение 3 ч), и далее при изотермическом прогреве (в течение 6 ч), вплоть до начала охлаждения и при достижении передаточной прочности по испытаниям кубов в горячем состоянии, равной 70% проектной прочности бетона.
Арматуру изделия подтягивают перемещением гидравлического натяжения устройства так, чтобы показания контрольного манометра (см. рис 13.15) оставались неизменными, а смещение арматуры относительно бетона по показаниям контрольного индикатора 3 равнялось нулю. Изготовленная ферма при испытаниях по действующему ГОСТ 8829—77 должна с запасом превосходить требования проекта по трещиностойкости и жесткости, являющиеся основными показателями качества. В результате может быть также выявлена возможность экономии арматуры.
Способ снижения предварительного напряжения в арматуре в период охлаждения после тепловой обработки. Способ может быть использован при стендовом производстве предварительно напряженных железобетонных конструкций в закрытых помещениях и на открытых полигонах, при положительной и отрицательной температурах внешней среды. Недостатком известных способов изготовления предварительно напряженных железобетонных изделий, включающих натяжение арматуры, формование, термообработку, охлаждение и отпуск натяжения арматуры, являются: трещинообразование в бетоне изделий, обрывы арматуры и ухудшение анкеровки из-за возрастания растягивающих усилий на свободных участках арматуры при охлаждении изделий на стенде после термообработки.
Новый способ повышает качество изготовляемых изделий. Это достигается тем, что, используя обычный метод изготовления предварительно напряженных железобетонных изделий (включающий натяжение арматуры, формование, термообработку, охлаждение и отпуск натяжения арматуры), отпуск натянутой арматуры осуществляют с момента начала охлаждения изделия одновременно с противоположных его сторон, причем напряжение в арматуре на свободных участках поддерживают постоянным.
Технология способа состоит в следующем. Выполняют натяжение арматуры, формование и термообработку. Перед охлаждением изделий на арматуре каждого свободного участка у торца изделия устанавливают индикатор с ценой деления 0,01 мм (см. рис, 13 15). После этого с момента начала охлаждения изделия осуществляют отпуск натяжения всей арматуры, причем напряжение в арматуре поддерживают постоянным по показаниям контрольного приспособления — динамометра или манометра. При этом арматура и бетон в торцовой части изделия не должны взаимно смещаться. Контроль этого условия проводят по показаниям контрольного индикатора. После достижения в заданный момент передаточной прочности бетона изделия и окончания подготовительных работ напряжение в арматуре каждого свободного участка снижают до нуля. Возможен вариант изготовления с осуществлением раннего начала охлаждения после прекращения подвода теплоты к изделию.
Пример 13.4. Изготовить предварительно напряженную двускатную балку длиной 18 м из бетона класса В45 на стенде с расстоянием между упорами 22 м и с расположением арматурных канатов вдоль иижнего пояса. Натяжение арматурных канатов производится с закреплением их на неподвижных упорах. После установки не напрягаемой арматуры, формования изделия (в течение 1,5 ч) проводят термообработку с равномерным подъемом температуры от 20 до 75 С (в течение 5 ч) и изотермическим прогревом (в течение 8 ч). Перед началом охлаждения изделия на каждом свободном участке арматуры у торца изделия устанавливают контрольный индикатор для регистрации совместных перемещений арматуры и бетона. При этом отмечают уровень напряжения в арматуре по показателям на контрольном измерительном приспособлении. Этот уровень принимают за постоянный на время всего охлаждения изделия.
Изделие охлаждают в камере на протяжении 3 ч при одновременном отпуске натяжения арматуры, при заданном показании контрольного манометра и соответственно постоянном напряжении в арматуре свободного участка. После достижения передаточной прочности бетона, равной 70% от проектной прочности бетона, и окончания подготовительных работ (распалубки, установки домкратов) напряжения в арматуре каждого свободного участка снижают до нуля с передачей усилия обжатия на охлаждаемый бетон.
Для повышения качества изготовляемых изделий отпуск натянутой арматуры осуществляют в момент начала охлаждения изделия одновременно (иногда с противоположных его сторон). Напряжение в арматуре при этом поддерживают постоянным. В результате повышаются трещиностойкость, жесткость и прочность. Поэтому изготовленная балка при испытаниях по ГОСТ 8829—77 должна отвечать всем требованиям проекта по трещиностойкости. жесткости и прочности.
Контрольные вопросы. 1. Как обеспечивают проектное положение арматуры в изделии? 2. Как точность н равномерность натяжения арматуры влияют на качество изделий? 3 Как условия и качество формования влияют на сцепление арматуры с бетоном? 4. Каково влияние особенностей тепловой обработки на качество изделий? 5. Как можно снизить технологическое трещинообразование в изделиях? 6. Как следует передавать с арматуры на бетон усилия предварительного обжатия? 7. Каковы особенности работы сборных элементов при распалубке, съеме с формы, кантовании и транспортировании? 8. Как влияют на качество изделий условия доэксплуатационной выдержки? 9. Приведите примеры практического учета технологических факторов при проектировании и заводском изготовлении железобетонных элементов.