
КАРБОНАТНОЕ СЫРЬЕ
Основными носителями оксида кальция в портландцементных сырьевых смесях являются породы, содержащие карбонат кальция. В составе сырьевой смеси для производства портландцементного клинкера доля карбонатного компонента достигает 70—75 %, поэтому цементные заводы, как правило, размещаются вблизи месторождений карбонатных пород. Определяющее значение карбонатного сырья при выборе сырьевой базы цементного завода заключается еще и в том, что эти породы размещены не повсеместно: например на Украине неглубокое их залегание, удобное для разработки, приурочено, фактически, к структурно-геологическим районам из имеющихся в пределах республики.
Глинистое сырье распространено гораздо шире, поэтому месторождения глин обычно обнаруживаются поблизости от месторождений карбонатного сырья, иногда даже во вскрышных породах карьеров карбонатных пород.
Карбонатные породы ь основном осадочного происхождения. Большинство карбонатов образовалось при одном из трех процессов складконакопления: 1) кристаллизация карбоната кальция за счет органогенного и неорганогенного осаждения или их сочетаний; 2) образование в результате химического и (или) механического разрушения ранее существовавших пород, переноса продуктов либо в виде обломочных частиц, либо в химическом растворе и их отложения; 3) цементация осадков карбоната кальция в условиях низких температур и давлений (условия образования и связанные с этим особенности строения и свойств подробно описаны в указанном обзоре). Несмотря на возможность наличия весьма разнообразных карбонатных примесей (MgCO3, MnCO3, FeCO3, SrCO3, ВаСО2, PbCO3), в естественных условиях обычными карбонатными минералами являются кальцит, арагонит и доломит. Возможен процесс метаморфизации исходных известняков за счет повышения температуры и давления на большой глубине или поблизости к местам вулканической или магматической деятельности; при этом карбонаты приобретают новые структурные, минералогические и текстурные характеристики. В результате перекристализации зерна укрупняются (до 10 мм и выше), структура становится сцепленной мозаичной, реже сланцеватой. В метаморфизованных известняках кальциту сопутствуют кварц, полевые шпаты, флогопит, мусковит, диопсид, скаполит, гроссуляр, тремолит, тальк, актинолит, пирит, апатит, доломит, хондродит и графит. Поскольку грубозернистые известково-силикатные смеси образуются в условиях высоких температур, они менее реакционноспособны по сравнению с тонкозернистыми глинистыми и кремнистыми примесими в осадочных породах. Изменение структуры карбонатов приводит к повышению термической устойчивости кристаллической решетки, увеличению пылеуноса. Кристалличность и грубозернистость таких пород требуют значительных затрат на измельчение, к ним труднее подобрать соответствующий алю- мосиликатный компонент, так как они уже обогащены кремнистым веществом. Кристаллические метаморфизованные известняки имеются в нескольких районах земного шара (Канада, Индия, Сибирь, Австралия, Южная Африка).
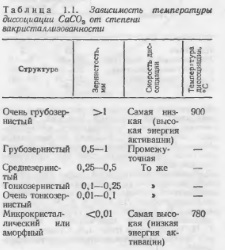
Очень редко встречаются карбонаты среди вулканических пород (переотложения из магм аномального состава), эти месторождения не имеют промышленного значения (за исключением Уганды). Магматические известняки содержат 1,95—2,7 % фосфатов в пересчете на Р2O5, щелочи и хлориды, что несколько затрудняет процесс их переработки в цементном производстве. Гранулометрический состав и степень закристал- лизованности карбонатных пород являются одними из важных свойств, регулирующих термические характеристики (табл. 1.1). Существуют и другие, менее употребительные классификации карбонатов, учитывающие размеры частиц (Рукин Л. Б., Пустовалов Л. В.).
С точки зрения пригодности для производства портландцемента важной характеристикой является химический состав, поэтому есть несколько классификаций известняков: как полигениык пород, учитывающих переходность состава; на основании соотношения кальция и магния: содержания глинистых и т. д. Известняк с глинистым цементирующим материалом легче измельчается и имеет более высокую реакционную способность, чем известняк с кремнистым цементирующим веществом.
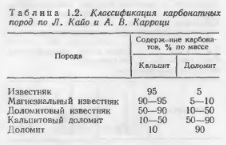
Однако большое влияние на пригодность породы оказывает вид глинистых примесей, поэтому весьма наглядной представляется классификация, разработанная С. Р. Гошем для известняков Индии. Эта классификация совпадает с характеристикой применимости глин для цементного производства.
Для технологических целей удобна классификация, основанная на минералогическом составе карбонатной породы. Упрощенная классификация разработана Л. Кайо и А. В. Каррошци (табл. 1.2), а более точная, учитывающая содержание глин и карбонатов в породе,— Г. И. Теодоровичем (табл. 1,3). Существует еще ряд других, меиее распространенных классификаций.
Практически все разновидности природных карбонатных материалов могут использоваться при производстве портландцементного клинкера, хотя в зависимости от условий образования, состава и структуры реакционная способность их различна: наиболее реакционноспособны однородные аморфные (скрытокристаллические) породы — мел и мелкокристаллические известняки; наименее — крупнокристаллический плотный мрамор (этот вид сырья не применяется). Промежуточное положение занимают различные виды известняков.
Природные карбонатные породы меньше, чем другие виды сырьевых компонентов, могу заменяться техногенными продуктами. Однако расход природного карбонатного сырья может быть в определенной мере снижен при комплексной (безотходной) разработке месторождений природного сырья: материалом для замены основного вида карбонатного компонента могут быть породы вскрыши по другим видам рудных и нерудных полезных ископаемых. Эффективность использования вскрышных или сопутствующих карбонатных пород определяется мощностью пласта или прослойки и степенью загрязненности примесными компонентами. Могут использоваться также отходы буто-щебеночного производства, пильных камней, хвосты обогащения некоторых производств, например серных руд и т. д.
В качестве материала, содержащего оксид кальция, связанный в силикаты, могут применяться гранулированный доменный шлак, нефелиновый шлам и электротермофосфорные шлаки (ЭТФ- шлаки) Гранулированиый доменный шлац и нефелиновый шлак (отходы производства глинозема из нефелинов и сиенитов) содержат двухкальциевый силикат; ЭТФ-шлак (отходы производства фосфорной кислоты) — моиосиликат кальция (волластонит). Однако гранулированный доменный шлак как компонент сырьевой смеси практически не используется, так как гораздо рентабельнее применять его как компонент смешанных цементов. Нефелиновый шлам и ЭТФ-шлак как цементное сырье представляют интерес лишь для отдельных регионов.
Свойства карбонатных пород как компонентов портландцементной сырьевой смеси определяются не только свойствами самой породы, но и совместимостью (сочетаемостью) физических, минералогических и термических характеристик с соответствующими свойствами алюмосиликатного и других компонентов. От этого зависит эффективность осуществления основных технологических переделов(измельчение, гомогенизация, диссоциация, клинкерообразование). Хорошо известно, что комбинация плотного кристаллического или тонкозернистого плотного кремнистого известняка с мягкой каолинитовой глиной дает неоднородную сырьевую муку с более крупными зернами карбоната кальция; комбинация мягкого мела и кристаллических сланцев дает сырьевую муку с более крупными силикатными зернами. С точки зрения эффективности (скорости) диссоциации и реакционной способности установлено, что кристаллический известняк реагирует вяло даже с аморфным кремнеземом в виде золы или шлака, а более реакционноспособный арагонит медленно реагирует с самородным кремнеземом в виде песчаника или кристаллических сланцев. Кремнезем в виде кремия, а- или Р-кварца более стоек к измельчению и менее реакционноспособен, чем связанный кремнезем (глины, полевые шпаты и т. д.). Сырьевые смеси практически одинакового химического, ио различного минералогического состава проявляют различные свойства при обжиге: реакционная способность смеси сильно падает при наличии кристаллического кварца, а при значительном его содержании клинкер может быть испорчен (рис. 1.2 (61). Повышение содержания в известняке кремнезема в виде Р-кварца иа 1,5 % понижает содержание C2S в клинкере более чем на 20 %.
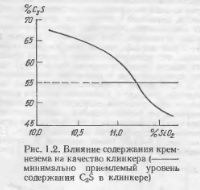
Реакционная способность карбоната как компонента портландцементной сырьевой смеси определяется многими факторами — кристаллической структурой, минералогическим составом, дисперсностью, наличием примесей и т. д.
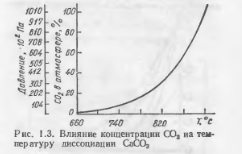
в табл. 1.4 [5, 6] (указанная температура диссоциации чистого кальцита — 898 °С по данным Ю. М. Бутта может колебаться в пределах от 812 до 928 °С в зависимости от размера зерен СаСO3, растворимости СаО в СаС03, дефектности решетки и т. д., что хорошо согласуется с данными табл. 1.2).
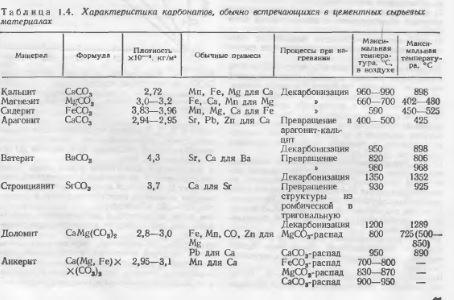
В реакции декарбонизации существует определенная связь между давлением, концентрацией СO2 и температурой (рис. 1.3). Например, Дж. Томпсоном показано, что при массовом отношении СаО : СаС03 =1:1 при нормальном давлении 100 %-го СO2 и температуре 898 °С система находится в состоянии равновесия; при снижении температуры до 890 °С реакция идет в сторону образования кальцита, при повышении до 910 С — образования оксида кальция. Реакция декарбонизации является (А. Хедвалл) процессом диффузии в твердом состоянии, при которой разложение СаС03 начинается с образования псевдоморфиых двумерных кристаллов СаО (2—3 %) по кристаллам CaCO3; лишь спустя некоторое время, известное как индукционный период, появляются трехмерные ядра кристаллов СаО. Чем крупнее исходные кристаллы и совершеннее их структура, тем продолжительнее индукционный период. Далее, по И. В. Кравченко, существует две стадии процесса разложения карбонатов:
1) кинетическая, скорость которой определяется энергией формирования и концентрацией ядер СаО;
2) диффузионная — скорость зависит от толщины проницаемых оболочек частиц и от скорости диффузии СO2.
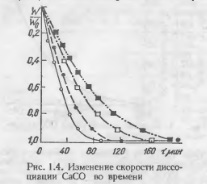
Диффузия в твердой фазе СO2 через СаО в зоне поверхности раздела реакций является стадией контроля скорости процесса декарбонизации. Так как реакция проходит от внешней части кусков известняка к внутренней, длина диффузионного пути прохождения газа через поры со временем увеличивается. Это вызывает рост обратного давления в процессе диффузии твердого состояния, и скорость реакции со временем снижается (рис. 1.4).
О. П. Мчедловым-Петросином было показано, что энергия активации при диссоциации известняка оказывает значительное влияние иа энергию активации образования минералов клинкера; это согласуется с данными А. К. Чатгерджи о том, что скорость формирования C2S снижается с ростом энергии активации при диссоциации карбонатов.
Температура диссоциации карбонатов и скорость процесса декарбонизации подвержены значительным колебаниям под влиинием следующих факторов.
Наличие связанных минералов и примесей. Влияние связанных минералов и примесей в основном сводится к понижению температуры разложении, поскольку парциальная упругость кальцита при диссоциации увеличивается, по Ф. У. Лохеру, такими оксидами как SiO2, Аl2О3, Fe2O3. Температура диссоциации карбонатов понижается (см. табл. 1.4) в последовательности кальцит - доломит - анкерит; т. е., если анкерит присутствует в известняке, он должен зыделять известь при относительно более низкой температуре, и, если не происходит ассимиляции этой извести, связанной с отсутствием других активных компонентов, кристаллы извести начинают терять активность. Эти кристаллы извести в 1,5— 2 раза меньше, чем те, которые были образованы, что ускоряет реакцию. Наличие арагонита вместо кальцита снижает температуру начала взаимодействия с глинистым компонентом иа 50 °С и более, а степень мергелизации известняков приводит к изменению качества клинкера за счет различия скорости формирования минералов иа заключительных этапах обжига. Структура, дисперсность и температура обжига. Влияние этого параметра показано в табл. 1.1 и на рис. 1.5—1.7. Имеет значение и степень измельчения карбонатной породы: по И. В. Кравченко и М. Т. Власовой крупнозернистые сырьевые смеси характеризуются двухступенчатой декарбонизацией (получено при помощи ДТА). Установлено, что:
у большинства известняков может иметь место двухступенчатое разложение с различными значениями Еа для первой и второй ступени, уровень энергии активации известняков лежит в пределах 120—250 кДж/моль;
чем выше зернистость и загрязненность известняка, тем ниже энергия активации при диссоциации;
существует, по-видимому, определенная связь между энергией активации, максимальной температурой и скоростью разложения (рис. 1.6). Зависимость степени декарбонизации известняка от дисперсности частиц и температуры свидетельствует о различном влиянии температуры на разные фракции материала: для частиц размером меиее 0,063 мм даже при темпе ратурах 1400—1500 °С достигаются высокие значения е (0,7—0,8), при 1650 °С — декарбонизация проходит на 98 %: для фракции 0,100— 0,160 мм наблюдается существенный рост степени декарбонизации в температурном интервале 1550—1650 °С и ее значение достигает 0,92, процесс разложения частиц данной фракции контролируется как кинетическими факторами, так и скоросгью подвода тепла. Для более крупных частиц размерами 0,200—0,315 мм при заданной продолжительности обжига значение е с ростом температуры практически не меняется, вероятно, процесс лимитируется только подводом теплоты к юне эндотермической реакции, протекающей фронтально от поверхности частицы к ее центру. Термообработка приводит к изменению дисперсности материала: обжиг фракции 0,2— 0,315 мм при 1650—1700 °С обеспечивает получение до 40 % частиц размерами менее 0,2 мм, при этом изменяется параметр кристаллической решетки оксида кальция (d = 0,283 против 0,282 нм v оксида кальция, полученного при медленном обжиге) и наблюдается увеличение дефектности кристаллов СаО. Это может быть связано с мгновенной диссоциацией карбонатов при термоударе, во время которой кристаллическая решетка возникающего оксида кальция не успевает образовать стабильную кубическую структуру в отличие от СаО, полученного путем длительного обжига.
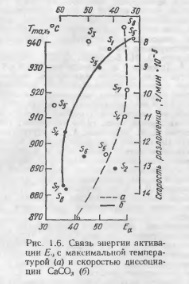
Поскольку в производственных условиях нельзя осуществить помол известняка до получения частиц ыонодисперсного состава, авторами [8] проводилось определение оптимальной степени измельчения при использовании симплекс-решетчатого планирования (трехфакторный план Шеффе) для трех групп частиц (0—0,063; 0,063—0.160 и 0,160—0,315 мм). Получено уравнение зависимости степени декарбонизации известняка от его гранулометрического состава:
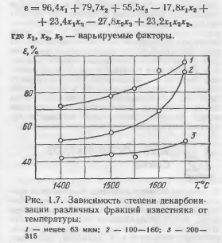
Для проведения линий задаваемого уровня функции отклика на диаграмме «состав — свойство» были рассчитаны значения степени декарбонизации известняка различного гранулометрического состава по сетке переменных в 66 точках с интервалом 5 % (полученные изолинии, вписанные в диаграмму гранулометрических составов известняка, представлены иа рис. 1.8). Выполненные исследования позволили авторам установить, что в процессе интенсивного обжига при температурах, приближенных к температуре топливного факела вращающейся печи, происходит практически мгновенная термическая диссоциация карбонатов, сопровождающаяся самоизмельчением декарбонизирующих частиц под действием термического удара. Возникающий при этом оксид кальция обладает мелкокристаллической дефектной структурой и отличается повышенной активностью по сравнению с оксидом кальция, полученным при медленном обжиге известняка до температуры 1100 °С, что соответствует температуре материала на выходе из зоны кальцинирования вращающейся печи. Это дает реальный технологический эффект: при подаче известняка с горячего конца печи оптимальной степенью его измельчения является тонкость помола, характеризующаяся 30 %-м остатком на сите №008 и позволяющей при незначительном снижении степени декарбонизации и получении оксида кальция максимальной активности существенно уменьшить затраты на помол.
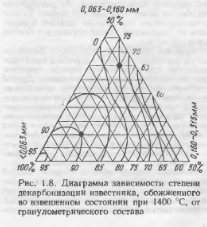