
РАЗНОВИДНОСТИ ПОМОЛЬНЫХ АГРЕГАТОВ, ПРИМЕНЯЕМЫХ ПРИ ПОМОЛЕ ЦЕМЕНТА
Портландцемент получают при помоле смеси, состоящей из цементного клинкера, инертных (до 10 %) или гидравлических (до 15 %) добавок и регулятора схватывания — двуводного гипса (3—5 %) Эффективность процесса помола, а следовательно, и производительность помольных агрегатов зависит от исходной крупности частиц измельчаемого материала, его физико-механических свойств. При уменьшении исходных размеров частиц цементного клинкера до 8—10 мм производительность помольного агрегата можно повышать на 10—15 %, а при питании мельницы материалом с размерами частиц до 2—3 мм — на 25—30 %. При питании мельницы недробленым клинкером ее производительность резко снижается, возрастает удельный расход электроэнергии. Поэтому перед тонким измельчением клинкер необходимо дробить, применяя короткоконусные, ударно-отражательные или инерционные дробилки конструкции Механобра, позволяющие получать частицы размерами не более 5 мм.
Цементный клинкер измельчают преимущественно в трубных мельницах сухого помола, работающих в открытом или замкнутом цикле. При двухстадийном измельчении дробление клинкера заменяется предварительным помолом в высокопроизводительных барабанных мельницах большого диаметра, обеспечивающих производительность до 120 т/ч. Материал на выходе нз такой мельницы содержит до 50—70 % остатка на сите № 008. Предварительный помол клникера можно производить и в стержневых мельницах, выдающих крупку с размерами частиц до 1—2 мм.
В. С. Севостьяновым и др. изучено влияние физико-механических характеристик клинкеров (гранулометрического состава, насыпной массы и др.) и технологических режимов измельчения (толщина слоя, скорость вращения валков и т. д.) на процесс предварительного измельчения клинкера в валковом прессе. Установлено, что с увеличением угловой скорости вращения валков от 0,05 до 1,0 м/с увеличивается выход фракции менее 80 мкм на 15—20 %, а потребляемая мощность привода возрастает с 1,5 до 8 кВт. Повышение давления прессования от 10 до 110 МПа обеспечивает выход фракций менее 80 мкм на 8—12 %.
Дальнейшее тонкое измельчение материала, полученного в результате предварительного помола, повышает производительность шаровой мельницы на 17—20 при одновременном снижении удельного расхода электроэнергии на 10—15 %. На второй стадии помола применяют трубные мельницы, загружаемые шарами малого диаметра (25—30 мм) и цильпебсом размерами 3—8 м. Производительность этих мельниц значительно возрастает при питании их мелкой крупкой. Двухстадийный помол применяют при производстве смешанных цементов, а также при тонком его измельчении.
В последние годы совершенствование процесса помола развивается в основном в направлении увеличения размеров мельниц и мощности их привода. Однако и мельницы большого диаметра для максимального снижения расхода электроэнергии требуют питания материалом малой крупности.
Помол клинкера в открытом цикле характеризуется повышенными энергозатратами ввиду частичного переизмельчения, относительно невысокой тонкостью помола (до 300 м2/кг). В качестве помольных агрегатов применяют многокамерные трубные (многотрубные) мельницы. При производстве рядового цемента с удельной поверхностью до 300 м2/кг применяют открытый цикл ломота.
Применение многотрубных мельниц позволяет уменьшить металлоемкость и стоимость помольных агрегатов, снизить удельный расход электроэнергии на 50—60 %, получить цемент высокого качества. Многотрубные мельницы исключают перегрев цемента, надежны и удобны в эксплуатации.
Помол в замкнутом цикле экономически более эффективен. При его использовании из процесса помола быстро удаляются мелкие фракции, поэтому готовый продукт более однороден по гранулометрическому составу: содержит большое количество средних фракций и относительно малое количество крупной фракции. Такой состав обеспечивает более высокую прочность цементного камня, в связи с чем помол по замкнутому циклу применяется при получении высокопрочных и быстротвердеющих цементов. Помол по замкнутому циклу позволяет сократить удельный расход электроэнергии на 10 % и одновременно на столько же повысить производительность мельниц. Измельчение клинкера по замкнутому циклу осуществляют по разным схемам. При непользовании двух мельниц получают полидисперсный цемент. Материал из мельницы грубого помола через сепаратор подается на домол в мельницу тонкого помола. Готовый продукт получают смешением тонких фракций из сепаратора и мельницы домола. Но эта схема имеет ряд недостатков: громоздка, металлоемка, требует большого количества транспортных средств. Более проста схема, основанная на применении трубной двухкамерной мельницы. Размолотый в данной мельницы материал подается в сепараторы, откуда крупка возвращается на домол в первую камеру мельницы, а готовая фракция поступает в силосы. Недостатком второй схемы является повышенный расход электроэнергии из-за некоторого переизмельчения материала. Применение длинной трубной мельницы позволяет получать полидисперсный зерновой состав вяжушего с повышенной тонкостью помола. Максимально повысить эффективность замкнутого цикла позволяет применение многокамерной трубной мельницы с разгрузкой материала на стыке между 2 и 3 камерами. После разделения в сепараторе крупка поступает на домол в 3 камеру, а готовый продукт получают путем смешивания мелкой фракции из сепаратора и материала, выходящего нз последней камеры мельницы. Недостаток третьей схемы состоит в невозможности перехода на открытый цикл, более высокой сложности в конструктивном исполнении н в эксплуатации. Схема пригодна только для специальных мельниц малых и средних размеров.
Применение на Новоспасском цементном заводе замкнутого цикла с сепаратором для мельницы размерами 4 X 13,5 м позволило повысить производительность помольного агрегата на 20 % при той же тонкости помола.
Ассортимент мелющих тел и степень заполнения ими объема мельницы существенным образом влияют на производительность помольного агрегата и тонкость помола готового продукта. Размеры мелющих тел определяются крупностью частиц цементного клинкера и добавок, а также их физико-химическими и физико-механическими свойствами. Чем крупнее исходные частицы измельчаемого материала, тем большими должны быть размеры шаров в первой камере. Применение крупных шаров не позволяет получать цемент с высокой тонкостью помола. Для получения высокомарочных тонкомолотых цементов наибольший эффект дает загрузка мелющих тел одинакового размера. При этом в первую камеру загружают наиболее крупные шары, в дальнейшем по ходу движения материала средний размер шаровой нaгрузки должен уменьшаться, а последнюю камеру загружают цильпебсом малых размеров.
Трубные мельницы делят на камеры специальными перегородками, позволяющими изменять ассортимент мелющих тел по длине мельницы. Для оптимизации процесса помола необходимо распределять мелющие тела по длине мельницы таким образом, чтобы крупные шары сосредоточивались в начале, а более мелкие — в конце камеры. Такое распределение можно обеспечить специальной бронефутеровкой. Сортирующие броиеплиты представляют собой конические кольца, образующие уклон 5—10° в сторону загрузочного конца. Применение бронеплит позволяет отказаться от установки части перегородок и повысить производительность мельницы на 5—7 %.
Существующие шаровые мельницы с постоянной скоростью вращения имеют тот принципиальный недостаток, что в результате нстнрання мелющих тел и бронефутеровки высота подъема шара все время уменьшается. Только регулирование скорости вращения мельницы позволяет получать оптимальную высоту подъема шаров. В связи с этим в зарубежной практике в последнее время получили широкое распространение мельницы с безредукторным дугостаторным электроприводом мощностью 6000 кВт и выше с регулируемой скоростью врашеиня. Например, норвежской фирмой «Суварангер АС» в 1982 г. введена в эксплуатацию огромная трубная мельница с безредукторным дугостатическим регулируемым электроприводом мощностью 35 тыс. кВт. Скорость вращения мельницы можно регулировать. Первая шаровая мельница с регулируемым электроприводом размерами 2 X 10,5 м мощностью 680 кВт введена в СССР на Белгородском цементном заводе. Оптимизация скорости вращения мельницы позволила повысить производительность на 25 % и снизить удельный расход электроэнергии на 26 % прн неизменной тонкости помола вяжущего. В 1982 г. на заводе «Гигант» ПО «Воскресенскцемент» впервые в СССР введена в эксплуатацию мельница размерами 4 X 13,5 м с отечественным регулируемым безредукторным электроприводом мощностью 3200 кВт. Эксплуатация этих мельниц показала, что регулировка скорости врашения мельницы позволяет существенно повысить ее производительность — более чем на 50 %, а также поддерживать оптимальный режим работы мельницы в интервале между очередными догрузками мелющими телами.
Наклонные междукамерные перегородки в мельницах замкнутого цикла измельчения используют для повышения производительности мельниц, снижения удельного расхода электроэнергии, а также для стабилизации зернового состава: установка перегородки с углом наклона 55° на цементной мельнице размерами 3,2 X 15 м (ПО «Ахангаранцемент») дала увеличение производительности на 12 %, удельный расход электроэнергии снизился на 9 %. При помоле в замкнутом цикле с сепаратором диаметром 3,5 м остаток на сите № 008 для шлакопортландцемента М400 составил 5—6 % при помоле указанной шихты в открытом цикле. Одним из направлений повышения эффективности помола в шаровых мельницах является разработка агрегатов с внутримельннчными энерго обменными устройствами (ВЭУ): наклонными перегородками, диафрагмами, кольцами, специальной футеровкой и т. д. [2]; ВЭУ обеспечивают снижение удельного расхода электроэнергии на 15—20 %, повышение производительности на 20—25 %.
Многолетняя промышленная эксплуатация одного из ВЭУ — наклонной межкамерной перегородки (НМЛ) свидетельствует о том, что ее применение на первой стаднн помола на 15—20 % сокращает удельный расход электроэнергии за счет уменьшения на 20—30 % массы мелющих тел в первой камере мельницы без существенного снижения производительности.
Применение на последней стадии тонкого помола цемента энергообменных устройств в виде лопастных эллипсных сегментов (ЛЭС) позволяет снизить удельный расход электроэнергии на 10—15 % и одновременно повысить производительность мельницы на 15—20 %.
Сочетание НМП и ЛЭС позволит повысить эффективность измельчения на 25 %.
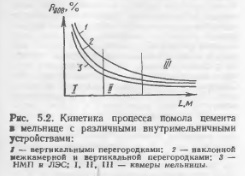
Анализ процесса помола в мельницах с различными ВЭУ (рис. 5.2) свидетельствует о необходимости дальнейшего совершенствования конструкций помольного оборудования. Наклонная межкамерная перегородка разрушает застойные зоны мелющей загрузки, способствует классификации измельчаемого материала, улучшает аспирацнонный режим мельницы. Несмотря на уменьшение массы мелющей загрузки на 20— 30 %, наклонная межкамерная перегородка обеспечивает интенсивное измельчение в I и II камерах. Применение ЛЭС в III цильпебсной камере обеспечивает интенсификацию истирающего действия мелющей загрузки на измельчаемый материал и своевременное удаление тонкомолотых частиц вяжущего из зоны помола. Опыт эксплуатации цементных мельннц размерами 4 X 13,5 м на Карачаево-Черкесском цементном заводе показал, что правильный выбор ВЭУ (с учетом размера мельницы и физико-механических характеристик измельчаемого клинкера) позволяет не только снизить энергетические затраты, но и повысить производительность мельниц на 15—20 %.
Поскольку использование НМП в цементных мельницах дает большой эффект, постоянно растет интерес к ним со стороны цементных заводов. Проведенные на Карачаево-Черкесском цементном заводе испытания подтвердили их высокую эффективность и целесообразность широкого внедрения в производство.
Как уже отмечалось, коэффициент полезного действия трубных шаровых мельннц очень низок. Поэтому за рубежом с начала 60-х годов получили распространение весьма перспективные помольные агрегаты — валковые мельницы. Принцип действия валковых мельниц аналогичен бегунам: измельчение материала осуществляется путем раздавливания катками. Валковые мельницы имеют существенные преимущества перед традиционными трубными. Онн компактнее, менее металлоемки, не требуют догрузки мелющими телами, легко поддаются автоматизации, имеют повышенный коэффициент использования и пониженные производственные затраты. Недостатком валковых мельниц, сдерживающим их широкое применение, был большой износ валков. Однако в последние годы получены весьма износостойкие материалы (например, нигард-IV, хромомолибденовый чугун) и, начиная с 70-х годов, валковые мельницы почучают широкое распространение при помоле цемента. Их серийное производство налажено фирмамя «Полизиус», «Пфейфер», «Леше».
Валковые мельницы работают в замкнутом цикле с проходными сепараторами, встроенными в верхнюю часть кожуха нли установленными вне корпуса. Применение валковых мельниц при помоле цемента позволяет снизить расход электроэнергии в среднем на 10—25 %. По данным фирмы «Полизиус» валковая мельница производительностью 80 т/ч позволяет снизить удельный расход электроэнергии иа 20 % по сравнению с шаровой мельницей замкнутого цикла той же производительности. По данным фирмы «Пфейфер» применение валковой мельницы типа MSP снижает расход электроэнергии на 25—30 %. Большой интерес для цементной промышленности представляет новый вид технологического оборудования — струйные мельницы, обеспечивающие одновременно с измельчением термохимическую обработку материала. Струйные мельницы очень просты в монтаже, эксплуатации и ремонте, практически бесшумны, не пылят. На Подольском экспериментальном цементном заводе с 1977 г. успешно работает струйная мельница типа МСП-25. Цементный клинкер загружают в бункер, а оттуда системой питателей и транспортеров подают в помольные эжекторы. Туда же по коллектору под давлением 0,4— 0, 6 МПа подают энергоноситель — сжатый воздух, подогретый до 350 °С. Скорость движения измельчаемых частиц возрастает до 100—150 м/с, что способствует их столкновению в помольной камере и измельчению. Готовый материал поступает в пылеразделитель, откуда грубая фракция возвращается на домол, а измельченный продукт осаждается в батарее циклонов. Энергоноситель очищается от мелкой фракции в пылеуловителе и выбрасывается в атмосферу. Готовый продукт получают путем смешивания осажденной в батарее циклонов и уловленной в пылеуловителе фракций. Исследования показали, что активность цемента, полученного в струйной мельнице, выше, чем у цемента из шаровой мельницы. На Западе фирмой «Маджак — Дональдсон» (США — Бельгия) осуществляется серийный выпуск струйных мельниц. Представляет интерес не имеющий аналогов в СССР и за рубежом новый тип помольного оборудования, основными элементами которого являются упруго деформированные рабочие органы из пружинной стали прямоугольного и трапецеидального сечеиия (Л. А. Сиваченко, А.И. Кургузиков). Рабочие органы представляют собой систему элементов криволинейной конфигурации с избирательной жесткостью, связанную с приводом. Измельчаемый материал подвергается в аппарате сложному комбинированному силовому воздействию с высокой частотой единичных нагрузок, подаваемых в зону разрушения дозированными потоками. Предложенный аппарат производительностью до 50 т/ч рекомендуется для тонкого и сверхтонкого измельчения цементного клинкера, карбонатных пород, кварцевого песка, шлаков н других строительных материалов и отходов, а также для домола цемента и других компонентов бетонных смесей. Аппарат, наряду с измельчением, обеспечивает качественное смешивание и гомогенизацию компонентов. Кроме того, аппарат имеет высокую активационную способность обеспечивая повышение прочности образцов из бетонных смесей (путем активации компонентов смеси) в 28-суточном возрасте в 1,3—2 раза, что позволяет сэкономить до 20—25 % цемента при той же рецептуре смеси или до 50—70 % цемента при использовании в качестве активных добавок золы или шлаков.
А. В Лузин и др. показали, что применение пневмонмпульсных измельчителей, работающих по принципу скоростного удара материала об отбойную поверхность при объемной концентрации материала 0,2—0,6, позволяет активировать материалы, переработка которых в традиционных помольных агрегатах затруднена н малоэффективна. Например, активация смеси цемента с наполнителем — кварцевым песком позволяет получать изделия, значительно превышающие по прочности контрольные образцы, изготовленные из неактивированной смеси (до 66 %), илн снизить содержание вяжущего (до 10 %) без снижения прочности и морозостойкости изделий. Одним нз важнейших направлений развития техники помола является разработка и внедрение в производство компактных, малоэнергоемкнх и надежных в работе измельчителей. К их числу относится центробежный измельчитель (разработка А. В. Богородского и др.), который состоит из двух рабочих органов, расположенных на вертикальных валах. Нижннй орган представляет собой диск, состоящий из пластин с концентрическими пазами, в которых установлены рифленые плиты. Верхний рабочий орган, выполненный в виде усеченного конуса с двумя рабочими поверхностями, расположен на трубчатом валу. Одна из рабочих поверхностей содержит элементы в виде винтовых выступов, высота которых уменьшается по мере приближения к нижнему основанию конуса; другая — пластины и концентрические пазы с рифлеными выступами.