
Прочность и деформативностъ арматурных сталей
Прочность и деформативностъ арматурных сталей характеризуются диаграммой os - es при растяжении стали до разрыва (рис. 1.23).
Для многих горячекатанных сталей характерно наличие на диаграмме участка линейной зависимости между напряжениями и деформациями (упругая работа стали) и четко выраженной площадки текучести (рис. 1.23, а), длина которой зависит от структуры стали. Для высокопрочных арматурных сталей (рис 1.23, б, в) четкого предела упругости и предела текучести нет, поэтому пользуются понятиями условного предела упругости и условного предела текучести.
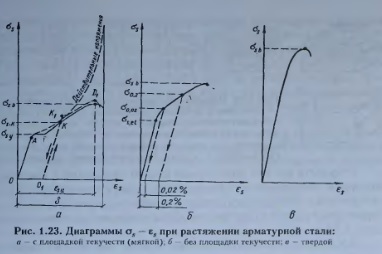
За условный предел упругости принимают напряжения, при которых возникают начальные остаточные относительные деформации, составляющие 0,02% участка образца, равного базе измерения. За физический предел текучести osy принимают наименьшие напряжения, при которых образец впервые получает значительные деформации без заметного увеличения нагрузки, за условный предел текучести — напряжения, при которых остаточные деформации достигают 0,2% длины участка образца, принимаемой в расчет при определении данной характеристики.
Под временным сопротивлением osb подразумеваются напряжения, отвечающие наибольшей нагрузке, предшествующей разрушению образца (т.е. нагрузке, при которой наступает его сужение — образуется шейка). Оно определяется по отношению к площади первоначального сечения, и поэтому является условным. После достижения временного сопротивления нагрузка начинает падать вследствие образования шейки на образце и продолжает снижаться вплоть до разрушения — разрыва. При этом напряжения, приходящиеся на единицу площади сечения шейки (т. е. действительные напряжения — см. рис. 1.23, а), возрастают до самого разрыва. Действительное сопротивление разрыву может значительно (в два раза и более) превосходить временное сопротивление.
В области пропорциональности между напряжениями и относительными удлинениями, которой соответствует прямолинейный участок диаграммы растяжения, пространственная решетка получает однородную, т.е. упругую деформацию, одинаковую во всех точках материала; такая деформация не изменяет его структуры и после снятия нагрузки сама собой исчезает. Но начиная с предела текучести, когда в материале проявляются остаточные деформации, внутренняя структура его делается заметно неоднородной.
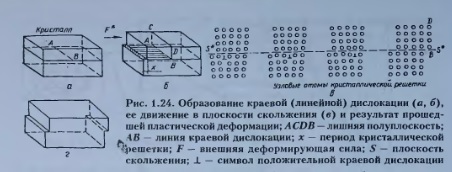
Текучесть мягких арматурных сталей связывают с быстрым движением (“скольжением”) дислокаций — дефектов кристаллов, представляющих собой линии, вдоль и вблизи которых нарушено характерное для кристаллов правильное расположение атомных плоскостей (рис. 1.24, а...в)*.
Поскольку дислокации являются упругими искажениями структуры кристаллов и, следовательно, обладают собственными полями напряжений, они под действием внешних напряжений, приложенных к кристаллу, приходят в движение, проявляющееся во взаимном проскальзывании атомных плоскостей — элементарных актов пластических деформаций (рис. 1.24, в, г).
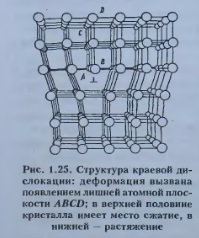
С ростом пластических деформаций число дислокаций растет, их поля напряжений перекрываются и скольжение затрудняется. Это так называемое явление вторичного упрочнения, наступающего после состояния текучести. Чтобы движение дислокаций могло продолжаться, нагрузку необходимо увеличить.
Все сказанное относится и к высокопрочным сталям, с той однако разницей, что здесь текучесть с самого начала проявляется в условиях деформационного упрочнения, одной из основных причин которого являются разного рода структурные неоднородности, препятствующие движению дислокации, такие, например, как границы зерен и скопление легирующих элементов и атомных примесей. В качестве иллюстрации приведена простейшая схема искажения структуры кристалла. В действительности характер дислокационной линии может меняться от краевого (линейного) до винтового и, следовательно, эта линия может извиваться самым причудливым образом. Если учесть ещё, что в 1 см3 холоднодеформированного металла может находиться до 1 млн.км. дислокаций, можно себе представить какие они образуют запутанные клубки и каким сложным образом пересекаются.
Перспективное изображение расположения атомов вокруг краевой дислокации в простом кубическом кристалле показано на рис. 1.25.
Как в мягких, так и в высокопрочных сталях разрушение включает в себя две стадии: появление зародышевых трещин и их распространение (прорастание). В первом случае скорость распространения трещины относительно мала и соизмерима со скоростью деформирования образца, во втором — со скоростью распространения звука в материале образца.
Выявить значения условных пределов упругости и текучести можно нагружением и разгрузкой образца последовательно возрастающими нагрузками с измерением остаточного удлинения образца после каждой разгрузки.
Упругие свойства арматурных сталей характеризуются условным модулем упругости, определяемым как отношение приращения напряжений от 0,15 до 0,4osu (или от 0,1 до 0,35osb) к относительному удлинению образца в том же интервале напряжений. Модуль упругости и здесь, как и применительно к бетону, можно рассматривать как характеристику упругого сопротивления, т. е как характеристику интенсивности нарастания напряжений с увеличением удлинения. А если более конкретно, то применительно к металлу (о бетоне столь определенно, к сожалению, говорить трудно) модуль упругости отражает изменение междуатомных сил сцепления с изменением междуатомных расстояний.
Серьезное значение для правильной оценки напряженно-деформированного состояния железобетонных конструкций на различных стадиях работы, для механизации арматурных работ и удобства натяжения напрягаемой арматуры (при групповом натяжении) имеют пластические свойства арматурных сталей, так как их ухудшение может стать причиной хрупкого (внезапного) разрыва арматуры под нагрузкой, чрезмерных потерь предварительного напряжения, хрупкого излома напрягаемой арматуры в местах резкого перегиба или при закреплении в захватах.
Особое значение приобретают пластические свойства арматурных сталей для конструкций в сейсмических районах, так как высокая пластичность создает благоприятные условия для перераспределения усилий в статически неопределимых конструкциях.
Пластические свойства сталей характеризуются полным относительным удлинением после разрыва и относительным равномерным удлинением.
После разрыва образцов в них сохраняются остаточные удлинения, которые состоят из равномерных удлинений, проявляющихся по всей длине стержня в процессе его нагружения до напряжений, равных osb, и сосредоточенных на участке шейки (длиной 2...4 d) в процессе ее образования вплоть до разрыва. Так вот, полное относительное удлинение — это изменение расчетной длины образца, в пределах которой произошел разрыв (в процентах от первоначальной длины), а относительное равномерное удлинение — изменение расчетной длины указанного образца (в процентах от соответствующей первоначальной длины, принимаемой равной 50 или 100 мм), не включающей место разрыва.
Полное относительное удлинение как характеристика арматурных сталей обладает рядом существенных недостатков. Например, на характер разрушения железобетонных конструкций оказывает влияние не столько полное, сколько равномерное удлинение арматуры, так как образование шейки совпадает с началом падения растягивающих усилий и поэтому происходит уже в процессе разрушения образца. Зависимость б от базы измерения приводит подчас к неправильной оценке действительных пластических свойств арматуры и наконец, поскольку образцы из витой проволочной арматуры теряют при разрушении первоначальную форму, определение полного относительного удлинения для такой арматуры оказывается, практически невозможным.
Так как относительное равномерное удлинение (полное или остаточное) лишено всех этих недостатков, ему и следует отдавать предпочтение при определении пластических свойств арматурных сталей.
Относительные удлинения после разрыва мягких арматурных сталей составляют (в зависимости от химического состава) от 14 до 25%, высокопрочных — от 3 до 8%.
Стальная арматура, как и бетон, обладает свойствами ползучести и релаксации напряжений, хотя их природа в том и другом случае совершенно различна.
Ползучесть и релаксацию напряжений в арматурных сталях связывают (во многих источниках) с процессом диффузионного характера — движением (“переползанием”) дислокаций в поле действия некоторых противодействующих сил (например, тормозящего влияния “облака” растворенных чужих атомов, искажающих решетку) и индивидуальным направленным перемещением точечных дефектов в виде вакансий (незанятых узлов решетки) и атомов внедрения (атомов, расположенных между узлами). Таким образом, здесь также речь идет о пластических деформациях, только протекающих медленно, во времени. В отношении совместной работы арматуры и бетона практический интерес представляет релаксация напряжений, так как именно она вызывает потери напряжений в предварительно напряженной арматуре, непосредственно влияющие на трещинообразование, ширину раскрытия трещин и деформации железобетонных элементов.
Значение релаксации напряжений в арматурных сталях зависит от многих факторов: механических характеристик стали, химического состава и структуры, технологии изготовления конструкций и условий их последующей эксплуатации.
Большое влияние на релаксацию оказывают начальные напряжения: чем они выше, тем сильнее проявляется релаксация напряжений. Особенно интенсивно она протекает в течение первых часов. За это время успевает проя виться около 60% потерь предварительного напряжения, замеренных за 100 ч. В интервале интересующих нас начальных напряжений наблюдается тенденция к затуханию релаксации напряжений, и через 1000 ч. значения связанных с нею потерь возрастают в среднем не более чем на 20...25%.
При повышении температуры сопротивление перемещению атомов в сталях значительно снижается, уменьшается и напряженность поля вокруг дислокационных систем. Следовательно, при тепловлажностной обработке предварительно напряженных конструкций релаксация напряжений должна увеличиваться. Как видно из опытов, при температуре около 100 °С потери от релаксации за 100 ч. увеличиваются в 2...4 раза по сравнению с потерями при 20 °С, а при 200 °С — в 4...6 раз.
При проектировании железобетонных конструкций кроме механических характеристик необходимо учитывать и некоторые другие свойства сталей.
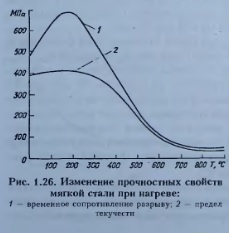
Так, в частности, существенным следует считать вопрос о защите арматуры от высоких температур (рис. 1.26). Поскольку физический предел текучести мягкой стали в железобетонных конструкциях является тем предельным напряжением, при котором начинается стадия разрушения конструкции, то допустимое нагревание арматуры из таких сталей не должен превышать 300...350 °С. То же самое можно сказать и о других арматурных сталях. При нагревании до 300...350 °С их прочностные характеристики практически не снижаются. Однако при нагревании до 400 °С начинается снижение указанных характеристик. При температуре 500 °С падение временного сопротивления для горячекатанных сталей достигает 60...70% первоначального, а для высокопрочной проволоки — 30...40%. В то же время пластические свойства арматуры при нагреве улучшаются и значения относительных удлинений после разрыва возрастают.
Для конструкций, эксплуатируемых при отрицательных температурах, необходимо учитывать склонность арматуры к хладоломкости (т. е. к повышению хрупкости), которая определяется маркой стали, способом ее выплавки и последующей обработки (термическое упрочнение и др.).
Прочностные характеристики арматурных сталей при снижении температуры в интервале до минус 60 °С возрастают, равномерное удлинение увеличивается, сосредоточенные деформации уменьшаются. Важной характеристикой арматурных сталей (при выборе типа соединений) является их свариваемость, которая зависит от химического состава и способа выплавки стали, диаметра стержней, конструкции свариваемого соединения и технологии его выполнения.
Важнейшими факторами, влияющими на механические свойства арматурных сталей, являются химический состав и технология изготовления стальной арматуры.
Предел прочности при разрыве мягких сталей относительно невысок. Повышение прочности стальной арматуры и уменьшение относительного удлинения при разрыве достигают введением в ее состав углерода и легирующих добавок — марганца, кремния, хрома, никеля, циркония и т. д. Так, марганец существенно повышает прочность стали без большого снижения пластичности. Кремний вводят для получения мелкозернистой структуры, но, улучшая прочностные показатели, он ухудшает свариваемость стали, а при повышенном содержании — и стойкость против коррозии. Содержание легирующих добавок обычно ограничивают количеством 0,6... 1,6%.
Дальнейшее повышение прочностных характеристик стержневой арматуры может быть достигнуто упрочнением за счет холодного деформирования (вытяжки) и термической обработки.
Сущность упрочнения стали — наклепа заключается в следующем (рис. 1.23): если в стержне создать растягивающие напряжения, попадающие на диаграмме os - es за площадкой текучести в область упрочнения материала, а затем стержень разгрузить, то диаграмма разгрузки получает вид прямой линии и стержень получает остаточные пластические деформации. При повторном нагружении, поскольку пластические деформации уже выбраны, новая линия диаграммы совпадает с линией разгрузки, оставаясь параллельной участку ОА, характеризующему упругую работу материала. Перегиб линии диаграммы наступит при напряжении.
Явление наклепа (в соответствии с преобладающей сегодня точкои зрения) связано, главным образом, с взаимодействием параллельных дислокаций, движение которых происходит по разным пересекающим друг друга плоскостям скольжения. В результате взаимодействия возникает комбинированная неподвижная дислокация. Возникновение таких барьеров сопровождается скоплением дислокаций (и, следовательно, ростом упругого взаимодействия между ними), препятствующих в месте источника скалыванию (пластическому деформированию).
С течением времени вследствие так называемого старения металла несколько повышается предел текучести (точка Кх), появляется небольшая площадка текучести и несколоко возрастает предел прочности (точка D).
Как видно из диаграммы, одновременно с повышением предела текучести уменьшается и относительное удлинение.
Увеличение прочности стали, связанное с вытяжкой, исчезает от рекристаллизации стали при повышении температуры примерно до 400 °С. Это следует иметь в виду при сварке или нагреве арматуры из упрочненной холодной обработкой стали.
Термическая обработка стали заключается в закалке (нагревании до 800 °С, быстром охлаждении в масле) и затем в отпуске в свинцовой ванне (при 500 °С). В результате такой обработки искажается кристаллическая решетка и создаются препятствия движению дислокаций. Наличие препятствий приводит к повышению плотности и, следовательно, оказывает влияние на интенсивность упрочнения. В результате термической обработки повышается растворимость легирующих элементов стали, что также отражается на её прочности.
Следует отметить, что термически обработанная сталь обладает большей пластичностью по сравнению с холоднообработанной.
От действия многократно повторяющейся нагрузки возможно усталостное разрушение арматуры при пониженном сопротивлении растяжению.
Для исследования сопротивления арматуры при переменных напряжениях на основании опытов строят кривую выносливости. По оси абсцисс откладывают число миллионов циклов нагрузки и разгрузки N, а по оси ординат — наибольшее значение периодически изменяющегося напряжения арматуры os. С увеличением N уменьшается os при разрушении. Начиная с 2 * 106 циклов кривая выносливости стали имеет горизонтальный участок.
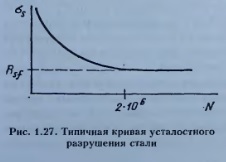
Предел прочности стальной арматуры при действии многократно повторяющейся нагрузки называют пределом выносливости (напряжение, соответствующее горизонтальному участку кривой выносливости).
В обычных железобетонных конструкциях характеристика перепада напряжений в рабочей арматуре ps колеблется, как правило, в пределах 0,1...0,4, в предварительно напряженных — в пределах 0,7...0,9, т. е. условия работы рабочей арматуры в последних из-за относительно малого перепада напряжений более благоприятны.
Отличительные признаки разрушения стали от усталости — внезапность разрушения без значительных видимых деформаций по плоскости, перпендикулярной к оси образца, практически полное отсутствие шейки и своеобразный вид излома, состоящий из двух резко отличающихся друг от друга частей (гладкой и шероховатой).
Усталость металлов связывают со структурной неоднородностью и пластическими деформациями в микрообъемах. Циклическое нагружение такого поликристаллического конгломерата, как сталь, порождает в наиболее напряженных структурных звеньях возникновение малых локальных зон пластических деформаций, накапливающихся с возрастанием числа циклов и приводящих к деформационному упрочнению. Их увеличение до критических значений, свойственных данному конкретному виду стали, приводит к зарождению и постепенному развитию трещин с последующим преимущественным прорастанием одной главной трещины и быстрым окончательным разрушением — разрывом образца.
Зарождение трещин происходит уже на начальных стадиях испытания, по истечении 5... 10% общего времени испытания. Все остальное время происходит их постепенное развитие. Места образования трещин называют очагами усталости. Обычно трещины образуются на поверхности, где концентрация напряжений наиболее значительна.
Существенную концентрацию напряжений на поверхности арматуры при работе на циклические нагрузки создает, к сожалению, периодический профиль, столь эффективный с точки зрения обеспечения ее совместной работы с бетоном (первые трещины возникают во впадинах у пересечения продольных и поперечных ребер, где концентрация напряжений наиболее значительна). Причем, с увеличением прочностных показателей стали ее чувствительность к концентраторам напряжений повышается и в результате предел выносливости остается практически постоянным. При упрочнении арматурной стали термической обработкой дополнительно возникают остаточные напряжения, что также отражается на относительном предел выносливости. Понижают предел выносливости и различные виды сварки, что связано с резким изменением геометрической формы, микроструктуры стали и возникновением остаточных напряжений.
Голышев А.Б., Бачинский В.Я., Полищук В.П., Железобетонные конструкции, Киев, 2001